Explosion-proof electric clamp butterfly valves play a pivotal role in safeguarding industrial processes where explosive gases or liquids are present. These valves are essential components in industries such as petrochemical, oil and gas, and chemical manufacturing, where the potential for explosions poses a significant risk to both personnel and equipment. In this article, we will delve into the key features and advantages of explosion-proof electric clamp butterfly valves, highlighting their crucial role in ensuring safety and efficiency.
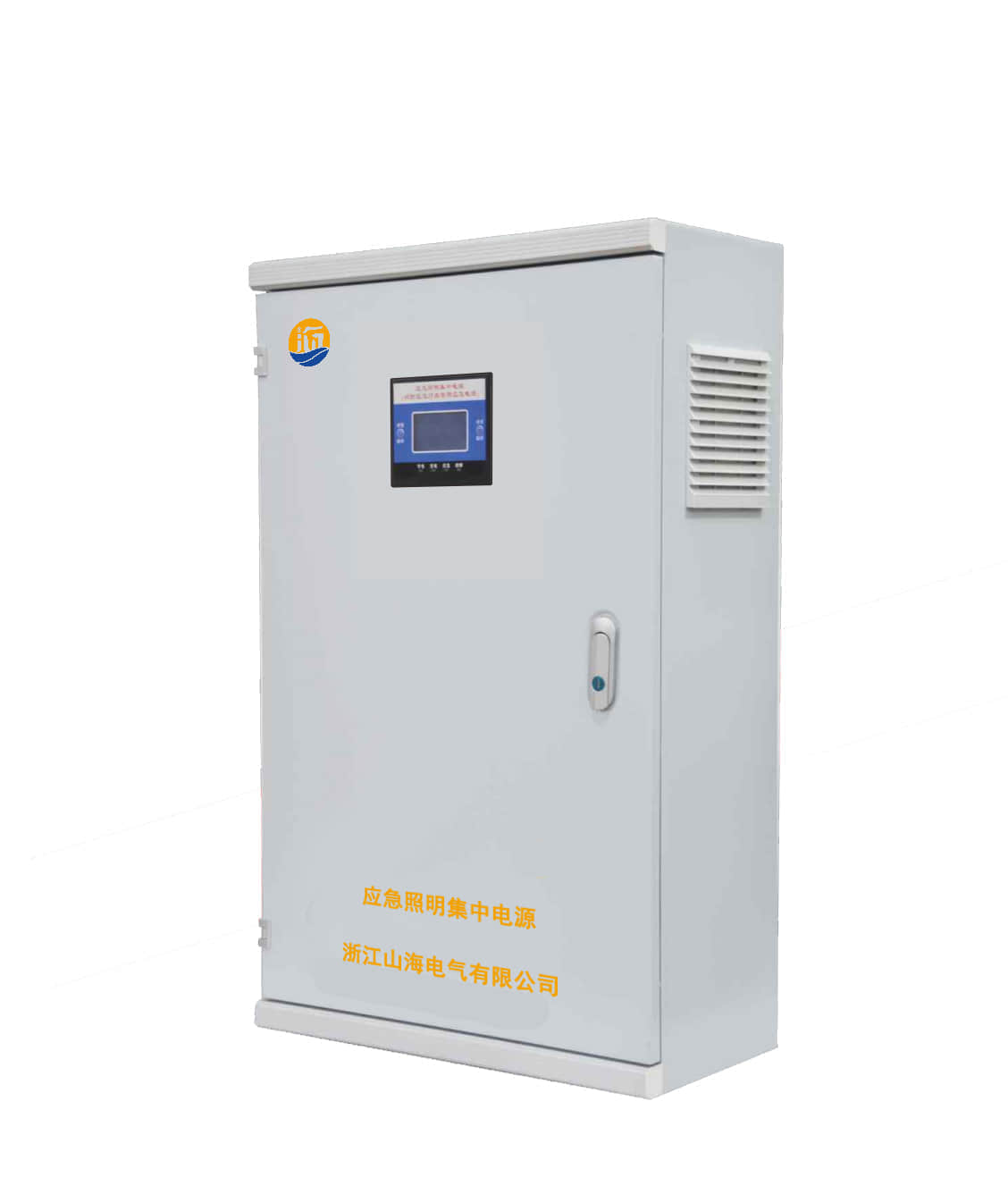
1. Understanding the Basics Explosion-proof electric clamp butterfly valves are designed to prevent explosions by containing and controlling the flow of flammable substances. They are constructed with robust materials that can withstand the pressure and temperature conditions typical of these industries. The butterfly valve mechanism itself consists of a rotating disc, or "butterfly," that controls the flow of fluids through the valve. This design allows for precise control over the flow rate, making it an ideal choice for various applications.
2. Key Features
One of the primary features that make explosion-proof electric clamp butterfly valves stand out is their ability to withstand high-pressure environments. These valves are equipped with reinforced seals and gaskets, ensuring a tight and secure closure even under extreme conditions. Additionally, they are designed to be electrically operated, allowing for remote control and automation, reducing the risk of human error and minimizing exposure to hazardous environments.
Furthermore, explosion-proof electric clamp butterfly valves are often equipped with explosion-proof enclosures and components. This feature prevents sparks, arcs, or high temperatures generated within the valve from igniting flammable gases or liquids in the surrounding atmosphere. In the event of a potentially dangerous situation, these valves can quickly shut off, preventing the escalation of an explosion.
3. Advantages
The advantages of using explosion-proof electric clamp butterfly valves are numerous:
Enhanced Safety:These valves are specifically engineered to reduce the risk of explosions, safeguarding both personnel and equipment.
Efficiency:The electric operation allows for precise control, leading to improved efficiency in processes and reduced waste.
Remote Operation:Operators can control these valves from a safe distance, reducing exposure to hazardous environments.
Reliability:The robust construction and explosion-proof features ensure the longevity and reliability of these valves, even in harsh conditions.
4. Applications
Explosion-proof electric clamp butterfly valves find applications in a wide range of industries, including:
Oil and Gas:These valves are used to control the flow of flammable hydrocarbons, ensuring safe and efficient extraction, processing, and transport.
Petrochemical:In chemical processing plants, these valves help manage the flow of volatile chemicals, preventing accidents and maintaining process integrity.
Mining:In mining operations where explosive gases may be present, these valves are crucial for safety and ventilation control.
Pharmaceuticals:Even in pharmaceutical manufacturing, where precision and sterility are essential, these valves can play a role in controlling the flow of volatile substances.
5. Conclusion
Explosion-proof electric clamp butterfly valves are indispensable in industries where safety and efficiency are paramount. Their robust construction, remote operation capabilities, and explosion-proof features make them a vital component in safeguarding processes that involve explosive gases or liquids. As technology continues to advance, these valves will play an increasingly critical role in ensuring the safety and success of various industrial operations.
标题:"Enhancing Industrial Safety with Explosion-Proof Pneumatic Ball Valves"
In industrial settings where the presence of explosive gases or flammable liquids poses a constant threat, safety is paramount. Explosion-proof pneumatic ball valves are critical components in ensuring that these environments remain secure and efficient. In this article, we will explore the essential features and advantages of explosion-proof pneumatic ball valves, shedding light on their indispensable role in safeguarding both personnel and equipment.
1. A Primer on Explosion-Proof Pneumatic Ball Valves
Explosion-proof pneumatic ball valves are engineered to mitigate the risk of explosions by controlling the flow of hazardous substances effectively. These valves are designed with materials that can withstand the high-pressure and high-temperature conditions typically encountered in industries such as petrochemical, oil and gas, and chemical manufacturing. The core mechanism of a ball valve consists of a spherical disc that regulates the flow of fluids through the valve, offering precise control and versatility for various applications.
2. Key Features
Explosion-proof pneumatic ball valves possess several critical features that make them indispensable in hazardous environments:
Robust Construction:These valves are built to withstand extreme conditions, including corrosive substances, high pressures, and wide temperature ranges. This ensures their longevity and reliability.
Explosion-Proof Design:The valves incorporate explosion-proof enclosures and components that prevent sparks, arcs, or heat generated within the valve from igniting flammable gases or liquids in the surrounding atmosphere.
Pneumatic Actuation:The valves are pneumatically operated, allowing for remote control and automation. This minimizes the risk of human exposure to dangerous environments and enhances operational efficiency.
Precise Flow Control:The ball valve design enables precise regulation of flow rates, making them suitable for a wide range of applications.
3. Advantages
Explosion-proof pneumatic ball valves offer several advantages:
Safety Enhancement:Their primary function is to reduce the risk of explosions, safeguarding both personnel and equipment. By swiftly closing in the event of a hazardous situation, they prevent further escalation.
Operational Efficiency:Remote pneumatic operation enables precise control of fluid flow, optimizing industrial processes and minimizing waste.
Longevity and Reliability:The valves are constructed with durability in mind, ensuring they perform consistently under harsh conditions.
4. Applications
Explosion-proof pneumatic ball valves find applications across various industries, including:
Oil and Gas:These valves are instrumental in controlling the flow of flammable hydrocarbons during extraction, processing, and transportation.
Petrochemical:Chemical processing plants use these valves to manage the flow of volatile chemicals safely, maintaining operational integrity.
Mining:In mining operations, where explosive gases may be present, these valves are crucial for safety and ventilation control.
Pharmaceuticals:Even in pharmaceutical manufacturing, where precision and sterility are essential, these valves contribute to the safe handling of potentially hazardous substances.
5. Conclusion
Explosion-proof pneumatic ball valves play a pivotal role in industries where safety and efficiency are paramount. Their robust construction, pneumatic operation, and explosion-proof design make them indispensable components for managing the flow of hazardous substances. As industrial technology continues to advance, these valves will remain crucial in safeguarding processes and ensuring the safety and success of various industrial operations.
标题:"Enhancing Safety and Efficiency with Explosion-Proof Electric Screw Ball Valves"
Explosion-proof electric screw ball valves are indispensable components in industries where the presence of explosive gases or flammable liquids demands uncompromising safety measures. These valves play a pivotal role in preventing catastrophic accidents and ensuring operational efficiency. In this article, we will delve into the key features and advantages of explosion-proof electric screw ball valves, shedding light on their crucial role in safeguarding industrial processes.
1. Unveiling the Essentials
Explosion-proof electric screw ball valves are meticulously designed to mitigate the risk of explosions by precisely regulating the flow of hazardous substances. They are engineered with durable materials capable of withstanding the extreme pressures and temperatures often encountered in industries such as petrochemical, oil and gas, and chemical manufacturing. At the heart of these valves lies a screw mechanism that controls the flow of fluids, providing precise flow regulation for a wide array of applications.
2. Key Features
The following key features set explosion-proof electric screw ball valves apart as vital components in hazardous environments:
Robust Build:These valves are constructed to withstand harsh conditions, including corrosive substances, high pressures, and temperature fluctuations, ensuring their longevity and reliability.
Explosion-Proof Design:Incorporating explosion-proof enclosures and components, these valves prevent the ignition of flammable gases or liquids in the surrounding atmosphere, even in situations where sparks, arcs, or heat are generated within the valve.
Electric Operation:Electric actuation enables remote control and automation, minimizing the risk of human exposure to hazardous environments and optimizing operational efficiency.
Precise Flow Control:The screw ball valve design allows for meticulous regulation of flow rates, making them versatile and adaptable to a wide range of applications.
3. Advantages
Explosion-proof electric screw ball valves offer several advantages:
Enhanced Safety:Their primary function is to reduce the risk of explosions, safeguarding both personnel and equipment. Swift closure during hazardous situations prevents further escalation.
Operational Efficiency:Electric actuation enables precise control of fluid flow, optimizing industrial processes and minimizing waste.
Longevity and Reliability:These valves are designed for durability, ensuring consistent performance under harsh conditions.
4. Applications
Explosion-proof electric screw ball valves find applications in various industries, including:
Oil and Gas:In the oil and gas sector, these valves regulate the flow of flammable hydrocarbons during extraction, processing, and transportation.
Petrochemical:Chemical processing plants rely on these valves to manage the flow of volatile chemicals safely, maintaining operational integrity.
Mining:These valves are crucial for safety and ventilation control in mining operations where explosive gases may be present.
Pharmaceuticals:Even in pharmaceutical manufacturing, where precision and sterility are paramount, these valves contribute to the safe handling of potentially hazardous substances.
5. Conclusion
Explosion-proof electric screw ball valves are instrumental in industries where safety and efficiency are non-negotiable. Their robust construction, electric operation, and explosion-proof design make them indispensable components for handling hazardous substances. As industrial technology continues to advance, these valves will remain vital in safeguarding processes and ensuring the safety and success of various industrial operations.
标题:"Enhancing Safety and Precision with Explosion-Proof Electric Diaphragm Regulating Valves"
In industries where the presence of explosive gases or flammable liquids is a constant concern, safety and precision are paramount. Explosion-proof electric diaphragm regulating valves have emerged as crucial components to ensure the security and efficiency of these environments. In this article, we will delve into the key features and advantages of explosion-proof electric diaphragm regulating valves, shedding light on their indispensable role in safeguarding industrial processes.
1. Understanding the Basics
Explosion-proof electric diaphragm regulating valves are meticulously engineered to minimize the risk of explosions by precisely controlling the flow of hazardous substances. They are crafted with durable materials capable of withstanding the high pressures and extreme temperatures often encountered in industries such as petrochemicals, oil and gas, and chemical manufacturing. The core mechanism of these valves is a diaphragm that flexes to regulate fluid flow, providing precise control and adaptability for a wide range of applications.
2. Key Features
Explosion-proof electric diaphragm regulating valves possess several key features that distinguish them as vital components in hazardous environments:
Sturdy Construction:These valves are designed to endure harsh conditions, including exposure to corrosive substances, high pressures, and temperature variations, ensuring their longevity and reliability.
Explosion-Proof Design:Incorporating explosion-proof enclosures and components, these valves prevent the ignition of flammable gases or liquids in the surrounding atmosphere. They are equipped to handle situations where sparks, arcs, or heat may be generated within the valve.
Electric Operation:Electric actuation enables remote control and automation, reducing the risk of human exposure to hazardous environments while enhancing operational efficiency.
Precise Flow Control:Diaphragm regulating valves allow for precise regulation of flow rates, making them adaptable to a wide variety of applications.
3. Advantages
Explosion-proof electric diaphragm regulating valves offer numerous advantages:
Enhanced Safety:Their primary function is to mitigate the risk of explosions, thereby safeguarding both personnel and equipment. Swift closure during hazardous situations prevents the escalation of potential disasters.
Operational Efficiency:Electric actuation facilitates precise control of fluid flow, optimizing industrial processes and minimizing waste.
Longevity and Reliability:These valves are constructed for durability, ensuring consistent performance under demanding conditions.
4. Applications
Explosion-proof electric diaphragm regulating valves find applications across various industries, including:
Oil and Gas:In the oil and gas sector, these valves are crucial for regulating the flow of flammable hydrocarbons during extraction, processing, and transportation.
Petrochemical:Chemical processing plants rely on these valves to safely manage the flow of volatile chemicals, maintaining operational integrity.
Mining:These valves play a critical role in safety and ventilation control in mining operations where explosive gases may be present.
Pharmaceuticals:Even in pharmaceutical manufacturing, where precision and sterility are essential, these valves contribute to the safe handling of potentially hazardous substances.
5. Conclusion
Explosion-proof electric diaphragm regulating valves are essential in industries where safety and precision are non-negotiable. Their robust construction, electric operation, and explosion-proof design make them indispensable for handling hazardous substances. As industrial technology continues to advance, these valves will remain pivotal in safeguarding processes and ensuring the safety and success of various industrial operations.
标题:"Securing Industrial Safety with Explosion-Proof Lithium Battery Valves"
In today's industrial landscape, safety is paramount, especially in environments where explosive gases or flammable liquids are present. Explosion-proof lithium battery valves have become vital components to ensure safety and reliability in such settings. In this article, we will explore the essential features and advantages of explosion-proof lithium battery valves, highlighting their crucial role in safeguarding industrial processes.
1. Unveiling the Essentials
Explosion-proof lithium battery valves are meticulously designed to minimize the risk of explosions by controlling the flow of hazardous substances with precision. They are crafted with robust materials capable of withstanding the extreme pressures and temperatures often encountered in industries like petrochemicals, oil and gas, and chemical manufacturing. The core mechanism of these valves consists of a battery-powered system that regulates fluid flow, offering precise control and adaptability for various applications.
2. Key Features
Explosion-proof lithium battery valves possess several key features that set them apart as vital components in hazardous environments:
Sturdy Construction:These valves are designed to endure harsh conditions, including exposure to corrosive substances, high pressures, and temperature fluctuations. This ensures their longevity and reliability.
Explosion-Proof Design:They incorporate explosion-proof enclosures and components, effectively preventing the ignition of flammable gases or liquids in the surrounding atmosphere. These valves are well-equipped to handle situations where sparks, arcs, or heat may be generated within the valve.
Battery-Powered Operation:Battery-driven systems enable remote control and automation, reducing the risk of human exposure to hazardous environments while enhancing operational efficiency.
Precise Flow Control:Lithium battery valves allow for precise regulation of flow rates, making them versatile and adaptable to a wide range of applications.
3. Advantages
Explosion-proof lithium battery valves offer several advantages:
Enhanced Safety:Their primary function is to mitigate the risk of explosions, safeguarding both personnel and equipment. In hazardous situations, they can swiftly close, preventing further escalation.
Operational Efficiency:Battery-powered operation facilitates precise control of fluid flow, optimizing industrial processes and minimizing waste.
Longevity and Reliability:These valves are constructed for durability, ensuring consistent performance under demanding conditions.
4. Applications
Explosion-proof lithium battery valves find applications across various industries, including:
Oil and Gas:In the oil and gas sector, these valves are crucial for regulating the flow of flammable hydrocarbons during extraction, processing, and transportation.
Petrochemical:Chemical processing plants rely on these valves to safely manage the flow of volatile chemicals, maintaining operational integrity.
Mining:These valves play a critical role in safety and ventilation control in mining operations where explosive gases may be present.
Pharmaceuticals:Even in pharmaceutical manufacturing, where precision and sterility are essential, these valves contribute to the safe handling of potentially hazardous substances.
5. Conclusion
Explosion-proof lithium battery valves are essential in industries where safety and precision are non-negotiable. Their robust construction, battery-powered operation, and explosion-proof design make them indispensable for handling hazardous substances. As industrial technology continues to advance, these valves will remain pivotal in safeguarding processes and ensuring the safety and success of various industrial operations.
标题:"The Power of Precision: Exploring Electric Actuators"
Electric actuators are indispensable devices that play a crucial role in various industries, from manufacturing to automation. These electromechanical devices are designed to convert electrical energy into mechanical motion, enabling precise control and automation of a wide range of applications. In this article, we will delve into the fundamentals, key features, and diverse applications of electric actuators, highlighting their significance in today's technological landscape.
Understanding Electric Actuators
Electric actuators are devices that transform electrical energy into mechanical movement. They provide controlled and precise linear or rotary motion, making them valuable components in numerous industrial processes. Unlike hydraulic or pneumatic actuators, electric actuators do not rely on fluid power, making them more suitable for specific applications where cleanliness, precision, and ease of control are essential.
Key Features of Electric Actuators
Electric actuators offer a range of features and benefits that make them highly desirable in various industries:
Precision Control:Electric actuators allow for precise control over movement, with the ability to stop at specific positions accurately. This precision is crucial in applications such as robotics and manufacturing.
Energy Efficiency:They are energy-efficient since they only consume power when in operation, unlike pneumatic systems that constantly require compressed air.
Clean and Quiet:Electric actuators produce minimal noise and do not require hydraulic fluids, making them a cleaner and quieter alternative.
Compact Design:Electric actuators often have a compact form factor, making them suitable for applications with limited space.
Maintenance-Friendly:They have lower maintenance requirements compared to hydraulic or pneumatic systems, reducing downtime and operating costs.
Applications of Electric Actuators
Electric actuators find applications in a wide range of industries, including:
Manufacturing:Electric actuators are used in assembly lines, CNC machinery, and robotics to precisely control movement, improving production efficiency and product quality.
Automotive:They play a critical role in various automotive systems, such as power windows, seat adjustments, and engine control.
Aerospace:Electric actuators are used in aircraft systems for functions like wing flap control and landing gear deployment.
Medical Devices:In medical equipment, such as surgical robots and diagnostic instruments, electric actuators enable precise movement and control.
Valve Control:Electric actuators are employed in the control of valves in industrial processes, ensuring accurate fluid flow regulation.
Renewable Energy:In wind turbines and solar tracking systems, electric actuators help optimize the positioning of components for maximum energy capture.
Home Automation:Electric actuators are used in home automation systems for functions like smart blinds, thermostats, and door locks.
Future Trends in Electric Actuation
As technology advances, electric actuators continue to evolve. Some emerging trends in electric actuation include:
Integration with IoT:Electric actuators are being integrated into the Internet of Things (IoT) ecosystem, allowing for remote monitoring and control.
Enhanced Efficiency:Ongoing research focuses on improving the energy efficiency and performance of electric actuators.
Miniaturization:Smaller and more compact electric actuators are being developed for applications in micro-robotics and medical devices.
Increased Connectivity:Electric actuators are becoming more interconnected, enabling seamless communication with other devices and systems.
In conclusion, electric actuators are versatile and essential components that empower industries with precise control and automation capabilities. Their clean and efficient operation, coupled with their adaptability to various applications, positions them as integral components in modern technology and industry. As technology continues to advance, electric actuators are expected to play an even more prominent role in shaping the future of automation and control systems.
标题:"Elevating Fluid Control: The Versatility of Stainless Steel Electric Ball Valves"
Stainless steel electric ball valves represent a significant advancement in fluid control technology, offering a wide range of applications across industries. Their durability, reliability, and precise control make them indispensable components in processes where fluid regulation is critical. In this article, we will explore the fundamentals, key features, and diverse applications of stainless steel electric ball valves, shedding light on their importance in modern engineering.
Understanding Stainless Steel Electric Ball Valves
Stainless steel electric ball valves are a type of quarter-turn valve that uses a spherical closure (the ball) to control the flow of fluids. These valves are specifically designed with a stainless steel body, making them resistant to corrosion, chemicals, and extreme temperatures. Electric actuators are integrated into the valve to enable remote control and automation, providing precise positioning of the ball to regulate fluid flow.
Key Features of Stainless Steel Electric Ball Valves
Stainless steel electric ball valves offer several features that make them highly valuable in fluid control systems:
Corrosion Resistance:The stainless steel construction ensures resistance to corrosion and chemical reactions, making these valves suitable for various aggressive environments.
Durability:Stainless steel is known for its robustness and longevity, ensuring the valve's reliability and extended service life.
Precise Control:Electric actuators allow for precise control of the ball's position, enabling accurate regulation of fluid flow rates.
Automation:The electric actuation feature enables remote operation, reducing the need for manual adjustments and improving process efficiency.
Versatility:These valves can handle a wide range of fluids, including water, gas, and corrosive chemicals, making them versatile across industries.
Applications of Stainless Steel Electric Ball Valves
Stainless steel electric ball valves find applications in numerous industries, including:
Oil and Gas:These valves are used to control the flow of crude oil, natural gas, and various chemicals in upstream and downstream processes.
Petrochemical:In chemical processing plants, stainless steel electric ball valves regulate the flow of corrosive substances and ensure operational safety.
Water Treatment:Municipal water treatment facilities use these valves to manage the flow of water, chemicals, and wastewater.
Food and Beverage:Stainless steel electric ball valves are employed in food and beverage processing to control the flow of liquids, including beverages, dairy products, and sauces.
Pharmaceutical:In pharmaceutical manufacturing, these valves play a crucial role in controlling the flow of pharmaceutical liquids and maintaining sterility.
Power Generation:In power plants, these valves are utilized in controlling cooling water, steam, and various fluids in energy production processes.
Advancements in Stainless Steel Electric Ball Valves
Stainless steel electric ball valves continue to evolve with technological advancements. Some emerging trends and developments in this field include:
Smart Valves:Integration with IoT technology enables real-time monitoring and data collection, enhancing predictive maintenance and efficiency.
Improved Materials:Ongoing research focuses on developing advanced stainless steel alloys with even greater resistance to corrosion and wear.
Energy Efficiency:Manufacturers are working to reduce energy consumption and increase the energy efficiency of electric actuators.
Miniaturization:Smaller, compact stainless steel electric ball valves are being developed for applications with limited space.
In conclusion, stainless steel electric ball valves have revolutionized fluid control systems with their durability, reliability, and precision. Their resistance to corrosion and chemicals, coupled with the capability for remote operation, makes them essential components in a wide range of industries. As technology continues to advance, these valves are expected to play an increasingly pivotal role in ensuring the efficiency and safety of fluid control processes.
标题:"Revolutionizing Fluid Control: The Versatility of Stainless Steel Electric Screw Ball Valves"
Stainless steel electric screw ball valves represent a significant advancement in fluid control technology, offering precision, reliability, and adaptability across industries. These valves, designed with a stainless steel body and an electrically actuated screw mechanism, play a pivotal role in processes where fluid regulation is paramount. In this article, we will delve into the fundamentals, key features, and diverse applications of stainless steel electric screw ball valves, highlighting their significance in modern engineering.
Understanding Stainless Steel Electric Screw Ball Valves
Stainless steel electric screw ball valves are quarter-turn valves that use a spherical closure (the ball) to control fluid flow. Their stainless steel construction not only makes them resistant to corrosion and chemicals but also ensures durability in harsh environments. These valves incorporate an electrically operated screw mechanism, which precisely positions the ball to regulate the flow of liquids or gases.
Key Features of Stainless Steel Electric Screw Ball Valves
Stainless steel electric screw ball valves offer a host of features that make them highly sought after in fluid control systems:
Corrosion Resistance:The stainless steel body ensures immunity to corrosion and chemical reactions, making these valves suitable for aggressive and corrosive environments.
Durability:Stainless steel's inherent robustness guarantees the valve's longevity, ensuring reliable performance over an extended service life.
Precision Control:Electric actuators precisely control the screw mechanism, allowing for accurate and repeatable regulation of fluid flow rates.
Automation:Electric actuation enables remote operation, reducing the need for manual adjustments and enhancing process efficiency.
Versatility:Stainless steel electric screw ball valves can handle a wide range of fluids, including water, chemicals, and gases, making them adaptable across industries.
Applications of Stainless Steel Electric Screw Ball Valves
Stainless steel electric screw ball valves find applications in numerous industries, including but not limited to:
Oil and Gas:These valves are employed to control the flow of crude oil, natural gas, and various chemicals in the extraction, processing, and transportation of hydrocarbons.
Petrochemical:Chemical processing plants rely on these valves to regulate the flow of corrosive substances and ensure operational safety.
Water Treatment:Municipal and industrial water treatment facilities use these valves to manage the flow of water, chemicals, and wastewater.
Food and Beverage:Stainless steel electric screw ball valves are utilized in the food and beverage industry to control the flow of liquids, including beverages, dairy products, and sauces.
Pharmaceutical:In pharmaceutical manufacturing, these valves play a crucial role in controlling the flow of pharmaceutical liquids and maintaining sterility.
Power Generation:Power plants employ these valves to control cooling water, steam, and various fluids in energy production processes.
Advancements in Stainless Steel Electric Screw Ball Valves
The field of stainless steel electric screw ball valves continues to evolve, driven by technological advancements and industry demands. Notable trends and developments include:
Smart Valves:Integration with IoT technology allows for real-time monitoring, data collection, and predictive maintenance, enhancing operational efficiency.
Improved Materials:Ongoing research focuses on developing advanced stainless steel alloys with enhanced resistance to corrosion and wear.
Energy Efficiency:Manufacturers are working to reduce energy consumption and increase the energy efficiency of electric actuators.
Compact Design:Smaller, more compact stainless steel electric screw ball valves are being developed to accommodate applications with limited space.
In conclusion, stainless steel electric screw ball valves have revolutionized fluid control systems with their durability, precision, and adaptability. Their resistance to corrosion and chemicals, coupled with the capability for remote operation, positions them as indispensable components in a wide range of industries. As technology continues to advance, these valves are expected to play an increasingly pivotal role in ensuring the efficiency and safety of fluid control processes.
标题:"Precise Control and Durability: Stainless Steel Electric Diaphragm Regulating Valves"
Stainless steel electric diaphragm regulating valves are at the forefront of fluid control technology, offering precision, versatility, and longevity in diverse industrial applications. These valves, constructed with a stainless steel body and an electrically actuated diaphragm, play a vital role in processes where accurate fluid regulation is essential. In this article, we will explore the fundamental principles, key features, and wide-ranging applications of stainless steel electric diaphragm regulating valves, highlighting their pivotal role in modern engineering.
Understanding Stainless Steel Electric Diaphragm Regulating Valves
Stainless steel electric diaphragm regulating valves are designed to control fluid flow accurately by utilizing an electrically actuated diaphragm. The valve body is crafted from stainless steel, ensuring resistance to corrosion and chemicals, while the electric actuation system enables precise positioning of the diaphragm for flow control.
Key Features of Stainless Steel Electric Diaphragm Regulating Valves
These valves offer a host of features that make them highly desirable in fluid control systems:
Corrosion Resistance:The stainless steel construction ensures the valve's durability and resistance to corrosion, making it suitable for harsh and corrosive environments.
Durability:Stainless steel's inherent robustness guarantees the valve's longevity, ensuring reliable performance over an extended service life.
Precise Control:Electric actuators precisely position the diaphragm, enabling accurate and repeatable regulation of fluid flow rates.
Automation:Electric actuation enables remote operation, reducing the need for manual adjustments and enhancing process efficiency.
Versatility:Stainless steel electric diaphragm regulating valves are capable of handling a wide range of fluids, including water, chemicals, and gases, making them adaptable across industries.
Applications of Stainless Steel Electric Diaphragm Regulating Valves
These valves find applications in various industries, including but not limited to:
Water Treatment:Municipal and industrial water treatment facilities utilize these valves to manage the flow of water, chemicals, and wastewater.
Chemical Manufacturing:These valves are crucial in chemical processing plants to regulate the flow of corrosive and hazardous chemicals, ensuring safety and process integrity.
Pharmaceuticals:In pharmaceutical manufacturing, these valves play a vital role in controlling the flow of pharmaceutical liquids and maintaining sterility.
Food and Beverage:The food and beverage industry employs stainless steel electric diaphragm regulating valves to control the flow of liquids, including beverages, dairy products, and sauces.
Power Generation:Power plants use these valves for precise control of cooling water, steam, and various fluids in energy production processes.
Advancements in Stainless Steel Electric Diaphragm Regulating Valves
The field of stainless steel electric diaphragm regulating valves continues to evolve to meet emerging industry demands. Notable trends and developments include:
Smart Valves:Integration with IoT technology enables real-time monitoring, data collection, and predictive maintenance, enhancing operational efficiency.
Enhanced Materials:Ongoing research focuses on developing advanced stainless steel alloys with superior resistance to corrosion and wear.
Energy Efficiency:Manufacturers are working to reduce energy consumption and enhance the energy efficiency of electric actuators.
Compact Design:Smaller, more compact stainless steel electric diaphragm regulating valves are being developed to accommodate applications with limited space.
In conclusion, stainless steel electric diaphragm regulating valves are pivotal in fluid control systems, offering precision, durability, and adaptability. Their resistance to corrosion and chemicals, coupled with the capability for remote operation, positions them as indispensable components across various industries. As technology continues to advance, these valves are expected to play an increasingly pivotal role in ensuring the efficiency and safety of fluid control processes.
标题:"Precision and Reliability: The Advantages of Stainless Steel Mounted Electric Eccentric Half Ball Valves"
Stainless steel mounted electric eccentric half ball valves represent a significant leap in fluid control technology, offering precision, durability, and versatility in various industrial applications. These valves, featuring a stainless steel construction and an electrically actuated eccentric half ball, play a pivotal role in processes requiring accurate fluid regulation. In this article, we will explore the fundamental principles, key features, and wide-ranging applications of stainless steel mounted electric eccentric half ball valves, emphasizing their crucial role in modern engineering.
Understanding Stainless Steel Mounted Electric Eccentric Half Ball Valves
Stainless steel mounted electric eccentric half ball valves are designed to control fluid flow accurately by employing an electrically actuated eccentric half ball. The valve body is constructed from stainless steel, ensuring resistance to corrosion and chemicals, while the electric actuation system precisely positions the eccentric half ball for flow control.
Key Features of Stainless Steel Mounted Electric Eccentric Half Ball Valves
These valves offer a host of features that make them highly desirable in fluid control systems:
Corrosion Resistance:The stainless steel construction ensures the valve's durability and resistance to corrosion, making it suitable for harsh and corrosive environments.
Durability:Stainless steel's inherent robustness guarantees the valve's longevity, ensuring reliable performance over an extended service life.
Precise Control:Electric actuators accurately position the eccentric half ball, enabling precise and repeatable regulation of fluid flow rates.
Automation:Electric actuation enables remote operation, reducing the need for manual adjustments and enhancing process efficiency.
Versatility:Stainless steel mounted electric eccentric half ball valves are capable of handling a wide range of fluids, including water, chemicals, and gases, making them adaptable across industries.
Applications of Stainless Steel Mounted Electric Eccentric Half Ball Valves
These valves find applications in various industries, including but not limited to:
Water Treatment:Municipal and industrial water treatment facilities utilize these valves to manage the flow of water, chemicals, and wastewater.
Chemical Manufacturing:These valves are crucial in chemical processing plants to regulate the flow of corrosive and hazardous chemicals, ensuring safety and process integrity.
Pharmaceuticals:In pharmaceutical manufacturing, these valves play a vital role in controlling the flow of pharmaceutical liquids and maintaining sterility.
Food and Beverage:The food and beverage industry employs stainless steel mounted electric eccentric half ball valves to control the flow of liquids, including beverages, dairy products, and sauces.
Power Generation:Power plants use these valves for precise control of cooling water, steam, and various fluids in energy production processes.
Advancements in Stainless Steel Mounted Electric Eccentric Half Ball Valves
The field of stainless steel mounted electric eccentric half ball valves continues to evolve to meet emerging industry demands. Notable trends and developments include:
Smart Valves:Integration with IoT technology enables real-time monitoring, data collection, and predictive maintenance, enhancing operational efficiency.
Enhanced Materials:Ongoing research focuses on developing advanced stainless steel alloys with superior resistance to corrosion and wear.
Energy Efficiency:Manufacturers are working to reduce energy consumption and enhance the energy efficiency of electric actuators.
Compact Design:Smaller, more compact stainless steel mounted electric eccentric half ball valves are being developed to accommodate applications with limited space.
In conclusion, stainless steel mounted electric eccentric half ball valves are pivotal in fluid control systems, offering precision, durability, and adaptability. Their resistance to corrosion and chemicals, coupled with the capability for remote operation, positions them as indispensable components across various industries. As technology continues to advance, these valves are expected to play an increasingly pivotal role in ensuring the efficiency and safety of fluid control processes.
标题:"Powering Precision and Durability: Stainless Steel Electric Power Station Valves"
Stainless steel electric power station valves represent a cornerstone of modern energy infrastructure, offering precision control, durability, and reliability in critical power generation processes. These valves, designed with a stainless steel body and electric actuation systems, play a pivotal role in power stations where precise fluid control is paramount. In this article, we will explore the fundamentals, key features, and diverse applications of stainless steel electric power station valves, emphasizing their essential role in the energy sector.
Understanding Stainless Steel Electric Power Station Valves
Stainless steel electric power station valves are engineered to control the flow of fluids accurately and efficiently in power generation facilities. These valves are constructed with a stainless steel body, ensuring resistance to corrosion and high-temperature environments. Electric actuators are integrated into the valve design, enabling precise and automated control of fluid flow within power stations.
Key Features of Stainless Steel Electric Power Station Valves
Stainless steel electric power station valves offer a range of features that make them highly valuable in fluid control systems within power generation facilities:
Corrosion Resistance:The stainless steel construction ensures the valve's resistance to corrosion, even in aggressive environments, thereby enhancing its durability and longevity.
High-Temperature Performance:Stainless steel can withstand extreme temperatures, making these valves suitable for applications where heat is a significant factor.
Precise Control:Electric actuators enable precise positioning of the valve, ensuring accurate regulation of fluid flow rates and optimizing power generation processes.
Automation:Electric actuation allows for remote operation and automation, reducing the need for manual adjustments and enhancing overall operational efficiency.
Reliability:Stainless steel electric power station valves are renowned for their reliability, minimizing downtime and maintenance costs.
Applications of Stainless Steel Electric Power Station Valves
These valves find essential applications in various areas of power generation, including but not limited to:
Fossil Fuel Power Plants:In coal, natural gas, or oil-fired power stations, these valves are used to control the flow of steam, cooling water, and other fluids essential for energy production.
Nuclear Power Plants:Stainless steel electric power station valves play a critical role in nuclear facilities by regulating coolant flow to maintain reactor temperature and safety.
Hydropower Plants:These valves are employed in controlling water flow in hydropower plants, optimizing energy generation from flowing water.
Geothermal Power Plants:In geothermal facilities, these valves are used to regulate the flow of geothermal fluids, which are used to generate electricity.
Renewable Energy Systems:Valves are also utilized in renewable energy systems, such as solar thermal power plants, to control the flow of heat transfer fluids.
Advancements in Stainless Steel Electric Power Station Valves
The field of stainless steel electric power station valves continues to evolve in response to emerging industry demands. Some notable trends and developments include:
Smart Valves:Integration with IoT technology allows for real-time monitoring, data collection, and predictive maintenance, enhancing operational efficiency and safety.
Enhanced Materials:Ongoing research focuses on developing advanced stainless steel alloys with even greater resistance to corrosion and wear.
Energy Efficiency:Manufacturers are working to reduce energy consumption and increase the energy efficiency of electric actuators.
Digital Twin Technology:Digital twins of valves are being used for modeling and simulations to optimize valve performance and maintenance.
In conclusion, stainless steel electric power station valves are essential components in modern energy infrastructure, offering precision, durability, and reliability in power generation processes. Their resistance to corrosion, high-temperature performance, and automation capabilities make them indispensable in various power generation facilities. As technology continues to advance, these valves are expected to play an increasingly pivotal role in ensuring the efficiency and reliability of power generation operations.
标题:"Precision at High Temperatures: The Advantages of WCB Electric High-Temperature Ball Valves"
WCB electric high-temperature ball valves represent a remarkable innovation in fluid control technology, offering precision, durability, and reliability in high-temperature environments. These valves, constructed with a WCB (cast carbon steel) body and electric actuation systems, play a pivotal role in industries where precise fluid control under extreme temperatures is essential. In this article, we will explore the fundamentals, key features, and diverse applications of WCB electric high-temperature ball valves, emphasizing their critical role in modern engineering.
Understanding WCB Electric High-Temperature Ball Valves
WCB electric high-temperature ball valves are meticulously engineered to control fluid flow with precision in environments characterized by elevated temperatures. These valves feature a WCB (cast carbon steel) body, known for its strength and resistance to high temperatures. Electric actuators are integrated into the valve design, allowing for precise and automated control of fluid flow even in extreme heat.
Key Features of WCB Electric High-Temperature Ball Valves
WCB electric high-temperature ball valves offer a range of features that make them highly valuable in fluid control systems under high-temperature conditions:
High-Temperature Resistance:The WCB (cast carbon steel) construction ensures the valve's durability and resilience in extreme temperatures, making it suitable for applications where heat is a significant factor.
Precise Control:Electric actuators enable precise positioning of the valve, ensuring accurate regulation of fluid flow rates, even in the presence of high temperatures.
Automation:Electric actuation allows for remote operation and automation, reducing the need for manual adjustments and enhancing overall operational efficiency.
Reliability:WCB electric high-temperature ball valves are renowned for their reliability, minimizing downtime and maintenance costs in industries with demanding temperature requirements.
Applications of WCB Electric High-Temperature Ball Valves
These valves find essential applications in various industries where high-temperature fluid control is imperative, including:
Power Generation:In fossil fuel power plants, these valves are used to control the flow of high-temperature steam, ensuring efficient energy production.
Oil and Gas:In refineries and petrochemical facilities, these valves regulate the flow of high-temperature hydrocarbons, acids, and other corrosive substances.
Metallurgy:In steel mills and metallurgical processes, WCB electric high-temperature ball valves play a crucial role in controlling the flow of molten metals and high-temperature gases.
Chemical Manufacturing:These valves are employed to manage the flow of high-temperature and corrosive chemicals, ensuring safety and process integrity.
Automotive Manufacturing:In heat treatment processes, these valves control the flow of high-temperature gases for metal hardening and tempering.
Advancements in WCB Electric High-Temperature Ball Valves
The field of WCB electric high-temperature ball valves continues to evolve in response to emerging industry demands. Some notable trends and developments include:
Smart Valves:Integration with IoT technology allows for real-time monitoring, data collection, and predictive maintenance, enhancing operational efficiency and safety.
Enhanced Materials:Ongoing research focuses on developing advanced materials with even greater resistance to high temperatures and corrosion.
Energy Efficiency:Manufacturers are working to reduce energy consumption and increase the energy efficiency of electric actuators.
Digital Twin Technology:Digital twins of valves are being used for modeling and simulations to optimize valve performance and maintenance.
In conclusion, WCB electric high-temperature ball valves are critical components in modern industries where precise fluid control under extreme temperatures is a necessity. Their high-temperature resistance, precision control, and automation capabilities make them indispensable in applications where heat and reliability are of utmost importance. As technology continues to advance, these valves are expected to play an increasingly pivotal role in ensuring the efficiency and safety of high-temperature fluid control processes.
标题:"Efficiency and Reliability: The WCB Pneumatic Butterfly Valve"
WCB pneumatic butterfly valves represent a significant advancement in fluid control technology, offering efficiency, reliability, and versatility across industries. These valves, constructed with a WCB (cast carbon steel) body and pneumatic actuation systems, play a pivotal role in processes that demand precise fluid control. In this article, we will delve into the fundamentals, key features, and diverse applications of WCB pneumatic butterfly valves, emphasizing their critical role in modern engineering.
Understanding WCB Pneumatic Butterfly Valves
WCB pneumatic butterfly valves are engineered to control fluid flow accurately and efficiently in a wide range of applications. These valves feature a WCB (cast carbon steel) body known for its strength and resistance to corrosion. Pneumatic actuators are integrated into the valve design, allowing for precise control of the butterfly disc's position to regulate fluid flow.
Key Features of WCB Pneumatic Butterfly Valves
These valves offer a host of features that make them highly desirable in fluid control systems:
Corrosion Resistance:The WCB construction ensures the valve's durability and resistance to corrosion, making it suitable for applications involving aggressive fluids.
Efficiency:Pneumatic actuators enable rapid and efficient valve operation, reducing response times in critical processes.
Precision Control:Pneumatic actuation allows for precise positioning of the butterfly disc, ensuring accurate regulation of fluid flow rates.
Automation:Pneumatic butterfly valves can be easily integrated into automated systems, enhancing overall operational efficiency.
Reliability:These valves are known for their reliability and longevity, reducing downtime and maintenance costs.
Applications of WCB Pneumatic Butterfly Valves
WCB pneumatic butterfly valves find applications in various industries, including but not limited to:
Water Treatment:Municipal and industrial water treatment facilities use these valves to manage the flow of water, chemicals, and wastewater.
Chemical Manufacturing:These valves are essential in chemical processing plants to regulate the flow of corrosive and hazardous chemicals, ensuring safety and process integrity.
Oil and Gas:In refineries and petrochemical facilities, these valves control the flow of various fluids, including crude oil, natural gas, and refined products.
Pharmaceuticals:In pharmaceutical manufacturing, these valves play a crucial role in controlling the flow of pharmaceutical liquids and maintaining sterility.
Food and Beverage:The food and beverage industry employs WCB pneumatic butterfly valves to control the flow of liquids, including beverages, dairy products, and sauces.
Advancements in WCB Pneumatic Butterfly Valves
The field of WCB pneumatic butterfly valves continues to evolve to meet emerging industry demands. Some notable trends and developments include:
Smart Valves:Integration with IoT technology allows for real-time monitoring, data collection, and predictive maintenance, enhancing operational efficiency and safety.
Enhanced Materials:Ongoing research focuses on developing advanced materials with even greater resistance to corrosion and wear.
Energy Efficiency:Manufacturers are working to reduce energy consumption and increase the energy efficiency of pneumatic actuators.
Digital Twin Technology:Digital twins of valves are being used for modeling and simulations to optimize valve performance and maintenance.
In conclusion, WCB pneumatic butterfly valves are pivotal in fluid control systems, offering efficiency, reliability, and adaptability in various industries. Their resistance to corrosion, precision control, and automation capabilities make them indispensable components for processes that demand precise fluid regulation. As technology continues to advance, these valves are expected to play an increasingly pivotal role in ensuring the efficiency and safety of fluid control processes.
标题:"Clarity and Control: Exploring the WCB Electric Glass Valve"
WCB electric glass valves are a remarkable innovation in fluid control technology, offering precision, transparency, and versatility across a spectrum of industries. These valves, constructed with a WCB (cast carbon steel) body and electric actuation systems, play a pivotal role in processes where transparency and precise fluid control are paramount. In this article, we will delve into the fundamentals, key features, and diverse applications of WCB electric glass valves, emphasizing their critical role in modern engineering.
Understanding WCB Electric Glass Valves
WCB electric glass valves are engineered to control fluid flow accurately and transparently, making them suitable for applications where visibility of the fluid is crucial. These valves feature a WCB (cast carbon steel) body known for its strength and resistance to corrosion. Electric actuators are integrated into the valve design, allowing for precise control of fluid flow while offering the unique advantage of transparency through a glass body.
Key Features of WCB Electric Glass Valves
These valves offer a host of features that make them highly desirable in fluid control systems:
Corrosion Resistance:The WCB construction ensures the valve's durability and resistance to corrosion, making it suitable for applications involving aggressive fluids.
Transparency:The glass body of these valves provides operators with clear visibility of the fluid, allowing for easy inspection and monitoring of the process.
Precision Control:Electric actuators enable precise positioning of the valve, ensuring accurate regulation of fluid flow rates.
Automation:Electric actuation allows for remote operation and integration into automated systems, enhancing overall operational efficiency.
Reliability:These valves are known for their reliability and longevity, reducing downtime and maintenance costs.
Applications of WCB Electric Glass Valves
WCB electric glass valves find applications in various industries, including but not limited to:
Chemical Manufacturing:These valves are essential in chemical processing plants to regulate the flow of corrosive and hazardous chemicals while providing a visual confirmation of the process.
Pharmaceuticals:In pharmaceutical manufacturing, these valves play a crucial role in controlling the flow of pharmaceutical liquids and maintaining sterility, with the added benefit of transparency.
Food and Beverage:The food and beverage industry employs WCB electric glass valves to control the flow of liquids, including beverages, dairy products, and sauces, allowing operators to monitor product quality.
Laboratory and Research:Laboratories often use these valves in experimental setups where visual observation of fluid flow is necessary.
Advancements in WCB Electric Glass Valves
The field of WCB electric glass valves continues to evolve to meet emerging industry demands. Some notable trends and developments include:
Smart Valves:Integration with IoT technology allows for real-time monitoring, data collection, and predictive maintenance, enhancing operational efficiency and safety.
Enhanced Materials:Ongoing research focuses on developing advanced materials for the glass body, improving resistance to temperature and pressure variations.
Energy Efficiency:Manufacturers are working to reduce energy consumption and increase the energy efficiency of electric actuators.
Digital Twin Technology:Digital twins of valves are being used for modeling and simulations to optimize valve performance and maintenance.
In conclusion, WCB electric glass valves offer precision and transparency in fluid control, making them indispensable components in modern industries. Their unique combination of corrosion resistance, precision control, and transparency provides operators with a clear view of the process while ensuring the efficient and reliable regulation of fluid flow. As technology continues to advance, these valves are expected to play an increasingly pivotal role in processes that require both control and visibility.
标题:"Seamless Precision: The Evolution of Electric Stainless Steel Ball Valves"
Electric stainless steel ball valves represent a significant advancement in fluid control technology, offering precision, durability, and versatility across industries. These valves, constructed with a stainless steel body and electric actuation systems, play a pivotal role in processes where fluid regulation is critical. In this article, we will explore the fundamentals, key features, and diverse applications of electric stainless steel ball valves, shedding light on their importance in modern engineering.
Understanding Electric Stainless Steel Ball Valves
Electric stainless steel ball valves are quarter-turn valves that utilize a spherical closure (the ball) to control the flow of fluids. Their construction features a stainless steel body, which ensures resistance to corrosion, chemicals, and extreme temperatures. Electric actuators are integrated into the valve, enabling remote control and automation, providing precise positioning of the ball to regulate fluid flow.
Key Features of Electric Stainless Steel Ball Valves
Electric stainless steel ball valves offer several features that make them highly valuable in fluid control systems:
Corrosion Resistance:The stainless steel construction ensures the valve's resistance to corrosion and chemical reactions, making these valves suitable for various aggressive environments.
Durability:Stainless steel is known for its robustness and longevity, ensuring the valve's reliability and extended service life.
Precise Control:Electric actuators allow for precise control of the ball's position, enabling accurate regulation of fluid flow rates.
Automation:The electric actuation feature enables remote operation, reducing the need for manual adjustments and improving process efficiency.
Versatility:These valves can handle a wide range of fluids, including water, gas, and corrosive chemicals, making them versatile across industries.
Applications of Electric Stainless Steel Ball Valves
Electric stainless steel ball valves find applications in numerous industries, including:
Oil and Gas:These valves are used to control the flow of crude oil, natural gas, and various chemicals in upstream and downstream processes.
Petrochemical:In chemical processing plants, stainless steel electric ball valves regulate the flow of corrosive substances and ensure operational safety.
Water Treatment:Municipal water treatment facilities use these valves to manage the flow of water, chemicals, and wastewater.
Food and Beverage:Stainless steel electric ball valves are employed in food and beverage processing to control the flow of liquids, including beverages, dairy products, and sauces.
Pharmaceutical:In pharmaceutical manufacturing, these valves play a crucial role in controlling the flow of pharmaceutical liquids and maintaining sterility.
Power Generation:In power plants, these valves are utilized in controlling cooling water, steam, and various fluids in energy production processes.
Advancements in Electric Stainless Steel Ball Valves
Electric stainless steel ball valves continue to evolve with technological advancements. Some emerging trends and developments in this field include:
Smart Valves:Integration with IoT technology enables real-time monitoring and data collection, enhancing predictive maintenance and efficiency.
Improved Materials:Ongoing research focuses on developing advanced stainless steel alloys with even greater resistance to corrosion and wear.
Energy Efficiency:Manufacturers are working to reduce energy consumption and increase the energy efficiency of electric actuators.
Miniaturization:Smaller, compact stainless steel electric ball valves are being developed for applications with limited space.
In conclusion, electric stainless steel ball valves have revolutionized fluid control systems with their durability, reliability, and precision. Their resistance to corrosion and chemicals, coupled with the capability for remote operation, makes them essential components in a wide range of industries. As technology continues to advance, these valves are expected to play an increasingly pivotal role in ensuring the efficiency and safety of fluid control processes.
标题:"Precision and Control: Unveiling the WCB Electric Globe Valve"
WCB electric globe valves represent a significant advancement in fluid control technology, offering precision, reliability, and versatility in various industrial applications. These valves, constructed with a WCB (cast carbon steel) body and electric actuation systems, play a pivotal role in processes that require precise fluid control. In this article, we will explore the fundamentals, key features, and diverse applications of WCB electric globe valves, emphasizing their critical role in modern engineering.
Understanding WCB Electric Globe Valves
WCB electric globe valves are engineered to regulate fluid flow accurately and efficiently in a wide range of industrial applications. These valves feature a WCB (cast carbon steel) body known for its strength and resistance to corrosion. Electric actuators are integrated into the valve design, allowing for precise control of fluid flow through a globe-shaped disc that moves perpendicular to the flow direction.
Key Features of WCB Electric Globe Valves
These valves offer a host of features that make them highly valuable in fluid control systems:
Corrosion Resistance:The WCB construction ensures the valve's durability and resistance to corrosion, making it suitable for applications involving aggressive fluids.
Precise Control:Electric actuators enable precise positioning of the valve's globe-shaped disc, ensuring accurate regulation of fluid flow rates.
Automation:Electric actuation allows for remote operation and integration into automated systems, enhancing overall operational efficiency.
Versatility:WCB electric globe valves are capable of handling various fluids, including water, steam, and a range of chemicals, making them adaptable across industries.
Reliability:These valves are known for their reliability, minimizing downtime and maintenance costs.
Applications of WCB Electric Globe Valves
WCB electric globe valves find applications in various industries, including but not limited to:
Oil and Gas:In oil refineries and petrochemical plants, these valves are used to control the flow of crude oil, natural gas, and various chemicals in critical processes.
Power Generation:Power plants utilize these valves to control the flow of steam and other fluids in energy production and turbine systems.
Chemical Manufacturing:Chemical processing plants rely on WCB electric globe valves to regulate the flow of corrosive and hazardous chemicals, ensuring safety and process integrity.
Water Treatment:Municipal and industrial water treatment facilities use these valves to manage the flow of water, chemicals, and wastewater.
HVAC Systems:These valves are integrated into HVAC (heating, ventilation, and air conditioning) systems for precise control of heating and cooling fluids.
Advancements in WCB Electric Globe Valves
The field of WCB electric globe valves continues to evolve to meet emerging industry demands. Notable trends and developments include:
Smart Valves:Integration with IoT technology allows for real-time monitoring, data collection, and predictive maintenance, enhancing operational efficiency and safety.
Enhanced Materials:Ongoing research focuses on developing advanced materials for improved resistance to corrosion and wear.
Energy Efficiency:Manufacturers are working to reduce energy consumption and enhance the energy efficiency of electric actuators.
Digital Twin Technology:Digital twins of valves are used for modeling and simulations to optimize valve performance and maintenance.
In conclusion, WCB electric globe valves play a pivotal role in fluid control systems, offering precision, reliability, and adaptability in various industries. Their resistance to corrosion, precision control, and automation capabilities make them indispensable components in processes that require accurate fluid regulation. As technology continues to advance, these valves are expected to play an increasingly crucial role in ensuring the efficiency and safety of fluid control processes.
标题:"The Pinnacle of Precision: Exploring Electric Ball Valve Manufacturers"
Electric ball valves are critical components in fluid control systems, and the choice of manufacturer plays a pivotal role in determining the quality, reliability, and performance of these valves. Electric ball valve manufacturers are at the forefront of innovation, producing cutting-edge solutions for a wide range of industries. In this article, we will delve into the world of electric ball valve manufacturers, exploring their significance, key attributes, and the impact they have on modern engineering.
The Significance of Electric Ball Valve Manufacturers
Electric ball valve manufacturers are instrumental in meeting the growing demand for efficient fluid control solutions across various sectors. Their role extends beyond mere production; they are catalysts of innovation and engineering excellence. The importance of these manufacturers can be summarized in several key points:
Quality Assurance:Reputable manufacturers adhere to stringent quality control processes, ensuring that their electric ball valves meet industry standards and customer expectations for performance and reliability.
Customization:Manufacturers often provide tailored solutions, allowing customers to specify valve parameters, materials, and features to suit their unique applications.
Innovation:Manufacturers continuously invest in research and development to create valves that are more efficient, environmentally friendly, and adaptable to the evolving needs of industries.
Technical Expertise:Electric ball valve manufacturers employ skilled engineers and technicians who possess in-depth knowledge of fluid dynamics, materials science, and automation technology, ensuring the design and production of high-quality valves.
Support and Maintenance:Many manufacturers offer after-sales support, maintenance, and spare parts services, ensuring the longevity and performance of their products.
Key Attributes of Electric Ball Valve Manufacturers
When evaluating electric ball valve manufacturers, certain attributes set the industry leaders apart:
Experience:Established manufacturers often have a long history of producing valves, demonstrating their expertise and reliability in the field.
Quality Certifications:Recognized certifications, such as ISO 9001, are indicative of a manufacturer's commitment to quality and compliance with international standards.
Product Range:A diverse product portfolio allows manufacturers to cater to various industries, applications, and specifications.
Innovation:Leading manufacturers invest in research and development to introduce innovative features like smart valves with IoT connectivity, digital monitoring, and enhanced energy efficiency.
Global Reach:Manufacturers with a global presence can provide their products and services to customers worldwide, ensuring accessibility and timely support.
Applications and Industries
Electric ball valve manufacturers serve a wide range of industries, including but not limited to:
Oil and Gas:For controlling the flow of crude oil, natural gas, and various petrochemicals.
Water Treatment:In municipal and industrial facilities for managing water, wastewater, and chemical processes.
Chemical Manufacturing:For precise regulation of corrosive and hazardous chemicals in chemical processing plants.
Power Generation:In power plants for controlling steam, cooling water, and various fluids in energy production.
Pharmaceuticals:Ensuring the accuracy and sterility of pharmaceutical liquids in manufacturing processes.
The Future of Electric Ball Valve Manufacturers
As industries continue to advance and embrace automation and smart technologies, electric ball valve manufacturers are poised for further growth and innovation. Future trends may include:
IoT Integration:Greater connectivity for real-time monitoring, data collection, and predictive maintenance.
Enhanced Materials:Continued development of advanced materials for improved corrosion resistance and longevity.
Energy Efficiency:Ongoing efforts to reduce energy consumption and enhance the energy efficiency of electric actuators.
Sustainability:Manufacturers may focus on eco-friendly materials and processes to meet environmental goals.
In conclusion, electric ball valve manufacturers play an indispensable role in modern engineering, offering high-quality, customizable solutions for fluid control needs across diverse industries. Their commitment to quality, innovation, and technical expertise ensures the reliability and efficiency of fluid control systems, making them a cornerstone of industrial processes worldwide.
标题:"Masters of Precision: The World of Electric High-Temperature Ball Valve Manufacturers"
Electric high-temperature ball valve manufacturers are the architects of precision and reliability in fluid control systems operating under extreme heat. These manufacturers are instrumental in designing, producing, and delivering cutting-edge solutions that regulate fluid flow with precision and efficiency in industries where elevated temperatures are the norm. In this article, we will delve into the realm of electric high-temperature ball valve manufacturers, exploring their significance, key attributes, and the pivotal role they play in modern engineering.
The Significance of Electric High-Temperature Ball Valve Manufacturers
Electric high-temperature ball valve manufacturers are indispensable in fulfilling the growing demand for advanced fluid control solutions across various sectors. Their significance extends beyond the production line; they are the driving force behind innovation and engineering excellence. Here are some key points illustrating their importance:
Quality Assurance:Reputable manufacturers adhere to stringent quality control processes, ensuring that their electric high-temperature ball valves meet industry standards and customer expectations for performance and reliability, especially in extreme heat conditions.
Customization:Manufacturers often provide tailored solutions, allowing customers to specify valve parameters, materials, and features to suit their unique high-temperature applications.
Innovation:Manufacturers invest heavily in research and development to create valves that are not only more efficient but also capable of withstanding extreme temperatures and harsh environments.
Technical Expertise:Electric high-temperature ball valve manufacturers employ skilled engineers and technicians who possess in-depth knowledge of materials science, fluid dynamics, and automation technology, ensuring the design and production of high-quality valves.
Support and Maintenance:Many manufacturers offer comprehensive after-sales support, maintenance, and spare parts services, ensuring the longevity and peak performance of their products in high-temperature environments.
Key Attributes of Electric High-Temperature Ball Valve Manufacturers
When evaluating electric high-temperature ball valve manufacturers, certain attributes set the industry leaders apart:
Experience:Established manufacturers often have a rich history of producing valves that demonstrates their expertise and reliability in the field, especially when it comes to high-temperature applications.
Quality Certifications:Recognized certifications, such as ISO 9001, are indicative of a manufacturer's commitment to quality and compliance with international standards in the realm of high-temperature fluid control.
Product Range:A diverse product portfolio enables manufacturers to cater to various high-temperature industries, applications, and unique specifications.
Innovation:Leading manufacturers invest in research and development to introduce innovative features, materials, and designs that can withstand extreme temperatures and challenging conditions.
Global Reach:Manufacturers with a global presence can provide their high-temperature valve products and services to customers worldwide, ensuring accessibility and timely support.
Applications and Industries
Electric high-temperature ball valve manufacturers serve a wide range of industries and high-temperature applications, including but not limited to:
Power Generation:For controlling the flow of high-temperature steam, hot water, and various fluids in power plants and boiler systems.
Oil and Gas:In refineries, petrochemical plants, and offshore drilling operations to manage the flow of high-temperature hydrocarbons, gases, and corrosive substances.
Metallurgy:For regulating the flow of molten metals, high-temperature gases, and industrial fluids in steel mills and metallurgical processes.
Chemical Manufacturing:In chemical processing plants to control the flow of high-temperature and corrosive chemicals, ensuring safety and process integrity.
High-Temperature Water Treatment:In facilities where hot water is used for various processes, including sterilization and cleaning.
The Future of Electric High-Temperature Ball Valve Manufacturers
As industries continue to advance and adopt smart technologies, electric high-temperature ball valve manufacturers are poised for further growth and innovation. Anticipated future trends may include:
IoT Integration:Greater connectivity for real-time monitoring, data collection, and predictive maintenance of high-temperature valves in extreme environments.
Enhanced Materials:Ongoing development of advanced materials and coatings for improved resistance to extreme temperatures and harsh conditions.
Energy Efficiency:Manufacturers will likely focus on reducing energy consumption and enhancing the energy efficiency of electric actuators in high-temperature applications.
Sustainability:A growing emphasis on eco-friendly materials and processes to meet environmental goals while ensuring high-temperature valve performance.
In conclusion, electric high-temperature ball valve manufacturers are essential players in modern engineering, offering high-quality, customizable solutions for fluid control needs in extreme heat. Their commitment to quality, innovation, and technical expertise ensures the reliability and efficiency of fluid control systems operating in the most challenging high-temperature environments.
标题:"Masters of Air: Exploring Pneumatic Ball Valve Manufacturers"
Pneumatic ball valve manufacturers are the unsung heroes behind the precision and efficiency of fluid control systems across various industries. These manufacturers are instrumental in designing, producing, and delivering cutting-edge solutions that regulate fluid flow with accuracy and reliability through the power of compressed air. In this article, we will dive into the realm of pneumatic ball valve manufacturers, exploring their significance, key attributes, and the pivotal role they play in modern engineering.
The Significance of Pneumatic Ball Valve Manufacturers
Pneumatic ball valve manufacturers are pivotal in fulfilling the increasing demand for advanced fluid control solutions across various sectors. Their significance goes beyond production; they are the architects of innovation and engineering excellence. Here's why they are important:
Quality Assurance:Reputable manufacturers adhere to strict quality control processes, ensuring that their pneumatic ball valves meet industry standards and customer expectations for performance and reliability.
Customization:Manufacturers often provide tailored solutions, allowing customers to specify valve parameters, materials, and features to suit their unique applications.
Innovation:Manufacturers invest in research and development to create valves that are not only more efficient but also capable of meeting evolving industry needs.
Technical Expertise:Pneumatic ball valve manufacturers employ skilled engineers and technicians who possess in-depth knowledge of fluid dynamics, materials science, and automation technology, ensuring the design and production of high-quality valves.
Support and Maintenance:Many manufacturers offer comprehensive after-sales support, maintenance, and spare parts services, ensuring the longevity and peak performance of their products.
Key Attributes of Pneumatic Ball Valve Manufacturers
When evaluating pneumatic ball valve manufacturers, certain attributes set the industry leaders apart:
Experience:Established manufacturers often have a rich history of producing valves, demonstrating their expertise and reliability in the field.
Quality Certifications:Recognized certifications, such as ISO 9001, demonstrate a manufacturer's commitment to quality and compliance with international standards in pneumatic fluid control.
Product Range:A diverse product portfolio allows manufacturers to cater to various industries, applications, and unique specifications.
Innovation:Leading manufacturers invest in research and development to introduce innovative features, materials, and designs that enhance valve performance.
Global Reach:Manufacturers with a global presence can provide their pneumatic ball valve products and services to customers worldwide, ensuring accessibility and timely support.
Applications and Industries
Pneumatic ball valve manufacturers serve a wide range of industries and applications, including but not limited to:
Oil and Gas:In oil refineries, petrochemical plants, and offshore drilling operations for controlling the flow of crude oil, natural gas, and various chemicals.
Water Treatment:In municipal and industrial facilities for managing water, wastewater, and chemical processes.
Chemical Manufacturing:In chemical processing plants to regulate the flow of corrosive and hazardous chemicals, ensuring safety and process integrity.
Power Generation:In power plants for controlling cooling water, steam, and various fluids in energy production processes.
Pharmaceuticals:Ensuring the accuracy and sterility of pharmaceutical liquids in manufacturing processes.
The Future of Pneumatic Ball Valve Manufacturers
As industries continue to advance and embrace automation and smart technologies, pneumatic ball valve manufacturers are poised for further growth and innovation. Anticipated future trends may include:
IoT Integration:Greater connectivity for real-time monitoring, data collection, and predictive maintenance of pneumatic valves.
Enhanced Materials:Ongoing development of advanced materials for improved corrosion resistance and longevity.
Energy Efficiency:Manufacturers will focus on reducing energy consumption and enhancing the energy efficiency of pneumatic actuators.
Sustainability:A growing emphasis on eco-friendly materials and processes to meet environmental goals while ensuring valve performance.
In conclusion, pneumatic ball valve manufacturers are essential players in modern engineering, offering high-quality, customizable solutions for fluid control needs across diverse industries. Their commitment to quality, innovation, and technical expertise ensures the reliability and efficiency of fluid control systems, making them a cornerstone of industrial processes worldwide.
Title:"Clarity and Precision: Exploring Electric Glass Valve Manufacturers"
Electric glass valve manufacturers are at the forefront of innovation, offering precision, transparency, and reliability in fluid control systems across various industries. These manufacturers are instrumental in designing, producing, and delivering cutting-edge solutions that regulate fluid flow while providing a clear view of the process through glass components. In this article, we will delve into the world of electric glass valve manufacturers, exploring their significance, key attributes, and the pivotal role they play in modern engineering.
The Significance of Electric Glass Valve Manufacturers
Electric glass valve manufacturers are indispensable in fulfilling the growing demand for precise and transparent fluid control solutions. Their significance goes beyond production; they are the architects of innovation and engineering excellence. Here's why they are important:
Quality Assurance:Reputable manufacturers adhere to strict quality control processes, ensuring that their electric glass valves meet industry standards and customer expectations for performance and reliability, especially when visibility is a critical factor.
Customization:Manufacturers often provide tailored solutions, allowing customers to specify valve parameters, materials, and features to suit their unique applications that require transparency.
Innovation:Manufacturers invest in research and development to create valves that offer precise control of fluid flow while maintaining transparency, even in harsh conditions.
Technical Expertise:Electric glass valve manufacturers employ skilled engineers and technicians who possess in-depth knowledge of materials science, fluid dynamics, and automation technology, ensuring the design and production of high-quality valves with glass components.
Support and Maintenance:Many manufacturers offer comprehensive after-sales support, maintenance, and spare parts services, ensuring the longevity and peak performance of their glass valve products.
Key Attributes of Electric Glass Valve Manufacturers
When evaluating electric glass valve manufacturers, several attributes set the industry leaders apart:
Experience:Established manufacturers often have a rich history of producing valves with glass components, demonstrating their expertise and reliability in the field.
Quality Certifications:Recognized certifications, such as ISO 9001, indicate a manufacturer's commitment to quality and compliance with international standards in the realm of electric glass valves.
Product Range:A diverse product portfolio allows manufacturers to cater to various industries, applications, and unique specifications, all of which require the clarity of glass.
Innovation:Leading manufacturers invest in research and development to introduce innovative features, materials, and designs that enhance valve performance while maintaining transparency.
Global Reach:Manufacturers with a global presence can provide their electric glass valve products and services to customers worldwide, ensuring accessibility and timely support.
Applications and Industries
Electric glass valve manufacturers serve a wide range of industries and applications, including but not limited to:
Pharmaceuticals:Ensuring the accuracy and sterility of pharmaceutical liquids in manufacturing processes that require transparency.
Chemical Manufacturing:In chemical processing plants to regulate the flow of corrosive and hazardous chemicals while maintaining visibility of the process.
Food and Beverage:In the food and beverage industry for controlling the flow of liquids, including beverages, dairy products, and sauces, while ensuring product quality through transparent components.
Laboratory and Research:Laboratories often use these valves in experimental setups where visual observation of fluid flow is necessary.
Water Treatment:In municipal and industrial water treatment facilities for managing water, chemicals, and wastewater while maintaining transparency for monitoring.
The Future of Electric Glass Valve Manufacturers
As industries continue to advance and embrace automation and smart technologies, electric glass valve manufacturers are poised for further growth and innovation. Anticipated future trends may include:
IoT Integration:Greater connectivity for real-time monitoring, data collection, and predictive maintenance of electric glass valves in transparent fluid control systems.
Enhanced Materials:Ongoing development of advanced glass materials and coatings for improved resistance to temperature variations and chemical corrosion.
Energy Efficiency:Manufacturers will focus on reducing energy consumption and enhancing the energy efficiency of electric actuators in glass valve systems.
Sustainability:A growing emphasis on eco-friendly materials and processes to meet environmental goals while ensuring the performance and transparency of glass valve components.
In conclusion, electric glass valve manufacturers are essential players in modern engineering, offering high-quality, customizable solutions for fluid control needs that require precision and transparency across diverse industries. Their commitment to quality, innovation, and technical expertise ensures the reliability and efficiency of fluid control systems, making them a cornerstone of industrial processes worldwide.
Title:"Navigating Excellence: The World of Marine Electric Butterfly Valve Manufacturers"
Marine electric butterfly valve manufacturers are at the helm of innovation, offering precision, reliability, and durability in fluid control systems for the maritime industry. These manufacturers play a pivotal role in designing, producing, and delivering cutting-edge solutions that regulate fluid flow with accuracy and efficiency in the challenging marine environment. In this article, we will dive into the world of marine electric butterfly valve manufacturers, exploring their significance, key attributes, and the vital role they play in modern maritime engineering.
The Significance of Marine Electric Butterfly Valve Manufacturers
Marine electric butterfly valve manufacturers are indispensable in meeting the unique demands of the maritime industry, where reliability, durability, and precision are paramount. Their significance extends beyond production; they are the architects of innovation and engineering excellence. Here's why they are crucial:
Quality Assurance:Reputable manufacturers adhere to strict quality control processes, ensuring that their marine electric butterfly valves meet industry standards and the stringent requirements of the maritime environment.
Customization:Manufacturers often provide tailored solutions, allowing customers to specify valve parameters, materials, and features to suit their specific marine applications.
Innovation:Manufacturers invest in research and development to create valves that offer precise control of fluid flow while withstanding the harsh conditions of the sea.
Technical Expertise:Marine electric butterfly valve manufacturers employ skilled engineers and technicians who possess in-depth knowledge of materials science, fluid dynamics, and automation technology, ensuring the design and production of high-quality valves suited for marine environments.
Support and Maintenance:Many manufacturers offer comprehensive after-sales support, maintenance, and spare parts services, ensuring the longevity and peak performance of their marine valve products.
Key Attributes of Marine Electric Butterfly Valve Manufacturers
When evaluating marine electric butterfly valve manufacturers, certain attributes set the industry leaders apart:
Experience:Established manufacturers often have a rich history of producing valves for maritime applications, demonstrating their expertise and reliability in the field.
Quality Certifications:Recognized certifications, such as ISO 9001 and marine-specific certifications, indicate a manufacturer's commitment to quality and compliance with international maritime standards.
Product Range:A diverse product portfolio allows manufacturers to cater to various marine applications, vessel types, and unique specifications.
Innovation:Leading manufacturers invest in research and development to introduce innovative features, materials, and designs that enhance valve performance in the maritime environment.
Global Reach:Manufacturers with a global presence can provide their marine electric butterfly valve products and services to customers worldwide, ensuring accessibility and timely support.
Applications in the Maritime Industry
Marine electric butterfly valve manufacturers serve a wide range of applications within the maritime industry, including but not limited to:
Shipbuilding:For controlling the flow of seawater, ballast water, and various fluids critical to ship operation and stability.
Marine Propulsion:In marine propulsion systems for regulating fuel and cooling water flow, ensuring efficient and safe engine operation.
Ballast Systems:In ballast water management systems for compliance with international regulations and maintaining vessel stability.
Offshore Platforms:On offshore oil and gas platforms for controlling the flow of drilling fluids, production fluids, and other substances in extreme marine conditions.
Marine HVAC Systems:In shipboard HVAC systems for regulating the flow of air and water for temperature control and comfort.
The Future of Marine Electric Butterfly Valve Manufacturers
As the maritime industry continues to evolve and embrace automation and smart technologies, marine electric butterfly valve manufacturers are poised for further growth and innovation. Anticipated future trends may include:
IoT Integration:Greater connectivity for real-time monitoring, data collection, and predictive maintenance of marine electric butterfly valves on vessels.
Enhanced Materials:Ongoing development of advanced materials and coatings for improved corrosion resistance and longevity in marine applications.
Energy Efficiency:Manufacturers will focus on reducing energy consumption and enhancing the energy efficiency of electric actuators in marine valve systems.
Environmental Compliance:Meeting evolving environmental regulations with eco-friendly materials and processes while ensuring valve performance in harsh marine conditions.
In conclusion, marine electric butterfly valve manufacturers are essential contributors to modern maritime engineering, offering high-quality, customizable solutions for fluid control needs in the challenging marine environment. Their commitment to quality, innovation, and technical expertise ensures the reliability and efficiency of fluid control systems on ships and offshore structures, making them indispensable in the maritime industry worldwide.
Title:"Powering Progress: The World of Electric Power Station Valve Manufacturers"
Electric power station valve manufacturers are the driving force behind the reliability, efficiency, and safety of electricity generation and distribution. These manufacturers play a pivotal role in designing, producing, and delivering cutting-edge valve solutions that control the flow of fluids and gases within power stations. In this article, we will explore the world of electric power station valve manufacturers, their significance, key attributes, and their crucial role in modern power generation infrastructure.
The Significance of Electric Power Station Valve Manufacturers
Electric power station valve manufacturers are instrumental in meeting the growing demand for robust and precise fluid control solutions in the power generation sector. Their significance extends beyond production; they are the architects of innovation and engineering excellence. Here's why they are essential:
Quality Assurance:Reputable manufacturers adhere to strict quality control processes, ensuring that their electric power station valves meet industry standards and stringent requirements for performance and safety in power generation facilities.
Customization:Manufacturers often provide tailored solutions, allowing power stations to specify valve parameters, materials, and features to meet their unique operational needs.
Innovation:Manufacturers invest in research and development to create valves that offer precise control of fluids and gases, contributing to improved efficiency and safety in power plants.
Technical Expertise:Electric power station valve manufacturers employ skilled engineers and technicians with expertise in materials science, fluid dynamics, and automation technology, ensuring the design and production of high-quality valves.
Support and Maintenance:Many manufacturers offer comprehensive after-sales support, maintenance, and spare parts services, ensuring the longevity and peak performance of their valve products.
Key Attributes of Electric Power Station Valve Manufacturers
When evaluating electric power station valve manufacturers, certain attributes distinguish industry leaders:
Experience:Established manufacturers often have a rich history of producing valves for power generation applications, demonstrating their expertise and reliability in the field.
Quality Certifications:Recognized certifications, such as ISO 9001 and ASME certifications, indicate a manufacturer's commitment to quality and compliance with international standards in power generation.
Product Range:A diverse product portfolio allows manufacturers to cater to various power generation applications, including steam, water, and gas control, meeting the specific needs of power plants.
Innovation:Leading manufacturers invest in research and development to introduce innovative features, materials, and designs that enhance valve performance and reliability in power generation.
Global Reach:Manufacturers with a global presence can provide their electric power station valve products and services to power stations worldwide, ensuring accessibility and timely support.
Applications in Power Generation
Electric power station valve manufacturers serve a wide range of applications within the power generation industry, including but not limited to:
Steam Turbines:In power plants, valves regulate the flow of steam to control turbine operation and energy generation.
Boiler Systems:For controlling the flow of water and steam within boilers to maintain temperature, pressure, and safety.
Gas Turbines:Valves play a role in managing the flow of fuel and combustion air in gas turbine systems for electricity generation.
Cooling Systems:In cooling water circuits to control the flow of cooling fluids and maintain optimal temperatures in power generation equipment.
Combined Cycle Power Plants:In combined cycle power plants that integrate gas and steam turbines for enhanced efficiency.
The Future of Electric Power Station Valve Manufacturers
As the power generation sector continues to evolve and embrace automation and smart technologies, electric power station valve manufacturers are poised for further growth and innovation. Anticipated future trends may include:
IoT Integration:Greater connectivity for real-time monitoring, data collection, and predictive maintenance of electric power station valves, enhancing overall plant efficiency and reliability.
Enhanced Materials:Ongoing development of advanced materials and coatings for improved corrosion resistance and longevity in challenging power plant environments.
Energy Efficiency:Manufacturers will focus on reducing energy consumption and enhancing the energy efficiency of electric actuators in valve systems.
Environmental Sustainability:Meeting evolving environmental regulations with eco-friendly materials and processes while ensuring valve performance and safety in power generation.
In conclusion, electric power station valve manufacturers are indispensable contributors to modern power generation infrastructure, offering high-quality, customizable solutions for fluid control needs in power plants. Their commitment to quality, innovation, and technical expertise ensures the reliability and efficiency of fluid control systems in electricity generation, making them essential in the power generation sector worldwide.
Title:"Igniting Safety: Exploring Explosion-Proof Electric Actuator OEM Manufacturers"
Explosion-proof electric actuator OEM (Original Equipment Manufacturer) manufacturers are at the forefront of safety and precision in industries where hazardous environments are a constant concern. These manufacturers play a pivotal role in designing, producing, and delivering cutting-edge solutions that control valve and equipment operations in explosive atmospheres. In this article, we will delve into the world of explosion-proof electric actuator OEM manufacturers, exploring their significance, key attributes, and the critical role they play in modern industrial safety.
The Significance of Explosion-Proof Electric Actuator OEM Manufacturers
Explosion-proof electric actuator OEM manufacturers are indispensable in fulfilling the growing demand for safety-critical solutions in industries such as oil and gas, petrochemical, chemical, and mining, where explosive atmospheres pose significant risks. Their significance goes beyond production; they are the guardians of innovation and engineering excellence in hazardous environments. Here's why they are essential:
Safety Assurance:Reputable manufacturers adhere to rigorous safety standards and certifications, ensuring that their explosion-proof electric actuators provide a robust safeguard against potential explosions or fires in hazardous areas.
Customization:Manufacturers often offer tailored solutions, allowing customers to specify actuator parameters, materials, and features to meet the unique requirements of their applications and environments.
Innovation:Manufacturers invest in research and development to create explosion-proof electric actuators that offer precise control while maintaining safety in explosive atmospheres.
Technical Expertise:Explosion-proof electric actuator OEM manufacturers employ highly skilled engineers and technicians who possess specialized knowledge of materials science, explosion protection, and automation technology, ensuring the design and production of high-quality actuators.
Support and Maintenance:Many manufacturers provide comprehensive after-sales support, maintenance, and spare parts services, ensuring the longevity and peak performance of their explosion-proof electric actuator products in hazardous areas.
Key Attributes of Explosion-Proof Electric Actuator OEM Manufacturers
When evaluating explosion-proof electric actuator OEM manufacturers, certain attributes distinguish industry leaders:
Experience:Established manufacturers often have a rich history of producing explosion-proof actuators, demonstrating their expertise and reliability in the field of hazardous-area automation.
Safety Certifications:Recognized certifications, such as ATEX, IECEx, and FM approvals, demonstrate a manufacturer's commitment to safety and compliance with international standards for explosive atmospheres.
Product Range:A diverse product portfolio allows manufacturers to cater to various industries, applications, and unique specifications, all of which demand safety and precision in hazardous environments.
Innovation:Leading manufacturers invest in research and development to introduce innovative features, materials, and designs that enhance actuator performance while ensuring explosion protection.
Global Reach:Manufacturers with a global presence can provide their explosion-proof electric actuator OEM products and services to customers worldwide, ensuring accessibility and timely support.
Applications in Hazardous Environments
Explosion-proof electric actuator OEM manufacturers serve a wide range of applications in industries where hazardous atmospheres are prevalent, including but not limited to:
Oil and Gas:For controlling valves and equipment in oil refineries, drilling platforms, and processing facilities, where flammable gases and liquids are present.
Petrochemical:In chemical processing plants handling volatile substances that require precise control while minimizing the risk of explosions.
Mining:In underground mining operations, where the presence of dust and gas mixtures poses explosion risks.
Chemical Manufacturing:For the safe automation of processes involving hazardous chemicals in chemical production plants.
Pharmaceuticals:In pharmaceutical manufacturing, where precision control in potentially explosive environments is crucial.
The Future of Explosion-Proof Electric Actuator OEM Manufacturers
As industries continue to advance and prioritize safety in hazardous environments, explosion-proof electric actuator OEM manufacturers are poised for further growth and innovation. Anticipated future trends may include:
IoT Integration:Greater connectivity for real-time monitoring, data collection, and predictive maintenance of explosion-proof electric actuators in hazardous areas.
Enhanced Materials:Ongoing development of advanced explosion-resistant materials and coatings for improved safety and durability.
Energy Efficiency:Manufacturers will focus on reducing energy consumption and enhancing the energy efficiency of explosion-proof electric actuators.
Environmental Sustainability:A growing emphasis on eco-friendly materials and processes to meet environmental goals while ensuring safety and precision in hazardous environments.
In conclusion, explosion-proof electric actuator OEM manufacturers are indispensable contributors to modern industrial safety, offering high-quality, customizable solutions for automation needs in explosive atmospheres. Their commitment to safety, innovation, and technical expertise ensures the reliability and precision of valve and equipment control in hazardous areas, making them vital players in industrial safety worldwide.
Title:"Safeguarding Industry: The Evolution of Explosion-Proof Electric Butterfly Valves"
Explosion-proof electric butterfly valves represent a crucial innovation in industrial safety, providing a reliable solution for managing fluid flow in hazardous environments. These valves are specifically designed to prevent explosions and fires in areas where flammable gases, vapors, or dust are present. In this article, we will explore the world of explosion-proof electric butterfly valves, their significance, key attributes, and their vital role in modern industrial safety.
The Significance of Explosion-Proof Electric Butterfly Valves
Explosion-proof electric butterfly valves are of paramount importance in industries such as oil and gas, petrochemical, chemical, mining, and more. Their significance extends beyond safety; they are the guardians of productivity and reliability in hazardous locations. Here's why they are essential:
Safety Assurance:These valves are meticulously engineered to prevent ignition sources from coming into contact with flammable substances, minimizing the risk of explosions or fires in volatile atmospheres.
Customization:Manufacturers often offer tailored solutions, allowing users to specify valve parameters, materials, and features to meet the unique requirements of their applications in hazardous environments.
Innovation:Continuous research and development efforts have resulted in innovative designs and materials that enhance the performance and safety of explosion-proof electric butterfly valves.
Technical Expertise:Manufacturers employ skilled engineers and technicians who possess specialized knowledge of explosion protection, materials science, and automation technology, ensuring the production of high-quality, reliable valves.
Support and Maintenance:Many manufacturers provide comprehensive after-sales support, maintenance, and spare parts services, ensuring the longevity and peak performance of their explosion-proof electric butterfly valves.
Key Attributes of Explosion-Proof Electric Butterfly Valves
When evaluating explosion-proof electric butterfly valves, certain attributes distinguish industry leaders:
Certifications:Recognized certifications, such as ATEX and IECEx, are indicative of a manufacturer's commitment to safety and compliance with international standards for explosive atmospheres.
Product Range:A diverse product portfolio enables manufacturers to cater to various industries, applications, and unique specifications, all of which require safety and precision in hazardous environments.
Innovation:Leading manufacturers invest in research and development to introduce features, materials, and designs that enhance valve performance while ensuring explosion protection.
Global Reach:Manufacturers with a global presence can provide their explosion-proof electric butterfly valves to customers worldwide, ensuring accessibility and timely support.
Applications in Hazardous Environments
Explosion-proof electric butterfly valves are deployed in a wide range of applications in industries where safety is paramount, including but not limited to:
Oil and Gas:For controlling the flow of flammable gases and liquids in oil refineries, drilling platforms, and processing facilities.
Petrochemical:In chemical processing plants that handle volatile substances requiring precise control while minimizing explosion risks.
Mining:In underground mining operations, where dust and gas mixtures pose explosion risks.
Chemical Manufacturing:For the safe automation of processes involving hazardous chemicals in chemical production plants.
Pharmaceuticals:In pharmaceutical manufacturing, where precise control in potentially explosive environments is critical.
The Future of Explosion-Proof Electric Butterfly Valves
As industries continue to advance and prioritize safety in hazardous environments, explosion-proof electric butterfly valve manufacturers are poised for further growth and innovation. Anticipated future trends may include:
IoT Integration:Greater connectivity for real-time monitoring, data collection, and predictive maintenance of explosion-proof electric butterfly valves in hazardous areas.
Enhanced Materials:Ongoing development of advanced explosion-resistant materials and coatings for improved safety and durability.
Energy Efficiency:Manufacturers will focus on reducing energy consumption and enhancing the energy efficiency of explosion-proof electric actuators.
Environmental Sustainability:A growing emphasis on eco-friendly materials and processes to meet environmental goals while ensuring safety and precision in hazardous environments.
In conclusion, explosion-proof electric butterfly valves are indispensable contributors to modern industrial safety, offering high-quality, customizable solutions for fluid control needs in explosive atmospheres. Their commitment to safety, innovation, and technical expertise ensures the reliability and precision of fluid control systems in hazardous areas, making them vital players in industrial safety worldwide.
Title:"Precision in Control: The World of Electric Two-Seat Regulating Valve OEM Manufacturers"
Electric two-seat regulating valve OEM (Original Equipment Manufacturer) manufacturers are key players in the realm of industrial automation and precision control. These manufacturers are at the forefront of designing, producing, and delivering cutting-edge solutions that regulate fluid flow with unparalleled accuracy. In this article, we will delve into the world of electric two-seat regulating valve OEM manufacturers, exploring their significance, key attributes, and the critical role they play in modern industrial processes.
The Significance of Electric Two-Seat Regulating Valve OEM Manufacturers
Electric two-seat regulating valve OEM manufacturers are instrumental in meeting the increasing demand for precise and reliable fluid control solutions across various industries. Their significance goes beyond production; they are the architects of innovation and engineering excellence. Here's why they are essential:
Precision Control:These valves offer exceptional control over fluid flow, making them indispensable in processes where accuracy is paramount, such as chemical manufacturing and power generation.
Customization:Manufacturers often provide tailored solutions, allowing customers to specify valve parameters, materials, and features to suit their unique applications and control requirements.
Innovation:Manufacturers invest in research and development to create valves that provide not only precise control but also innovative features and designs that enhance overall system performance.
Technical Expertise:Electric two-seat regulating valve OEM manufacturers employ skilled engineers and technicians who possess in-depth knowledge of fluid dynamics, materials science, and automation technology, ensuring the design and production of high-quality valves.
Support and Maintenance:Many manufacturers offer comprehensive after-sales support, maintenance, and spare parts services, ensuring the longevity and peak performance of their valve products.
Key Attributes of Electric Two-Seat Regulating Valve OEM Manufacturers
When evaluating electric two-seat regulating valve OEM manufacturers, certain attributes set industry leaders apart:
Experience:Established manufacturers often have a rich history of producing valves, demonstrating their expertise and reliability in the field of precise fluid control.
Quality Certifications:Recognized certifications, such as ISO 9001, indicate a manufacturer's commitment to quality and compliance with international standards in fluid control.
Product Range:A diverse product portfolio allows manufacturers to cater to various industries, applications, and unique specifications, all of which demand precision and reliability in fluid control.
Innovation:Leading manufacturers invest in research and development to introduce innovative features, materials, and designs that enhance valve performance and accuracy.
Global Reach:Manufacturers with a global presence can provide their electric two-seat regulating valve OEM products and services to customers worldwide, ensuring accessibility and timely support.
Applications and Industries
Electric two-seat regulating valve OEM manufacturers serve a wide range of industries and applications, including but not limited to:
Chemical Manufacturing:For precise control of chemical processes where accurate regulation of flow rates and pressures is essential.
Power Generation:In power plants to control the flow of steam, cooling water, and various fluids for efficient and reliable energy production.
Pharmaceuticals:Ensuring the accuracy and sterility of pharmaceutical liquids in manufacturing processes.
Water Treatment:In municipal and industrial facilities for managing water, wastewater, and chemical processes with precision.
Oil and Gas:For controlling the flow of hydrocarbons and chemicals in the oil and gas industry, ensuring safety and process integrity.
The Future of Electric Two-Seat Regulating Valve OEM Manufacturers
As industries continue to advance and embrace automation and smart technologies, electric two-seat regulating valve OEM manufacturers are poised for further growth and innovation. Anticipated future trends may include:
IoT Integration:Greater connectivity for real-time monitoring, data collection, and predictive maintenance of electric two-seat regulating valves, enhancing system efficiency and reliability.
Enhanced Materials:Ongoing development of advanced materials and coatings for improved corrosion resistance and longevity in diverse industrial environments.
Energy Efficiency:Manufacturers will focus on reducing energy consumption and enhancing the energy efficiency of electric actuators in valve systems.
Environmental Sustainability:A growing emphasis on eco-friendly materials and processes to meet environmental goals while ensuring the performance and accuracy of electric two-seat regulating valves.
In conclusion, electric two-seat regulating valve OEM manufacturers are essential contributors to modern industrial processes, offering high-quality, customizable solutions for precision fluid control needs across diverse industries. Their commitment to quality, innovation, and technical expertise ensures the reliability and accuracy of fluid control systems, making them vital partners in industrial automation worldwide.
Title:"Efficiency Unleashed: The World of Electric Sludge Discharge Valve OEM Manufacturers"
Electric sludge discharge valve OEM (Original Equipment Manufacturer) manufacturers are pivotal in ensuring the efficient operation of various industrial processes, particularly in wastewater treatment and sludge handling. These manufacturers are at the forefront of designing, producing, and delivering cutting-edge solutions that help manage and dispose of sludge effectively. In this article, we will explore the world of electric sludge discharge valve OEM manufacturers, their significance, key attributes, and the crucial role they play in modern industrial and environmental processes.
The Significance of Electric Sludge Discharge Valve OEM Manufacturers
Electric sludge discharge valve OEM manufacturers are instrumental in addressing the ever-growing demand for efficient and environmentally friendly sludge management solutions. Their significance goes beyond production; they are the architects of innovation and engineering excellence. Here's why they are indispensable:
Efficient Sludge Management:These valves play a critical role in the effective discharge of sludge from industrial processes and wastewater treatment facilities, improving overall efficiency.
Customization:Manufacturers often provide tailored solutions, allowing customers to specify valve parameters, materials, and features to meet the unique requirements of their sludge discharge applications.
Innovation:Manufacturers invest in research and development to create valves that offer precise and reliable sludge control while minimizing environmental impact.
Technical Expertise:Electric sludge discharge valve OEM manufacturers employ skilled engineers and technicians who possess specialized knowledge of fluid dynamics, materials science, and automation technology, ensuring the design and production of high-quality valves.
Support and Maintenance:Many manufacturers offer comprehensive after-sales support, maintenance, and spare parts services, ensuring the longevity and peak performance of their valve products in sludge management systems.
Key Attributes of Electric Sludge Discharge Valve OEM Manufacturers
When evaluating electric sludge discharge valve OEM manufacturers, certain attributes set industry leaders apart:
Experience:Established manufacturers often have a rich history of producing valves for sludge management, demonstrating their expertise and reliability in the field.
Quality Certifications:Recognized certifications, such as ISO 9001, indicate a manufacturer's commitment to quality and compliance with international standards in sludge discharge.
Product Range:A diverse product portfolio allows manufacturers to cater to various industries, applications, and unique specifications, all of which require efficient sludge management.
Innovation:Leading manufacturers invest in research and development to introduce innovative features, materials, and designs that enhance valve performance and reliability in sludge discharge.
Global Reach:Manufacturers with a global presence can provide their electric sludge discharge valve OEM products and services to customers worldwide, ensuring accessibility and timely support.
Applications and Industries
Electric sludge discharge valve OEM manufacturers serve a wide range of applications within industries focused on sludge management and wastewater treatment, including but not limited to:
Wastewater Treatment:In sewage treatment plants for efficient sludge dewatering and disposal.
Industrial Processes:In various industries such as pulp and paper, chemical manufacturing, and mining, for the controlled discharge of sludge generated during production.
Environmental Remediation:In environmental cleanup and soil remediation projects, where sludge disposal requires precision and control.
Biogas Production:In anaerobic digestion processes for the controlled release of digested sludge and biogas production.
The Future of Electric Sludge Discharge Valve OEM Manufacturers
As industries continue to evolve and prioritize efficient and environmentally responsible sludge management, electric sludge discharge valve OEM manufacturers are poised for further growth and innovation. Anticipated future trends may include:
IoT Integration:Greater connectivity for real-time monitoring, data collection, and predictive maintenance of electric sludge discharge valves, enhancing overall system efficiency and reliability.
Enhanced Materials:Ongoing development of advanced materials and coatings for improved corrosion resistance and longevity in diverse sludge management environments.
Energy Efficiency:Manufacturers will focus on reducing energy consumption and enhancing the energy efficiency of electric actuators in valve systems.
Environmental Sustainability:A growing emphasis on eco-friendly materials and processes to meet environmental goals while ensuring efficient and precise sludge discharge.
In conclusion, electric sludge discharge valve OEM manufacturers are essential contributors to modern industrial and environmental processes, offering high-quality, customizable solutions for efficient sludge management needs across diverse industries. Their commitment to quality, innovation, and technical expertise ensures the reliability and efficiency of sludge management systems, making them vital partners in environmental sustainability and industrial efficiency worldwide.
Title:"Precision and Durability: Exploring Electric Stainless Steel Flange Ball Valve ODM Manufacturers"
Electric stainless steel flange ball valve ODM (Original Design Manufacturer) companies are pivotal in ensuring the reliability and precision of fluid control systems in various industries. These manufacturers are at the forefront of designing, producing, and delivering cutting-edge solutions that regulate fluid flow with exceptional precision and durability. In this article, we will explore the world of electric stainless steel flange ball valve ODM manufacturers, their significance, key attributes, and the critical role they play in modern industrial processes.
The Significance of Electric Stainless Steel Flange Ball Valve ODM Manufacturers
Electric stainless steel flange ball valve ODM manufacturers are instrumental in addressing the increasing demand for high-performance fluid control solutions in industries such as oil and gas, chemical manufacturing, and water treatment. Their significance extends beyond production; they are the innovators and architects of engineering excellence. Here's why they are indispensable:
Precision Control:These valves offer exceptional control over fluid flow, making them essential for processes where accuracy is paramount, such as petrochemical refining and pharmaceutical production.
Customization:Manufacturers often provide tailored solutions, allowing customers to specify valve parameters, materials, and features to meet the unique requirements of their applications.
Innovation:Manufacturers invest in research and development to create valves that provide not only precise control but also innovative features, materials, and designs that enhance overall system performance.
Technical Expertise:Electric stainless steel flange ball valve ODM manufacturers employ skilled engineers and technicians with specialized knowledge of materials science, fluid dynamics, and automation technology, ensuring the design and production of high-quality valves.
Support and Maintenance:Many manufacturers offer comprehensive after-sales support, maintenance, and spare parts services, ensuring the longevity and peak performance of their valve products in fluid control systems.
Key Attributes of Electric Stainless Steel Flange Ball Valve ODM Manufacturers
When evaluating electric stainless steel flange ball valve ODM manufacturers, certain attributes distinguish industry leaders:
Experience:Established manufacturers often have a rich history of producing valves, demonstrating their expertise and reliability in the field of fluid control.
Quality Certifications:Recognized certifications, such as ISO 9001, indicate a manufacturer's commitment to quality and compliance with international standards in fluid control.
Product Range:A diverse product portfolio allows manufacturers to cater to various industries, applications, and unique specifications, all of which require precision and durability in fluid control.
Innovation:Leading manufacturers invest in research and development to introduce innovative features, materials, and designs that enhance valve performance and reliability.
Global Reach:Manufacturers with a global presence can provide their electric stainless steel flange ball valve ODM products and services to customers worldwide, ensuring accessibility and timely support.
Applications and Industries
Electric stainless steel flange ball valve ODM manufacturers serve a wide range of applications within industries that demand precision and durability in fluid control, including but not limited to:
Oil and Gas:For controlling the flow of various fluids in exploration, drilling, refining, and distribution processes.
Chemical Manufacturing:In chemical processing plants that require precise control over chemical reactions and fluid flow.
Water Treatment:In municipal and industrial water treatment facilities for regulating water flow, chemical dosing, and filtration.
Pharmaceuticals:Ensuring the accuracy and sterility of pharmaceutical liquids in manufacturing processes.
Food and Beverage:For controlling the flow of ingredients, liquids, and gases in food processing and bottling plants.
The Future of Electric Stainless Steel Flange Ball Valve ODM Manufacturers
As industries continue to advance and prioritize precision, durability, and sustainability in fluid control, electric stainless steel flange ball valve ODM manufacturers are poised for further growth and innovation. Anticipated future trends may include:
IoT Integration:Greater connectivity for real-time monitoring, data collection, and predictive maintenance of electric stainless steel flange ball valves, enhancing overall system efficiency and reliability.
Enhanced Materials:Ongoing development of advanced materials and coatings for improved corrosion resistance and longevity in diverse industrial environments.
Energy Efficiency:Manufacturers will focus on reducing energy consumption and enhancing the energy efficiency of electric actuators in valve systems.
Environmental Sustainability:A growing emphasis on eco-friendly materials and processes to meet environmental goals while ensuring efficient and precise fluid control.
In conclusion, electric stainless steel flange ball valve ODM manufacturers are essential contributors to modern industrial processes, offering high-quality, customizable solutions for precision fluid control needs across diverse industries. Their commitment to quality, innovation, and technical expertise ensures the reliability and efficiency of fluid control systems, making them vital partners in industrial efficiency and precision control worldwide.
Title:"Powering Precision: The World of Electric Flange Ball Valve ODM Manufacturers"
Electric flange ball valve ODM (Original Design Manufacturer) companies are at the forefront of industrial innovation, providing critical solutions for precise fluid control in various applications. These manufacturers design, produce, and deliver cutting-edge electric flange ball valves that play a pivotal role in industries such as oil and gas, petrochemicals, and water treatment. In this article, we will explore the realm of electric flange ball valve ODM manufacturers, examining their significance, key attributes, and the crucial role they play in modern industrial processes.
The Significance of Electric Flange Ball Valve ODM Manufacturers
Electric flange ball valve ODM manufacturers are essential in addressing the increasing demand for high-performance fluid control solutions. Their significance goes beyond production; they are the architects of innovation and engineering excellence. Here's why they are indispensable:
Precision Control:These valves offer exceptional control over fluid flow, making them essential for processes where accuracy is paramount, such as chemical manufacturing and power generation.
Customization:Manufacturers often provide tailored solutions, allowing customers to specify valve parameters, materials, and features to meet the unique requirements of their applications.
Innovation:Manufacturers invest in research and development to create valves that provide not only precise control but also innovative features, materials, and designs that enhance overall system performance.
Technical Expertise:Electric flange ball valve ODM manufacturers employ skilled engineers and technicians with specialized knowledge of materials science, fluid dynamics, and automation technology, ensuring the design and production of high-quality valves.
Support and Maintenance:Many manufacturers offer comprehensive after-sales support, maintenance, and spare parts services, ensuring the longevity and peak performance of their valve products in fluid control systems.
Key Attributes of Electric Flange Ball Valve ODM Manufacturers
When evaluating electric flange ball valve ODM manufacturers, certain attributes distinguish industry leaders:
Experience:Established manufacturers often have a rich history of producing valves, demonstrating their expertise and reliability in the field of fluid control.
Quality Certifications:Recognized certifications, such as ISO 9001, indicate a manufacturer's commitment to quality and compliance with international standards in fluid control.
Product Range:A diverse product portfolio allows manufacturers to cater to various industries, applications, and unique specifications, all of which require precision and reliability in fluid control.
Innovation:Leading manufacturers invest in research and development to introduce innovative features, materials, and designs that enhance valve performance and reliability.
Global Reach:Manufacturers with a global presence can provide their electric flange ball valve ODM products and services to customers worldwide, ensuring accessibility and timely support.
Applications and Industries
Electric flange ball valve ODM manufacturers serve a wide range of applications within industries that demand precision and reliability in fluid control, including but not limited to:
Oil and Gas:For controlling the flow of various fluids in exploration, drilling, refining, and distribution processes.
Petrochemicals:In chemical processing plants that require precise control over chemical reactions and fluid flow.
Water Treatment:In municipal and industrial water treatment facilities for regulating water flow, chemical dosing, and filtration.
Power Generation:Ensuring the accuracy of fluid control in power plants for efficient and reliable energy production.
Food and Beverage:For controlling the flow of ingredients, liquids, and gases in food processing and bottling plants.
The Future of Electric Flange Ball Valve ODM Manufacturers
As industries continue to advance and prioritize precision, efficiency, and sustainability in fluid control, electric flange ball valve ODM manufacturers are poised for further growth and innovation. Anticipated future trends may include:
IoT Integration:Greater connectivity for real-time monitoring, data collection, and predictive maintenance of electric flange ball valves, enhancing overall system efficiency and reliability.
Enhanced Materials:Ongoing development of advanced materials and coatings for improved corrosion resistance and longevity in diverse industrial environments.
Energy Efficiency:Manufacturers will focus on reducing energy consumption and enhancing the energy efficiency of electric actuators in valve systems.
Environmental Sustainability:A growing emphasis on eco-friendly materials and processes to meet environmental goals while ensuring efficient and precise fluid control.
In conclusion, electric flange ball valve ODM manufacturers are essential contributors to modern industrial processes, offering high-quality, customizable solutions for precision fluid control needs across diverse industries. Their commitment to quality, innovation, and technical expertise ensures the reliability and efficiency of fluid control systems, making them vital partners in industrial efficiency and precision control worldwide.
Title:"Mastering Control: The World of Pneumatic Butterfly Valve ODM Manufacturers"
Pneumatic butterfly valve ODM (Original Design Manufacturer) companies are pivotal players in the world of industrial automation, providing essential solutions for precise fluid control across various industries. These manufacturers design, produce, and deliver cutting-edge pneumatic butterfly valves that play a crucial role in processes such as HVAC systems, water treatment, and food processing. In this article, we will explore the realm of pneumatic butterfly valve ODM manufacturers, examining their significance, key attributes, and the pivotal role they play in modern industrial processes.
The Significance of Pneumatic Butterfly Valve ODM Manufacturers
Pneumatic butterfly valve ODM manufacturers are instrumental in addressing the increasing demand for high-performance fluid control solutions. Their significance goes beyond production; they are the architects of innovation and engineering excellence. Here's why they are indispensable:
Precise Control:These valves offer exceptional control over fluid flow, making them essential for processes where accuracy is paramount, such as pharmaceutical manufacturing and chemical processing.
Customization:Manufacturers often provide tailored solutions, allowing customers to specify valve parameters, materials, and features to meet the unique requirements of their applications.
Innovation:Manufacturers invest in research and development to create valves that provide not only precise control but also innovative features, materials, and designs that enhance overall system performance.
Technical Expertise:Pneumatic butterfly valve ODM manufacturers employ skilled engineers and technicians with specialized knowledge of materials science, fluid dynamics, and automation technology, ensuring the design and production of high-quality valves.
Support and Maintenance:Many manufacturers offer comprehensive after-sales support, maintenance, and spare parts services, ensuring the longevity and peak performance of their valve products in fluid control systems.
Key Attributes of Pneumatic Butterfly Valve ODM Manufacturers
When evaluating pneumatic butterfly valve ODM manufacturers, certain attributes distinguish industry leaders:
Experience:Established manufacturers often have a rich history of producing valves, demonstrating their expertise and reliability in the field of fluid control.
Quality Certifications:Recognized certifications, such as ISO 9001, indicate a manufacturer's commitment to quality and compliance with international standards in fluid control.
Product Range:A diverse product portfolio allows manufacturers to cater to various industries, applications, and unique specifications, all of which require precision and reliability in fluid control.
Innovation:Leading manufacturers invest in research and development to introduce innovative features, materials, and designs that enhance valve performance and reliability.
Global Reach:Manufacturers with a global presence can provide their pneumatic butterfly valve ODM products and services to customers worldwide, ensuring accessibility and timely support.
Applications and Industries
Pneumatic butterfly valve ODM manufacturers serve a wide range of applications within industries that demand precision and reliability in fluid control, including but not limited to:
Water Treatment:In municipal and industrial water treatment facilities for regulating water flow, chemical dosing, and filtration.
HVAC Systems:Controlling the flow of air and water in heating, ventilation, and air conditioning systems for efficient temperature control.
Food and Beverage:For controlling the flow of ingredients, liquids, and gases in food processing and bottling plants, ensuring product quality and safety.
Pharmaceuticals:Ensuring the accuracy and sterility of pharmaceutical liquids in manufacturing processes.
Chemical Manufacturing:In chemical processing plants that require precise control over chemical reactions and fluid flow.
The Future of Pneumatic Butterfly Valve ODM Manufacturers
As industries continue to advance and prioritize precision, efficiency, and sustainability in fluid control, pneumatic butterfly valve ODM manufacturers are poised for further growth and innovation. Anticipated future trends may include:
IoT Integration:Greater connectivity for real-time monitoring, data collection, and predictive maintenance of pneumatic butterfly valves, enhancing overall system efficiency and reliability.
Enhanced Materials:Ongoing development of advanced materials and coatings for improved corrosion resistance and longevity in diverse industrial environments.
Energy Efficiency:Manufacturers will focus on reducing energy consumption and enhancing the energy efficiency of pneumatic actuators in valve systems.
Environmental Sustainability:A growing emphasis on eco-friendly materials and processes to meet environmental goals while ensuring efficient and precise fluid control.
In conclusion, pneumatic butterfly valve ODM manufacturers are essential contributors to modern industrial processes, offering high-quality, customizable solutions for precision fluid control needs across diverse industries. Their commitment to quality, innovation, and technical expertise ensures the reliability and efficiency of fluid control systems, making them vital partners in industrial efficiency and precision control worldwide.
Title:"Elevating Control: The World of Electric Single-Seat Regulating Valve ODM Manufacturers"
Electric single-seat regulating valve ODM (Original Design Manufacturer) companies are pivotal in the world of industrial automation, providing essential solutions for precise fluid control across various industries. These manufacturers design, produce, and deliver cutting-edge electric single-seat regulating valves that play a crucial role in processes such as chemical processing, power generation, and pharmaceutical manufacturing. In this article, we will explore the realm of electric single-seat regulating valve ODM manufacturers, examining their significance, key attributes, and the pivotal role they play in modern industrial processes.
The Significance of Electric Single-Seat Regulating Valve ODM Manufacturers
Electric single-seat regulating valve ODM manufacturers are instrumental in addressing the increasing demand for high-performance fluid control solutions. Their significance goes beyond production; they are the architects of innovation and engineering excellence. Here's why they are indispensable:
Precision Control:These valves offer exceptional control over fluid flow, making them essential for processes where accuracy is paramount, such as chemical reactions and flow control in pharmaceutical production.
Customization:Manufacturers often provide tailored solutions, allowing customers to specify valve parameters, materials, and features to meet the unique requirements of their applications.
Innovation:Manufacturers invest in research and development to create valves that provide not only precise control but also innovative features, materials, and designs that enhance overall system performance.
Technical Expertise:Electric single-seat regulating valve ODM manufacturers employ skilled engineers and technicians with specialized knowledge of materials science, fluid dynamics, and automation technology, ensuring the design and production of high-quality valves.
Support and Maintenance:Many manufacturers offer comprehensive after-sales support, maintenance, and spare parts services, ensuring the longevity and peak performance of their valve products in fluid control systems.
Key Attributes of Electric Single-Seat Regulating Valve ODM Manufacturers
When evaluating electric single-seat regulating valve ODM manufacturers, certain attributes distinguish industry leaders:
Experience:Established manufacturers often have a rich history of producing valves, demonstrating their expertise and reliability in the field of fluid control.
Quality Certifications:Recognized certifications, such as ISO 9001, indicate a manufacturer's commitment to quality and compliance with international standards in fluid control.
Product Range:A diverse product portfolio allows manufacturers to cater to various industries, applications, and unique specifications, all of which require precision and reliability in fluid control.
Innovation:Leading manufacturers invest in research and development to introduce innovative features, materials, and designs that enhance valve performance and reliability.
Global Reach:Manufacturers with a global presence can provide their electric single-seat regulating valve ODM products and services to customers worldwide, ensuring accessibility and timely support.
Applications and Industries
Electric single-seat regulating valve ODM manufacturers serve a wide range of applications within industries that demand precision and reliability in fluid control, including but not limited to:
Chemical Processing:For precise control of chemical reactions and the flow of various fluids in chemical manufacturing plants.
Power Generation:Ensuring the accuracy of fluid control in power plants for efficient and reliable energy production.
Pharmaceuticals:Ensuring the accuracy and sterility of pharmaceutical liquids in manufacturing processes.
Water Treatment:In municipal and industrial water treatment facilities for regulating water flow, chemical dosing, and filtration.
Food and Beverage:For controlling the flow of ingredients, liquids, and gases in food processing and bottling plants, ensuring product quality and safety.
The Future of Electric Single-Seat Regulating Valve ODM Manufacturers
As industries continue to advance and prioritize precision, efficiency, and sustainability in fluid control, electric single-seat regulating valve ODM manufacturers are poised for further growth and innovation. Anticipated future trends may include:
IoT Integration:Greater connectivity for real-time monitoring, data collection, and predictive maintenance of electric single-seat regulating valves, enhancing overall system efficiency and reliability.
Enhanced Materials:Ongoing development of advanced materials and coatings for improved corrosion resistance and longevity in diverse industrial environments.
Energy Efficiency:Manufacturers will focus on reducing energy consumption and enhancing the energy efficiency of electric actuators in valve systems.
Environmental Sustainability:A growing emphasis on eco-friendly materials and processes to meet environmental goals while ensuring efficient and precise fluid control.
In conclusion, electric single-seat regulating valve ODM manufacturers are essential contributors to modern industrial processes, offering high-quality, customizable solutions for precision fluid control needs across diverse industries. Their commitment to quality, innovation, and technical expertise ensures the reliability and efficiency of fluid control systems, making them vital partners in industrial efficiency and precision control worldwide.
Title:"Powering Innovation: The World of Lithium Battery Valve ODM Manufacturers"
Lithium battery valve ODM (Original Design Manufacturer) companies are at the forefront of technological advancement, providing critical solutions for the safe and efficient operation of lithium-ion batteries in various applications. These manufacturers design, produce, and deliver cutting-edge lithium battery valves that play a pivotal role in industries such as electric vehicles (EVs), renewable energy storage, and portable electronics. In this article, we will explore the realm of lithium battery valve ODM manufacturers, examining their significance, key attributes, and the crucial role they play in the modern world of energy storage and mobility.
The Significance of Lithium Battery Valve ODM Manufacturers
Lithium battery valve ODM manufacturers are instrumental in addressing the increasing demand for high-performance battery management solutions. Their significance goes beyond production; they are the architects of innovation and engineering excellence. Here's why they are indispensable:
Battery Safety:These valves are essential components for maintaining the safety and integrity of lithium-ion batteries, preventing overpressure, thermal runaway, and other potential hazards.
Customization:Manufacturers often provide tailored solutions, allowing customers to specify valve parameters, materials, and features to meet the unique requirements of their battery systems.
Innovation:Manufacturers invest in research and development to create valves that provide not only safety but also innovative features, materials, and designs that enhance battery performance and longevity.
Technical Expertise:Lithium battery valve ODM manufacturers employ skilled engineers and technicians with specialized knowledge of materials science, fluid dynamics, and battery technology, ensuring the design and production of high-quality valves.
Support and Maintenance:Many manufacturers offer comprehensive after-sales support, maintenance, and spare parts services, ensuring the longevity and peak performance of their valve products in battery management systems.
Key Attributes of Lithium Battery Valve ODM Manufacturers
When evaluating lithium battery valve ODM manufacturers, certain attributes distinguish industry leaders:
Experience:Established manufacturers often have a rich history of producing valves for lithium-ion batteries, demonstrating their expertise and reliability in the field of energy storage.
Quality Certifications:Recognized certifications, such as ISO 9001, indicate a manufacturer's commitment to quality and compliance with international standards in battery management.
Product Range:A diverse product portfolio allows manufacturers to cater to various lithium battery applications, from small consumer electronics to large-scale energy storage systems.
Innovation:Leading manufacturers invest in research and development to introduce innovative features, materials, and designs that enhance valve performance and reliability in battery management.
Global Reach:Manufacturers with a global presence can provide their lithium battery valve ODM products and services to customers worldwide, ensuring accessibility and timely support.
Applications and Industries
Lithium battery valve ODM manufacturers serve a wide range of applications within industries that rely on lithium-ion batteries for energy storage and mobility, including but not limited to:
Electric Vehicles (EVs):Ensuring the safety and performance of lithium-ion batteries in electric cars and e-bikes.
Renewable Energy Storage:Regulating the flow of energy in battery systems used in solar and wind energy storage.
Consumer Electronics:Enhancing the safety and efficiency of lithium-ion batteries in smartphones, laptops, and other portable devices.
Industrial and Grid Storage:Maintaining the integrity of large-scale battery arrays used in industrial settings and electrical grid management.
Aerospace:Ensuring the safety and reliability of lithium-ion batteries in spacecraft and aviation applications.
The Future of Lithium Battery Valve ODM Manufacturers
As industries continue to advance and prioritize energy efficiency and sustainability, lithium battery valve ODM manufacturers are poised for further growth and innovation. Anticipated future trends may include:
Advanced Materials:Ongoing development of materials and coatings for improved corrosion resistance and longevity in diverse battery management environments.
Smart Valve Technology:Integration of smart sensors and IoT connectivity for real-time monitoring, data collection, and predictive maintenance of lithium battery valves.
Energy Density Enhancement:Innovations aimed at increasing the energy density and performance of lithium-ion batteries, driving the need for more advanced valve solutions.
Environmental Sustainability:A growing emphasis on eco-friendly materials and processes to meet environmental goals while ensuring the safety and performance of lithium-ion batteries.
In conclusion, lithium battery valve ODM manufacturers are essential contributors to modern energy storage and mobility solutions, offering high-quality, customizable safety solutions for lithium-ion batteries across diverse industries. Their commitment to quality, innovation, and technical expertise ensures the reliability and safety of battery management systems, making them vital partners in the evolving landscape of energy storage and electric mobility.
Title:"Innovative Excellence: China's Leading Electric Stainless Steel Flange Ball Valve Manufacturer"
China has emerged as a global leader in industrial innovation, and this distinction extends to the realm of electric stainless steel flange ball valve manufacturing. With a commitment to precision engineering, reliability, and customization, Chinese manufacturers have been at the forefront of supplying cutting-edge solutions to industries worldwide. In this article, we will delve into the world of China's electric stainless steel flange ball valve manufacturers, exploring their significance, key attributes, and the pivotal role they play in modern industrial processes.
The Significance of Chinese Electric Stainless Steel Flange Ball Valve Manufacturers
Chinese electric stainless steel flange ball valve manufacturers are instrumental in addressing the growing global demand for high-performance fluid control solutions. Their significance goes beyond production; they are pioneers of innovation and engineering excellence. Here's why they are essential:
Precision Control:These valves offer exceptional control over fluid flow, making them crucial for applications where accuracy is paramount, such as petrochemical refining and pharmaceutical production.
Customization:Manufacturers often provide tailored solutions, allowing customers to specify valve parameters, materials, and features to meet the unique requirements of their applications.
Innovation:Chinese manufacturers invest heavily in research and development to create valves that not only provide precise control but also incorporate innovative features, materials, and designs that enhance overall system performance.
Technical Expertise:Electric stainless steel flange ball valve manufacturers in China employ skilled engineers and technicians with specialized knowledge in materials science, fluid dynamics, and automation technology, ensuring the design and production of high-quality valves.
Support and Maintenance:Many manufacturers offer comprehensive after-sales support, maintenance, and spare parts services, ensuring the longevity and peak performance of their valve products in fluid control systems.
Key Attributes of Chinese Electric Stainless Steel Flange Ball Valve Manufacturers
When evaluating Chinese electric stainless steel flange ball valve manufacturers, several attributes distinguish them as industry leaders:
Experience:Established manufacturers often have a rich history of producing valves, demonstrating their expertise and reliability in the field of fluid control.
Quality Certifications:Recognized certifications, such as ISO 9001, indicate a manufacturer's commitment to quality and compliance with international standards in fluid control.
Product Range:A diverse product portfolio allows manufacturers to cater to various industries, applications, and unique specifications, all of which require precision and reliability in fluid control.
Innovation:Leading Chinese manufacturers invest in research and development to introduce innovative features, materials, and designs that enhance valve performance and reliability.
Global Reach:Manufacturers with a global presence can provide their electric stainless steel flange ball valve products and services to customers worldwide, ensuring accessibility and timely support.
Applications and Industries
Chinese electric stainless steel flange ball valve manufacturers serve a wide range of applications within industries that demand precision and reliability in fluid control, including but not limited to:
Oil and Gas:For controlling the flow of various fluids in exploration, drilling, refining, and distribution processes.
Petrochemicals:In chemical processing plants that require precise control over chemical reactions and fluid flow.
Water Treatment:In municipal and industrial water treatment facilities for regulating water flow, chemical dosing, and filtration.
Pharmaceuticals:Ensuring the accuracy and sterility of pharmaceutical liquids in manufacturing processes.
Food and Beverage:For controlling the flow of ingredients, liquids, and gases in food processing and bottling plants, ensuring product quality and safety.
The Future of Chinese Electric Stainless Steel Flange Ball Valve Manufacturers
As industries continue to advance and prioritize precision, efficiency, and sustainability in fluid control, Chinese electric stainless steel flange ball valve manufacturers are poised for further growth and innovation. Anticipated future trends may include:
IoT Integration:Greater connectivity for real-time monitoring, data collection, and predictive maintenance of electric stainless steel flange ball valves, enhancing overall system efficiency and reliability.
Enhanced Materials:Ongoing development of advanced materials and coatings for improved corrosion resistance and longevity in diverse industrial environments.
Energy Efficiency:Manufacturers will focus on reducing energy consumption and enhancing the energy efficiency of electric actuators in valve systems.
Environmental Sustainability:A growing emphasis on eco-friendly materials and processes to meet environmental goals while ensuring efficient and precise fluid control.
In conclusion, China's electric stainless steel flange ball valve manufacturers are essential contributors to modern industrial processes, offering high-quality, customizable solutions for precision fluid control needs across diverse industries. Their commitment to quality, innovation, and technical expertise ensures the reliability and efficiency of fluid control systems, making them vital partners in industrial efficiency and precision control on a global scale.
Title:"Unveiling Excellence: China's Leading Electric Flange Ball Valve Manufacturer"
China has solidified its position as a global leader in industrial innovation, and its expertise extends into the realm of electric flange ball valve manufacturing. With a dedication to precision engineering, reliability, and customization, Chinese manufacturers have played a pivotal role in providing cutting-edge solutions to industries around the world. In this article, we will delve into the world of China's electric flange ball valve manufacturers, exploring their significance, key attributes, and the crucial role they play in modern industrial processes.
The Significance of Chinese Electric Flange Ball Valve Manufacturers
Chinese electric flange ball valve manufacturers are instrumental in addressing the growing global demand for high-performance fluid control solutions. Their significance goes beyond production; they are pioneers of innovation and engineering excellence. Here's why they are essential:
Precision Control:Electric flange ball valves offer exceptional control over fluid flow, making them crucial for applications where accuracy is paramount, such as oil and gas, chemical processing, and water treatment.
Customization:Manufacturers often provide tailored solutions, allowing customers to specify valve parameters, materials, and features to meet the unique requirements of their applications.
Innovation:Chinese manufacturers invest heavily in research and development to create valves that not only provide precise control but also incorporate innovative features, materials, and designs that enhance overall system performance.
Technical Expertise:Electric flange ball valve manufacturers in China employ skilled engineers and technicians with specialized knowledge in materials science, fluid dynamics, and automation technology, ensuring the design and production of high-quality valves.
Support and Maintenance:Many manufacturers offer comprehensive after-sales support, maintenance, and spare parts services, ensuring the longevity and peak performance of their valve products in fluid control systems.
Key Attributes of Chinese Electric Flange Ball Valve Manufacturers
When evaluating Chinese electric flange ball valve manufacturers, several attributes distinguish them as industry leaders:
Experience:Established manufacturers often have a rich history of producing valves, demonstrating their expertise and reliability in the field of fluid control.
Quality Certifications:Recognized certifications, such as ISO 9001, indicate a manufacturer's commitment to quality and compliance with international standards in fluid control.
Product Range:A diverse product portfolio allows manufacturers to cater to various industries, applications, and unique specifications, all of which require precision and reliability in fluid control.
Innovation:Leading Chinese manufacturers invest in research and development to introduce innovative features, materials, and designs that enhance valve performance and reliability.
Global Reach:Manufacturers with a global presence can provide their electric flange ball valve products and services to customers worldwide, ensuring accessibility and timely support.
Applications and Industries
Chinese electric flange ball valve manufacturers serve a wide range of applications within industries that demand precision and reliability in fluid control, including but not limited to:
Oil and Gas:For controlling the flow of various fluids in exploration, drilling, refining, and distribution processes.
Petrochemicals:In chemical processing plants that require precise control over chemical reactions and fluid flow.
Water Treatment:In municipal and industrial water treatment facilities for regulating water flow, chemical dosing, and filtration.
Pharmaceuticals:Ensuring the accuracy and sterility of pharmaceutical liquids in manufacturing processes.
Food and Beverage:For controlling the flow of ingredients, liquids, and gases in food processing and bottling plants, ensuring product quality and safety.
The Future of Chinese Electric Flange Ball Valve Manufacturers
As industries continue to advance and prioritize precision, efficiency, and sustainability in fluid control, Chinese electric flange ball valve manufacturers are poised for further growth and innovation. Anticipated future trends may include:
IoT Integration:Greater connectivity for real-time monitoring, data collection, and predictive maintenance of electric flange ball valves, enhancing overall system efficiency and reliability.
Enhanced Materials:Ongoing development of advanced materials and coatings for improved corrosion resistance and longevity in diverse industrial environments.
Energy Efficiency:Manufacturers will focus on reducing energy consumption and enhancing the energy efficiency of electric actuators in valve systems.
Environmental Sustainability:A growing emphasis on eco-friendly materials and processes to meet environmental goals while ensuring efficient and precise fluid control.
In conclusion, China's electric flange ball valve manufacturers are essential contributors to modern industrial processes, offering high-quality, customizable solutions for precision fluid control needs across diverse industries. Their commitment to quality, innovation, and technical expertise ensures the reliability and efficiency of fluid control systems, making them vital partners in industrial efficiency and precision control on a global scale.
Title:"Precision in Motion: China's Leading Electric Flanged Hard Seal Butterfly Valve Manufacturer"
China has firmly established itself as a global hub of industrial innovation, and this distinction extends to the realm of electric flanged hard seal butterfly valve manufacturing. With a commitment to precision engineering, reliability, and innovation, Chinese manufacturers have played a pivotal role in providing cutting-edge solutions to industries around the world. In this article, we will delve into the world of China's electric flanged hard seal butterfly valve manufacturers, exploring their significance, key attributes, and the crucial role they play in modern industrial processes.
The Significance of Chinese Electric Flanged Hard Seal Butterfly Valve Manufacturers
Chinese electric flanged hard seal butterfly valve manufacturers are instrumental in addressing the growing global demand for high-performance fluid control solutions. Their significance goes beyond production; they are pioneers of innovation and engineering excellence. Here's why they are essential:
Precision Control:Electric flanged hard seal butterfly valves offer exceptional control over fluid flow, making them crucial for applications where accuracy is paramount, such as oil and gas, chemical processing, and water treatment.
Customization:Manufacturers often provide tailored solutions, allowing customers to specify valve parameters, materials, and features to meet the unique requirements of their applications.
Innovation:Chinese manufacturers invest heavily in research and development to create valves that not only provide precise control but also incorporate innovative features, materials, and designs that enhance overall system performance.
Technical Expertise:Electric flanged hard seal butterfly valve manufacturers in China employ skilled engineers and technicians with specialized knowledge in materials science, fluid dynamics, and automation technology, ensuring the design and production of high-quality valves.
Support and Maintenance:Many manufacturers offer comprehensive after-sales support, maintenance, and spare parts services, ensuring the longevity and peak performance of their valve products in fluid control systems.
Key Attributes of Chinese Electric Flanged Hard Seal Butterfly Valve Manufacturers
When evaluating Chinese electric flanged hard seal butterfly valve manufacturers, several attributes distinguish them as industry leaders:
Experience:Established manufacturers often have a rich history of producing valves, demonstrating their expertise and reliability in the field of fluid control.
Quality Certifications:Recognized certifications, such as ISO 9001, indicate a manufacturer's commitment to quality and compliance with international standards in fluid control.
Product Range:A diverse product portfolio allows manufacturers to cater to various industries, applications, and unique specifications, all of which require precision and reliability in fluid control.
Innovation:Leading Chinese manufacturers invest in research and development to introduce innovative features, materials, and designs that enhance valve performance and reliability.
Global Reach:Manufacturers with a global presence can provide their electric flanged hard seal butterfly valve products and services to customers worldwide, ensuring accessibility and timely support.
Applications and Industries
Chinese electric flanged hard seal butterfly valve manufacturers serve a wide range of applications within industries that demand precision and reliability in fluid control, including but not limited to:
Oil and Gas:For controlling the flow of various fluids in exploration, drilling, refining, and distribution processes.
Petrochemicals:In chemical processing plants that require precise control over chemical reactions and fluid flow.
Water Treatment:In municipal and industrial water treatment facilities for regulating water flow, chemical dosing, and filtration.
Pharmaceuticals:Ensuring the accuracy and sterility of pharmaceutical liquids in manufacturing processes.
Food and Beverage:For controlling the flow of ingredients, liquids, and gases in food processing and bottling plants, ensuring product quality and safety.
The Future of Chinese Electric Flanged Hard Seal Butterfly Valve Manufacturers
As industries continue to advance and prioritize precision, efficiency, and sustainability in fluid control, Chinese electric flanged hard seal butterfly valve manufacturers are poised for further growth and innovation. Anticipated future trends may include:
IoT Integration:Greater connectivity for real-time monitoring, data collection, and predictive maintenance of electric flanged hard seal butterfly valves, enhancing overall system efficiency and reliability.
Enhanced Materials:Ongoing development of advanced materials and coatings for improved corrosion resistance and longevity in diverse industrial environments.
Energy Efficiency:Manufacturers will focus on reducing energy consumption and enhancing the energy efficiency of electric actuators in valve systems.
Environmental Sustainability:A growing emphasis on eco-friendly materials and processes to meet environmental goals while ensuring efficient and precise fluid control.
In conclusion, China's electric flanged hard seal butterfly valve manufacturers are essential contributors to modern industrial processes, offering high-quality, customizable solutions for precision fluid control needs across diverse industries. Their commitment to quality, innovation, and technical expertise ensures the reliability and efficiency of fluid control systems, making them vital partners in industrial efficiency and precision control on a global scale.
Title:"Leading the Flow: China's Premier Electric Single Seat Regulating Valve Manufacturer"
China has earned its reputation as a global industrial powerhouse, and this distinction extends to the realm of electric single-seat regulating valve manufacturing. With a steadfast dedication to precision engineering, reliability, and innovation, Chinese manufacturers have positioned themselves as leaders in providing cutting-edge solutions to industries around the world. In this article, we will explore the world of China's electric single-seat regulating valve manufacturers, examining their significance, key attributes, and the pivotal role they play in modern industrial processes.
The Significance of Chinese Electric Single Seat Regulating Valve Manufacturers
Chinese electric single-seat regulating valve manufacturers are instrumental in addressing the growing global demand for high-performance fluid control solutions. Their significance goes beyond production; they are pioneers of innovation and engineering excellence. Here's why they are indispensable:
Precision Control:Electric single-seat regulating valves offer exceptional control over fluid flow, making them indispensable for applications where accuracy is paramount, such as chemical processing, power generation, and pharmaceutical manufacturing.
Customization:Manufacturers often provide tailored solutions, enabling customers to specify valve parameters, materials, and features to meet the unique requirements of their applications.
Innovation:Chinese manufacturers invest substantially in research and development to create valves that provide precise control while incorporating innovative features, materials, and designs that enhance overall system performance.
Technical Expertise:Electric single-seat regulating valve manufacturers in China employ highly skilled engineers and technicians with specialized knowledge in materials science, fluid dynamics, and automation technology. This ensures the design and production of high-quality valves.
Support and Maintenance:Many manufacturers offer comprehensive after-sales support, maintenance, and spare parts services, ensuring the longevity and peak performance of their valve products in fluid control systems.
Key Attributes of Chinese Electric Single Seat Regulating Valve Manufacturers
When evaluating Chinese electric single-seat regulating valve manufacturers, several attributes distinguish them as industry leaders:
Experience:Established manufacturers often have a rich history of producing valves, demonstrating their expertise and reliability in the field of fluid control.
Quality Certifications:Recognized certifications, such as ISO 9001, indicate a manufacturer's commitment to quality and compliance with international standards in fluid control.
Product Range:A diverse product portfolio allows manufacturers to cater to various industries, applications, and unique specifications, all of which require precision and reliability in fluid control.
Innovation:Leading Chinese manufacturers invest in research and development to introduce innovative features, materials, and designs that enhance valve performance and reliability.
Global Reach:Manufacturers with a global presence can provide their electric single-seat regulating valve products and services to customers worldwide, ensuring accessibility and timely support.
Applications and Industries
Chinese electric single-seat regulating valve manufacturers serve a wide range of applications within industries that demand precision and reliability in fluid control, including but not limited to:
Chemical Processing:For precise control of chemical reactions and the flow of various fluids in chemical manufacturing plants.
Power Generation:Ensuring the accuracy of fluid control in power plants for efficient and reliable energy production.
Pharmaceuticals:Ensuring the accuracy and sterility of pharmaceutical liquids in manufacturing processes.
Water Treatment:In municipal and industrial water treatment facilities for regulating water flow, chemical dosing, and filtration.
Food and Beverage:For controlling the flow of ingredients, liquids, and gases in food processing and bottling plants, ensuring product quality and safety.
The Future of Chinese Electric Single Seat Regulating Valve Manufacturers
As industries continue to advance and prioritize precision, efficiency, and sustainability in fluid control, Chinese electric single-seat regulating valve manufacturers are poised for further growth and innovation. Anticipated future trends may include:
IoT Integration:Greater connectivity for real-time monitoring, data collection, and predictive maintenance of electric single-seat regulating valves, enhancing overall system efficiency and reliability.
Enhanced Materials:Ongoing development of advanced materials and coatings for improved corrosion resistance and longevity in diverse industrial environments.
Energy Efficiency:Manufacturers will focus on reducing energy consumption and enhancing the energy efficiency of electric actuators in valve systems.
Environmental Sustainability:A growing emphasis on eco-friendly materials and processes to meet environmental goals while ensuring efficient and precise fluid control.
In conclusion, China's electric single-seat regulating valve manufacturers are essential contributors to modern industrial processes, offering high-quality, customizable solutions for precision fluid control needs across diverse industries. Their commitment to quality, innovation, and technical expertise ensures the reliability and efficiency of fluid control systems, making them vital partners in industrial efficiency and precision control on a global scale.
Title:"Innovation in Motion: China's Leading Electric Three Eccentric Butterfly Valve Manufacturer"
China has earned its place as a global industrial leader, and this distinction extends to the domain of electric three eccentric butterfly valve manufacturing. With a steadfast commitment to precision engineering, reliability, and innovation, Chinese manufacturers have positioned themselves as pioneers in providing cutting-edge solutions to industries around the world. In this article, we will delve into the world of China's electric three eccentric butterfly valve manufacturers, exploring their significance, key attributes, and the vital role they play in modern industrial processes.
The Significance of Chinese Electric Three Eccentric Butterfly Valve Manufacturers
Chinese electric three eccentric butterfly valve manufacturers are pivotal in addressing the growing global demand for high-performance fluid control solutions. Their significance transcends production; they are trailblazers in innovation and engineering excellence. Here's why they are indispensable:
Precision Control:Electric three eccentric butterfly valves offer exceptional control over fluid flow, making them indispensable for applications where precision and reliability are paramount, such as oil and gas, power generation, and chemical processing.
Customization:Manufacturers often provide tailored solutions, enabling customers to specify valve parameters, materials, and features to meet the unique requirements of their applications.
Innovation:Chinese manufacturers invest significantly in research and development to create valves that provide precise control while incorporating innovative features, materials, and designs that enhance overall system performance.
Technical Expertise:Electric three eccentric butterfly valve manufacturers in China employ highly skilled engineers and technicians with specialized knowledge in materials science, fluid dynamics, and automation technology. This ensures the design and production of high-quality valves.
Support and Maintenance:Many manufacturers offer comprehensive after-sales support, maintenance, and spare parts services, ensuring the longevity and peak performance of their valve products in fluid control systems.
Key Attributes of Chinese Electric Three Eccentric Butterfly Valve Manufacturers
When evaluating Chinese electric three eccentric butterfly valve manufacturers, several attributes distinguish them as industry leaders:
Experience:Established manufacturers often have a rich history of producing valves, showcasing their expertise and reliability in the field of fluid control.
Quality Certifications:Recognized certifications, such as ISO 9001, attest to a manufacturer's commitment to quality and compliance with international standards in fluid control.
Product Range:A diverse product portfolio allows manufacturers to cater to various industries, applications, and unique specifications, all of which require precision and reliability in fluid control.
Innovation:Leading Chinese manufacturers invest in research and development to introduce innovative features, materials, and designs that enhance valve performance and reliability.
Global Reach:Manufacturers with a global presence can provide their electric three eccentric butterfly valve products and services to customers worldwide, ensuring accessibility and timely support.
Applications and Industries
Chinese electric three eccentric butterfly valve manufacturers serve a wide range of applications within industries that demand precision and reliability in fluid control, including but not limited to:
Oil and Gas:For controlling the flow of various fluids in exploration, drilling, refining, and distribution processes.
Power Generation:Ensuring the accuracy of fluid control in power plants for efficient and reliable energy production.
Chemical Processing:For precise control of chemical reactions and the flow of various fluids in chemical manufacturing plants.
Water Treatment:In municipal and industrial water treatment facilities for regulating water flow, chemical dosing, and filtration.
Metals and Mining:For controlling the flow of slurry and other abrasive materials in mining and metallurgical processes.
The Future of Chinese Electric Three Eccentric Butterfly Valve Manufacturers
As industries continue to advance and prioritize precision, efficiency, and sustainability in fluid control, Chinese electric three eccentric butterfly valve manufacturers are poised for further growth and innovation. Anticipated future trends may include:
IoT Integration:Greater connectivity for real-time monitoring, data collection, and predictive maintenance of electric three eccentric butterfly valves, enhancing overall system efficiency and reliability.
Enhanced Materials:Ongoing development of advanced materials and coatings for improved corrosion resistance and longevity in diverse industrial environments.
Energy Efficiency:Manufacturers will focus on reducing energy consumption and enhancing the energy efficiency of electric actuators in valve systems.
Environmental Sustainability:A growing emphasis on eco-friendly materials and processes to meet environmental goals while ensuring efficient and precise fluid control.
In conclusion, China's electric three eccentric butterfly valve manufacturers are indispensable contributors to modern industrial processes, offering high-quality, customizable solutions for precision fluid control needs across diverse industries. Their commitment to quality, innovation, and technical expertise ensures the reliability and efficiency of fluid control systems, making them vital partners in industrial efficiency and precision control on a global scale.
Title:"Precision in Control: The Versatile Electric Single Seat Regulating Valve"
Introduction:
In the world of fluid control systems, precision is paramount. Industries ranging from petrochemicals to pharmaceuticals rely on efficient and accurate control of fluid flows to ensure the safety, quality, and efficiency of their processes. At the heart of this precision is the electric single seat regulating valve. In this article, we will explore the significance, key attributes, and diverse applications of the electric single seat regulating valve.
The Significance of Electric Single Seat Regulating Valves
Electric single seat regulating valves play a pivotal role in modern industrial processes, offering precise control over the flow of fluids, gases, and steam. Their significance lies in their ability to:
Achieve Precision Control:These valves excel in applications where accuracy is crucial, such as maintaining precise temperatures, pressures, and flow rates. Industries like pharmaceuticals, food and beverage, and HVAC rely on their precise control capabilities.
Ensure Process Efficiency:By fine-tuning fluid flow, electric single seat regulating valves help industries optimize their processes, reduce energy consumption, and enhance overall efficiency.
Enhance Safety:In industries like chemicals and oil and gas, maintaining strict control over fluid flow is vital to prevent accidents and ensure worker safety.
Comply with Regulations:Many industries operate under stringent regulatory requirements, and these valves aid in meeting compliance standards by providing accurate control and monitoring.
Key Attributes of Electric Single Seat Regulating Valves
When evaluating electric single seat regulating valves, several key attributes distinguish them as essential components of fluid control systems:
Precise Modulation:These valves offer precise modulation, allowing for fine adjustments in flow rates and pressure, making them ideal for applications that require tight control.
Versatility:Electric single seat regulating valves can be customized to suit various applications and industries, thanks to their adaptability to different flow media and conditions.
Highly Reliable:Manufacturers often build these valves with durability and longevity in mind, ensuring reliable performance even in demanding industrial environments.
Remote Control:Electric actuators enable remote control and automation, making it easier to integrate these valves into complex systems and enabling real-time adjustments.
Low Maintenance:Properly maintained, these valves can operate efficiently for extended periods, reducing downtime and maintenance costs.
Applications Across Industries
Electric single seat regulating valves find applications across a spectrum of industries, including:
Pharmaceuticals:Ensuring precise dosing and control of ingredients and solvents in pharmaceutical manufacturing.
Food and Beverage:Regulating the flow of liquids and gases in food processing, ensuring consistent product quality.
Petrochemicals:Controlling the flow of chemicals, gases, and feedstock in refining and chemical manufacturing.
Power Generation:Maintaining precise control over steam and cooling water flows in power plants.
HVAC:Regulating heating and cooling fluids in commercial and residential HVAC systems for energy efficiency.
Water Treatment:Controlling the flow of water, chemicals, and filtration processes in water treatment facilities.
The Future of Electric Single Seat Regulating Valves
As industries continue to advance, electric single seat regulating valves will evolve to meet changing demands. Future trends may include:
Smart Valve Technology:Integration with IoT and AI for real-time monitoring and predictive maintenance.
Enhanced Materials:Development of advanced materials for improved durability and corrosion resistance.
Energy Efficiency:Greater focus on reducing energy consumption and enhancing valve actuator efficiency.
Sustainability:Eco-friendly valve materials and processes to align with environmental goals.
In conclusion, electric single seat regulating valves are indispensable assets in fluid control systems across industries. Their precision, reliability, and adaptability ensure that modern industrial processes operate efficiently, safely, and in compliance with regulatory standards. As technology continues to advance, these valves will remain at the forefront of precision fluid control, driving innovation and efficiency in diverse sectors.
Title:"Mounted Electric Eccentric Half Ball Valve: Precision in Fluid Control"
Introduction:
Fluid control is at the heart of many industrial processes, and the quest for precision and efficiency is a constant endeavor. Among the array of valves designed to meet these demands, the mounted electric eccentric half ball valve stands out as a versatile and reliable choice. In this article, we will explore the significance, key attributes, and wide-ranging applications of the mounted electric eccentric half ball valve.
The Significance of Mounted Electric Eccentric Half Ball Valves
Mounted electric eccentric half ball valves are critical components in industries where precise control over fluid flow is essential. Their significance lies in their ability to:
Provide Exceptional Control:These valves excel in applications where precise modulation of flow is required, ensuring accurate control of fluid volumes, temperatures, and pressures.
Maximize Efficiency:By facilitating rapid open-close cycles and precise throttling, mounted electric eccentric half ball valves help industries optimize their processes, reduce energy consumption, and enhance overall efficiency.
Enhance Safety:Industries like oil and gas rely on these valves to maintain strict control over fluid flow, contributing to accident prevention and worker safety.
Ensure Compliance:In sectors with stringent regulatory requirements, these valves help meet standards by providing reliable and precise control while enabling remote monitoring.
Key Attributes of Mounted Electric Eccentric Half Ball Valves
Several key attributes distinguish mounted electric eccentric half ball valves as indispensable components in fluid control systems:
Eccentric Design:The eccentric geometry of the ball allows for precise control, even in high-velocity and high-pressure applications, reducing wear and extending valve lifespan.
Bi-Directional Sealing:These valves offer tight sealing in both directions, minimizing leakage and ensuring secure isolation of fluids.
Highly Durable:Manufacturers often construct these valves from durable materials, making them reliable even in harsh industrial environments.
Adaptability:The versatility of these valves makes them suitable for various media types, including liquids, gases, and slurries, in a wide range of temperatures and pressures.
Remote Control:Electric actuators enable remote control and automation, making it easier to integrate these valves into complex systems and enabling real-time adjustments.
Applications Across Industries
Mounted electric eccentric half ball valves find applications across a multitude of industries, including:
Oil and Gas:Controlling the flow of crude oil, natural gas, and various fluids in exploration, drilling, refining, and distribution processes.
Chemical Processing:Regulating the flow of chemicals, solvents, and reactive substances in chemical manufacturing and petrochemical plants.
Water Treatment:Ensuring precise control over water flow, chemical dosing, and filtration processes in municipal and industrial water treatment facilities.
Power Generation:Managing steam, cooling water, and fuel flows in power plants for efficient energy production.
Mining and Minerals:Handling abrasive slurries and mineral processing fluids in mining and metallurgical operations.
The Future of Mounted Electric Eccentric Half Ball Valves
As industries continue to advance, mounted electric eccentric half ball valves will evolve to meet emerging demands. Future trends may include:
Advanced Materials:Development of novel materials and coatings for improved durability, corrosion resistance, and extended valve lifespan.
Digitalization:Integration with IoT and AI technologies for real-time monitoring, data analytics, and predictive maintenance.
Energy Efficiency:Greater emphasis on reducing energy consumption through improved valve actuator efficiency.
Environmental Sustainability:Adoption of eco-friendly materials and processes to align with sustainability goals.
In conclusion, mounted electric eccentric half ball valves are integral to modern fluid control systems across diverse industries. Their precise control, reliability, and adaptability ensure that industrial processes operate efficiently, safely, and in compliance with regulatory standards. As technology continues to advance, these valves will remain at the forefront of precision fluid control, driving innovation and efficiency in various sectors.
Title:"Explosion-Proof Damper Actuators: Ensuring Safety and Control in Hazardous Environments"
Introduction:
In industrial settings, especially those dealing with hazardous materials or environments, safety and precise control are paramount. Explosion-proof damper actuators play a critical role in achieving these objectives. These specialized devices provide the ability to control dampers and maintain the safety and efficiency of processes in environments where explosive gases or materials are present. In this article, we will explore the significance, key attributes, and applications of explosion-proof damper actuators.
The Significance of Explosion-Proof Damper Actuators
Explosion-proof damper actuators are vital components in industries where safety takes precedence. Their significance lies in their ability to:
Mitigate Hazards:In environments where explosive gases or dust are present, these actuators ensure that the operation of dampers is controlled safely to prevent potential accidents or explosions.
Enable Remote Control:Explosion-proof actuators can be operated remotely, allowing for precise and safe control even in dangerous settings.
Enhance Efficiency:By controlling airflow and gas flow, these actuators help industries optimize processes, reduce energy consumption, and improve overall efficiency.
Compliance Assurance:Many industries operate under strict regulatory standards. Explosion-proof damper actuators help meet these standards by providing safe and precise control while ensuring compliance.
Key Attributes of Explosion-Proof Damper Actuators
Several key attributes distinguish explosion-proof damper actuators as essential components in hazardous environments:
Explosion-Proof Design:These actuators are specifically designed to prevent explosions by containing any potential sparks or heat sources within a sealed housing.
Durable Construction:Manufacturers use robust materials that can withstand harsh conditions and maintain reliable performance.
Remote Operation:Explosion-proof damper actuators are often equipped with remote control capabilities, making them suitable for integration into complex systems.
Certifications:These actuators undergo rigorous testing and receive certifications to ensure they meet the necessary safety and quality standards.
Compatibility:They are compatible with a wide range of damper types and sizes, making them versatile for various applications.
Applications Across Industries
Explosion-proof damper actuators find applications in industries where safety and precise control are imperative, including:
Oil and Gas:Controlling dampers in facilities where explosive gases are present, such as refineries, petrochemical plants, and offshore drilling rigs.
Chemical Processing:Regulating airflow in processes involving flammable or volatile chemicals.
Mining:Controlling ventilation systems in mines, where explosive gases and dust can pose significant risks.
Wastewater Treatment:Managing airflow and gas control in sewage treatment facilities.
Power Generation:Ensuring safety and efficiency in power plants, especially those using combustible fuels.
The Future of Explosion-Proof Damper Actuators
As industries continue to advance and prioritize safety and efficiency, explosion-proof damper actuators will evolve to meet new demands. Future trends may include:
Smart Technology Integration:Incorporating IoT and AI for real-time monitoring, predictive maintenance, and data analytics to enhance safety and efficiency.
Energy Efficiency:Greater focus on reducing energy consumption through improved actuator designs and control algorithms.
Environmental Sustainability:Adoption of eco-friendly materials and processes to align with sustainability goals.
In conclusion, explosion-proof damper actuators are indispensable assets in ensuring safety and precise control in hazardous environments across various industries. Their ability to mitigate risks, enhance efficiency, and enable remote control makes them critical components in achieving operational excellence while prioritizing safety in challenging settings. As technology continues to advance, these actuators will remain at the forefront of safety and control solutions in hazardous environments.
Title:"Explosion-Proof Intelligent Integrated Actuator: The Future of Safe and Smart Automation"
Introduction:
In today's industrial landscape, the demand for both safety and efficiency is non-negotiable. Industries dealing with hazardous environments, such as oil and gas, petrochemicals, and mining, require automation solutions that prioritize safety while enhancing operational control. The explosion-proof intelligent integrated actuator has emerged as a game-changer in these industries, combining advanced automation with a focus on safety. In this article, we will delve into the significance, key attributes, and diverse applications of the explosion-proof intelligent integrated actuator.
The Significance of Explosion-Proof Intelligent Integrated Actuators
Explosion-proof intelligent integrated actuators hold immense significance in industries where safety is paramount. Their importance lies in their unique ability to:
Mitigate Hazardous Risks:In environments with explosive gases or materials, these actuators provide automation capabilities without compromising safety, preventing potential accidents or explosions.
Enable Smart Control:Combining automation and intelligence, these actuators allow for real-time monitoring, data analytics, and precise control in hazardous settings.
Enhance Efficiency:By optimizing processes, reducing energy consumption, and ensuring precise control, these actuators contribute to improved operational efficiency.
Compliance Assurance:Many industries operate under stringent safety and regulatory standards, and explosion-proof intelligent integrated actuators help meet these standards by ensuring safe and precise control while maintaining compliance.
Key Attributes of Explosion-Proof Intelligent Integrated Actuators
Several key attributes distinguish explosion-proof intelligent integrated actuators as essential components in hazardous environments:
Explosion-Proof Design:These actuators are purpose-built to contain potential sparks or heat sources within a sealed housing, eliminating the risk of ignition in explosive atmospheres.
Intelligent Control:Equipped with advanced control systems and sensors, they offer real-time monitoring and automation capabilities, allowing for smarter and more efficient operations.
Durable Construction:Manufacturers utilize robust materials to ensure these actuators can withstand harsh environmental conditions while maintaining reliable performance.
Certifications:They undergo rigorous testing and receive certifications to verify their compliance with stringent safety and quality standards.
Adaptability:Explosion-proof intelligent integrated actuators are versatile and can be customized for various applications and industries, making them suitable for a wide range of scenarios.
Applications Across Industries
Explosion-proof intelligent integrated actuators find applications in industries where safety and precise control are non-negotiable, including:
Oil and Gas:Controlling valves and equipment in refineries, drilling platforms, and processing facilities where explosive gases are present.
Petrochemicals:Regulating the flow of volatile chemicals and maintaining safety in chemical manufacturing plants.
Mining:Managing ventilation systems and equipment in mines, where explosive gases and dust pose significant risks.
Wastewater Treatment:Optimizing control and safety in sewage treatment plants.
Power Generation:Ensuring safety and efficiency in power plants, particularly those using combustible fuels.
The Future of Explosion-Proof Intelligent Integrated Actuators
As industries continue to advance and prioritize both safety and efficiency, explosion-proof intelligent integrated actuators will evolve to meet new demands. Future trends may include:
Advanced Connectivity:Enhanced integration with IoT and AI technologies for real-time monitoring, predictive maintenance, and data-driven decision-making.
Energy Efficiency:Continued focus on reducing energy consumption through improved actuator designs and control algorithms.
Environmental Sustainability:Adoption of eco-friendly materials and processes to align with sustainability goals while maintaining safety and efficiency.
In conclusion, explosion-proof intelligent integrated actuators represent a significant advancement in safety and control automation, particularly in hazardous environments. Their ability to mitigate risks, enhance efficiency, and enable smart control positions them as indispensable assets for industries prioritizing both safety and operational excellence. As technology continues to advance, these actuators will remain at the forefront of safe and intelligent automation solutions in hazardous settings.
Title:"Safety Meets Precision: The Evolution of Explosion-Proof Electric Bellows Stop Valves"
Introduction:
In industries where volatile and hazardous substances are part of the daily operation, safety is paramount. The explosion-proof electric bellows stop valve has emerged as a critical component, offering a seamless blend of precision control and safety in high-risk environments. This article will explore the significance, key attributes, and applications of explosion-proof electric bellows stop valves, shedding light on their role in ensuring both safety and operational excellence.
The Significance of Explosion-Proof Electric Bellows Stop Valves
Explosion-proof electric bellows stop valves hold immense significance in industries where safety is not negotiable. Their importance is deeply rooted in their ability to:
Mitigate Explosive Hazards:In settings where explosive gases or materials are present, these valves ensure safety by preventing ignition sources, minimizing the risk of catastrophic accidents.
Provide Precise Control:Bellows stop valves are well-suited for applications that require precise flow control, helping industries maintain accurate pressure, temperature, and flow rates.
Enhance Efficiency:By fine-tuning fluid flow, these valves optimize processes, reduce energy consumption, and enhance overall operational efficiency.
Ensure Regulatory Compliance:Many industries must adhere to strict safety and environmental regulations. Explosion-proof electric bellows stop valves help meet these standards by ensuring safe and precise control while maintaining compliance.
Key Attributes of Explosion-Proof Electric Bellows Stop Valves
Several key attributes set explosion-proof electric bellows stop valves apart as essential components in hazardous environments:
Explosion-Proof Design:These valves are meticulously engineered to prevent sparks or heat sources from escaping the valve housing, effectively eliminating the risk of ignition in explosive atmospheres.
Bellows Technology:The bellows actuator provides precise and reliable control, making these valves suitable for critical applications that demand accurate modulation.
Durable Construction:Manufacturers use robust materials that can withstand corrosive substances and harsh conditions while maintaining reliable performance.
Remote Control Capability:Electric actuation enables remote control and automation, making it easier to integrate these valves into complex systems and enabling real-time adjustments.
Certifications:Explosion-proof electric bellows stop valves undergo rigorous testing and certification to ensure their compliance with stringent safety and quality standards.
Applications Across Industries
Explosion-proof electric bellows stop valves find applications across a spectrum of industries where safety and precision control are paramount, including:
Oil and Gas:Controlling the flow of volatile substances in refineries, drilling platforms, and processing facilities where explosive gases are present.
Chemical Processing:Regulating the flow of hazardous chemicals, solvents, and reactive substances in chemical manufacturing plants.
Mining:Managing ventilation systems and controlling the flow of gases in mines, where explosive gases and dust pose significant risks.
Power Generation:Ensuring safety and efficiency in power plants, particularly those using combustible fuels.
Petrochemicals:Maintaining precise control in petrochemical plants, where safety and precise control are non-negotiable.
The Future of Explosion-Proof Electric Bellows Stop Valves
As industries continue to evolve and emphasize safety, explosion-proof electric bellows stop valves will continue to adapt to meet emerging demands. Future trends may include:
Advanced Connectivity:Enhanced integration with IoT and AI technologies for real-time monitoring, predictive maintenance, and data-driven decision-making.
Energy Efficiency:Ongoing focus on reducing energy consumption through improved valve actuator efficiency and control algorithms.
Environmental Sustainability:Adoption of eco-friendly materials and processes to align with sustainability goals while maintaining safety and efficiency.
In conclusion, explosion-proof electric bellows stop valves represent the pinnacle of safety and precision control in hazardous environments. Their ability to mitigate risks, enhance efficiency, and enable remote control positions them as indispensable assets for industries prioritizing safety and operational excellence. As technology continues to advance, these valves will remain at the forefront of safety and precision control solutions in high-risk settings.
Title:"Explosion-Proof Electric Sludge Discharge Valve: Safeguarding Industrial Processes"
Introduction:
In industries where the handling of hazardous materials and substances is routine, ensuring safety is paramount. The explosion-proof electric sludge discharge valve has emerged as a critical component in maintaining both safety and operational efficiency. This article explores the significance, key attributes, and applications of explosion-proof electric sludge discharge valves, shedding light on their pivotal role in safeguarding industrial processes.
The Significance of Explosion-Proof Electric Sludge Discharge Valves
Explosion-proof electric sludge discharge valves play an indispensable role in industries where safety is non-negotiable. Their significance lies in their unique ability to:
Mitigate Explosive Hazards:In environments with explosive gases or materials, these valves provide a secure means of managing sludge discharge without the risk of ignition or catastrophic accidents.
Ensure Precise Control:Sludge discharge is a critical process in many industries. These valves allow for accurate control, maintaining optimal flow rates and process conditions.
Enhance Operational Efficiency:By facilitating the efficient removal of sludge and waste materials, these valves contribute to process optimization, reduce downtime, and improve overall efficiency.
Compliance Assurance:Industries with stringent safety and environmental regulations benefit from explosion-proof electric sludge discharge valves, which ensure safe and compliant operations.
Key Attributes of Explosion-Proof Electric Sludge Discharge Valves
Several key attributes distinguish explosion-proof electric sludge discharge valves as essential components in hazardous environments:
Explosion-Proof Design:These valves are engineered to prevent sparks, heat, or electrical faults from igniting surrounding explosive atmospheres, ensuring safety during sludge discharge.
Robust Construction:Manufacturers use durable materials that can withstand corrosive substances and harsh conditions, ensuring reliable performance over time.
Remote Control Capability:Electric actuation allows for remote control and automation, simplifying integration into complex systems and enabling real-time adjustments.
Certifications:Explosion-proof electric sludge discharge valves undergo rigorous testing and certification to ensure they meet stringent safety and quality standards.
Customizability:They can be tailored to meet specific industry needs, including variations in size, material, and flow capacity.
Applications Across Industries
Explosion-proof electric sludge discharge valves find applications across various industries where safety and precise control are paramount, including:
Oil and Gas:Managing the safe discharge of sludge and waste materials in refineries, drilling platforms, and processing facilities where explosive gases are present.
Chemical Processing:Ensuring the safe removal of hazardous waste materials, chemicals, and by-products in chemical manufacturing plants.
Mining:Facilitating the efficient disposal of slurry and waste materials in mining and mineral processing operations.
Wastewater Treatment:Maintaining safe and efficient sludge removal in sewage treatment plants.
The Future of Explosion-Proof Electric Sludge Discharge Valves
As industries continue to advance and prioritize both safety and operational efficiency, explosion-proof electric sludge discharge valves will evolve to meet new demands. Future trends may include:
Advanced Connectivity:Integration with IoT and AI technologies for real-time monitoring, predictive maintenance, and data-driven decision-making.
Energy Efficiency:Enhanced actuator designs and control algorithms to reduce energy consumption during sludge discharge.
Environmental Sustainability:Adoption of eco-friendly materials and processes to align with sustainability goals while maintaining safety and efficiency.
In conclusion, explosion-proof electric sludge discharge valves are indispensable for ensuring safety and efficiency in hazardous environments across various industries. Their ability to mitigate risks, enhance efficiency, and enable remote control positions them as essential assets for industries prioritizing both safety and operational excellence. As technology continues to advance, these valves will remain at the forefront of safety and precision control solutions in high-risk settings.
引言:
在如今的工业和商业环境中,有很多应用场景需要灯具能够在恶劣条件下可靠运行。无论是在油田、化工厂、采矿场所还是户外建筑工地,LED三防灯都成为了关键的照明解决方案。本文将深入探讨LED三防灯的重要性、关键特点以及广泛的应用领域,揭示它们在极端环境中扮演的关键角色。
LED三防灯的重要性
LED三防灯在需要强大耐用性和稳定性的恶劣环境中***关重要。它们的重要性在于:
确保工作安全:在油田、化工工厂或采矿场等危险环境中,确保良好的照明是关系到工人生命安全的问题。
提供可靠照明:LED三防灯具备高度的稳定性和可靠性,能够在恶劣条件下持续提供均匀的照明,不受振动、湿度或温度变化的影响。
减少能源消耗:它们采用LED技术,能够显著减少能源消耗,有助于降低运营成本。
满足法规标准:在许多工业领域,符合法规标准是必要的,LED三防灯的设计使其符合相关法规和安全标准。
LED三防灯的关键特点
LED三防灯的关键特点使它们成为极端环境下不可或缺的照明设备:
防爆设计:这些灯具采用特殊设计,能够有效防止火花或高温点的产生,从而在易燃环境中确保安全。
耐用性:制造商采用坚固的材料,使这些灯具能够抵御腐蚀、震动和恶劣天气条件,确保长期可靠运行。
节能:LED技术的采用不仅提供了均匀的照明,还显著降低了能源消耗,有助于降低运营成本。
多功能性:它们通常具有可调光、遥控和智能控制功能,使其适用于各种照明需求。
LED三防灯的应用领域
LED三防灯广泛应用于需要高度安全性和可靠性的各种领域,包括:
油田和石油化工:提供安全的照明,确保工作人员在潜在的危险环境中能够清晰地看到操作。
采矿业:在地下矿山和露天矿山中提供可靠的照明,确保工作人员的安全和高效工作。
化工工厂:在处理危险化学品和材料的工业环境中提供照明。
建筑工地:在户外建筑工地提供坚固的照明设备,应对各种天气条件。
LED三防灯的未来
随着工业的不断发展和安全性的不断强调,LED三防灯将不断演进,以满足新的需求。未来的趋势可能包括:
智能化:更多的智能控制功能,例如远程监控、自动化和能源管理,以提高效率和安全性。
环保:采用更多的环保材料和技术,以减少对环境的影响,同时保持高效性。
更广泛的应用:LED三防灯将进一步扩展到更多领域,满足各种需求。
总之,LED三防灯在极端环境下的安全和高效照明解决方案中发挥着关键作用。它们的能力可以降低风险、提高工作效率,并确保工业过程的顺畅运行。随着技术的不断进步,LED三防灯将继续在各种恶劣条件下提供可靠的照
标题:LED三防灯:照亮安全与可靠之路
引言:
在现代工业和商业环境中,对于可靠且安全的照明需求日益增加。特别是在那些恶劣的条件下,如油田、化工厂、采矿场地以及户外施工现场,我们需要能够在极端环境下运行的照明解决方案。LED三防灯已经成为满足这些需求的关键设备。本文将深入探讨LED三防灯的重要性、关键特点以及广泛的应用领域,以阐明它们在确保安全和提高工作效率方面的关键作用。
LED三防灯的重要性
在需要强大耐用性和可靠性的危险环境中,LED三防灯具有极其重要的地位。它们的重要性在于:
确保工作安全:在油田、化工厂或采矿场等危险环境中,良好的照明对于工人的安全***关重要。
提供可靠照明:LED三防灯具有高度稳定性和可靠性,能够在恶劣条件下提供均匀的照明,不受振动、湿度或温度变化的影响。
降低能源消耗:采用LED技术,大幅降低能源消耗,有助于降低运营成本。
符合法规标准:在许多工业领域,符合法规标准是必要的,LED三防灯的设计使其符合相关的法规和安全标准。
LED三防灯的关键特点
LED三防灯具有许多关键特点,使其成为极端环境下不可或缺的照明设备:
防爆设计:这些灯具采用特殊设计,能够有效防止火花、高温点或电气故障引发爆炸,确保了在易燃环境中的安全。
耐用性:制造商采用坚固的材料,使这些灯具能够抵御腐蚀、震动和恶劣天气条件,确保长期可靠运行。
节能:采用LED技术,不仅提供均匀的照明,还显著降低了能源消耗,有助于降低运营成本。
多功能性:它们通常具有可调光、遥控和智能控制功能,使其适用于各种照明需求。
LED三防灯的应用领域
LED三防灯广泛应用于需要高度安全性和可靠性的各种领域,包括:
油田和石油化工:提供安全的照明,确保工作人员在潜在的危险环境中能够清晰地看到操作。
采矿业:在地下矿山和露天矿山中提供可靠的照明,确保工作人员的安全和高效工作。
化工工厂:在处理危险化学品和材料的工业环境中提供照明。
建筑工地:在户外建筑工地提供坚固的照明设备,应对各种天气条件。
LED三防灯的未来
随着工业的不断发展和安全性的不断强调,LED三防灯将不断演进,以满足新的需求。未来的趋势可能包括:
智能化:更多的智能控制功能,例如远程监控、自动化和能源管理,以提高效率和安全性。
环保:采用更多的环保材料和技术,以减少对环境的影响,同时保持高效性。
更广泛的应用:LED三防灯将进一步扩展到更多领域,满足各种需求。
总之,LED三防灯在极端环境下的安全和高效照明解决方案中发挥着关键作用。它们的能力可以降低风险、提高工作效率,并确保工业过程的顺畅运行。随着技术的不断进步,LED三防灯将继续在各种恶劣条件下提供可靠的照明解决方案。
引言:
随着工业、采矿和化工领域的不断发展,对安全和可靠的照明需求变得日益重要。在这些高风险的环境中,led防爆灯成为了不可或缺的照明解决方案,其背后是一批专业的厂家,致力于提供***的产品。本文将深入探讨LED防爆灯厂家的关键作用、主要特点以及其在安全照明领域的广泛应用。 LED防爆灯厂家在保障工业安全方面发挥着关键作用,其重要性在于: 提供高质量产品:厂家通过先进的研发和生产工艺,确保led防爆灯具备出色的性能和耐用性,以应对极端条件下的工作环境。 符合标准和法规:厂家确保其产品符合国际安全标准和法规,为客户提供合规的照明解决方案。
技术支持和服务:厂家提供技术支持和售后服务,以确保LED防爆灯的正常运行,并在需要时进行维护和维修。
定制解决方案:厂家通常能够根据客户的具体需求,提供定制化的照明解决方案,以满足不同行业和应用的要求。
LED防爆灯的主要特点
LED防爆灯具有一些关键特点,使其在安全照明领域脱颖而出:
防爆设计:这些灯具经过特殊设计,能够在易燃气体或粉尘存在的危险环境中工作,而不会引发火花或爆炸。
高能效和长寿命:采用LED技术,LED防爆灯具有高能效、低能耗和长寿命的特点,有助于降低能源成本和维护费用。
耐用性:厂家使用坚固的材料和密封设计,以抵御腐蚀、震动和恶劣天气条件,确保产品的稳定性和可靠性。
多功能性:LED防爆灯通常具备可调光、遥控和智能控制等功能,以满足不同照明需求。
LED防爆灯的广泛应用
LED防爆灯在需要高度安全性和可靠性的各种领域广泛应用,包括:
石油和天然气工业:提供安全的照明,确保工作人员在危险环境中可以清晰地看到操作。
采矿业:在地下矿山和露天矿山中提供可靠的照明,确保工作人员的安全和高效工作。
化工工业:在处理危险化学品和材料的工业环境中提供照明。
海上和船舶工业:在海上平台和船舶上提供耐用的照明设备,应对恶劣海况。
LED防爆灯的未来
随着工业的不断发展和对安全性的不断强调,LED防爆灯将继续演进,以满足新的需求。未来的趋势可能包括:
智能化:更多的智能控制功能,例如远程监控、自动化和能源管理,以提高效率和安全性。
环保:采用更多的环保材料和技术,以减少对环境的影响,同时保持高效性。
更广泛的应用:LED防爆灯将进一步扩展到更多领域,满足各种需求。
总之,LED防爆灯厂家在确保工业安全和提高工作效率方面发挥着关键作用。它们的产品具备***的性能和可靠性,能够在各种恶劣条件下提供安全的照明解决方案。随着技术的不断进步,LED防爆灯将继续为各种高风险环境中的安全照明提供可靠的支持。
标题:LED防爆灯厂家:安全照明的坚实后盾
引言:
在众多工业和商业领域中,确保安全照明是***关重要的。特别是在危险环境中,如石油化工、采矿、制药和军工等行业,安全照明不仅关系到生产效率,更是关系到工人的生命安全。而在这一领域,LED防爆灯厂家扮演着不可或缺的角色。本文将深入探讨LED防爆灯厂家的重要性、关键特点以及它们在安全照明领域的应用。
LED防爆灯厂家的重要性
在确保危险环境下的安全照明方面,LED防爆灯厂家发挥着关键作用,其重要性在于:
高质量产品:LED防爆灯厂家通过研发和创新,提供高品质、高性能的产品,以满足危险环境下的需求。
符合法规标准:厂家确保其产品符合国际安全标准和法规,为客户提供合规的照明解决方案。
技术支持与服务:厂家提供技术支持和售后服务,包括安装指导、维护和维修,以确保LED防爆灯的正常运行。
创新和定制:厂家不断创新,能够根据客户的具体需求,提供定制化的照明解决方案,以满足不同行业和应用的要求。
LED防爆灯的关键特点
LED防爆灯具备一系列关键特点,使其在安全照明领域备受青睐:
防爆设计:这些灯具采用特殊设计,能够在易燃气体或粉尘存在的危险环境中工作,而不会引发火花或爆炸。
高效节能:LED技术的应用使LED防爆灯具有高能效、低能耗的特点,能够降低能源成本。
长寿命:LED光源具有长寿命,减少了维护和更换的频率,提高了可靠性。
耐用性:厂家采用坚固的材料和密封设计,以抵御腐蚀、震动和恶劣天气条件,确保产品的稳定性和可靠性。
多功能性:LED防爆灯通常具有可调光、遥控和智能控制等功能,以满足不同照明需求。
LED防爆灯的广泛应用
LED防爆灯在需要高度安全性和可靠性的各种领域广泛应用,包括:
石油和天然气工业:在石油钻井平台、炼油厂和天然气处理厂等危险环境中提供安全照明。
采矿业:在地下矿山和露天采矿场中提供可靠的照明,确保工作人员的安全。
化工工业:在处理危险化学品和材料的工业环境中提供照明。
制药工业:在制药厂内确保干净和安全的生产环境。
军工领域:在军事设施和舰船上提供可靠的照明设备。
LED防爆灯的未来
随着工业的不断发展和对安全性的不断强调,LED防
标题:LED三防灯:照亮安全之路
引言:
在现代工业和商业领域,安全和可靠的照明设备对于人员的安全和工作效率***关重要。尤其是在危险环境下,如石油钻井平台、化工厂、采矿场所以及户外施工现场,LED三防灯已成为必不可少的照明解决方案。本文将深入探讨LED三防灯的重要性、关键特点以及广泛的应用领域,以阐明它们在确保安全和提高工作效率方面的关键作用。
LED三防灯的重要性
在危险环境中,LED三防灯具有极其重要的地位,因为它们可以:
确保工作安全:在油田、化工厂或采矿场等危险环境中,良好的照明对于工人的安全***关重要。
提供可靠照明:LED三防灯具有高度稳定性和可靠性,能够在恶劣条件下提供均匀的照明,不受振动、湿度或温度变化的影响。
降低能源消耗:采用LED技术,大幅降低能源消耗,有助于降低运营成本。
符合法规标准:在许多工业领域,符合法规标准是必要的,LED三防灯的设计使其符合相关的法规和安全标准。
LED三防灯的关键特点
LED三防灯具有许多关键特点,使其成为极端环境下不可或缺的照明设备:
防爆设计:这些灯具采用特殊设计,能够有效防止火花、高温点或电气故障引发爆炸,确保了在易燃环境中的安全。
耐用性:制造商采用坚固的材料,使这些灯具能够抵御腐蚀、震动和恶劣天气条件,确保长期可靠运行。
节能:采用LED技术,不仅提供均匀的照明,还显著降低了能源消耗,有助于降低运营成本。
多功能性:它们通常具有可调光、遥控和智能控制功能,使其适用于各种照明需求。
LED三防灯的应用领域
LED三防灯广泛应用于需要高度安全性和可靠性的各种领域,包括:
石油和天然气工业:提供安全的照明,确保工作人员在潜在的危险环境中能够清晰地看到操作。
采矿业:在地下矿山和露天矿山中提供可靠的照明,确保工作人员的安全和高效工作。
化工工厂:在处理危险化学品和材料的工业环境中提供照明。
建筑工地:在户外建筑工地提供坚固的照明设备,应对各种天气条件。
LED三防灯的未来
随着工业的不断发展和安全性的不断强调,LED三防灯将不断演进,以满足新的需求。未来的趋势可能包括:
智能化:更多的智能控制功能,例如远程监控、自动化和能源管理,以提高效率和安全性。
环保:采用更多的环保材料和技术,以减少对环境的影响,同时保持高效性。
更广泛的应用:LED三防灯将进一步扩展到更多领域,满足各种需求。
总之,LED三防灯在极端环境下的安全和高效照明解决方案中发挥着关键作用。它们的能力可以降低风险、提高工作效率,并确保工业过程的顺畅运行。随着技术的不断进步,LED三防灯将继续在各种恶劣条件下提供可靠的照明解决方案。
引言:
在现代社会中,电力设备和电子设备的应用已经无处不在。为了确保电流稳定、电路可靠,接线盒作为电路连接的精密守护者,发挥着***关重要的作用。本文将深入探讨接线盒的定义、功能、种类以及在不同领域中的应用,以揭示其在电力领域的不可或缺性。
接线盒的定义和功能
接线盒,也称为配电箱或连接盒,是一种用于连接电缆或电线的设备。它的主要功能是:
电线连接:接线盒允许电线或电缆的连接,确保电流顺畅流动,同时保护连接点不受外部环境的影响。
分布电力:它可以将电力分布到不同的电路或设备,确保电力供应可靠。
保护:接线盒通常具有防水、防尘、防腐蚀等特性,以保护内部电线和连接点。
维护:接线盒的设计通常考虑到了维护和检修的需要,使维护工作更加便捷。
接线盒的种类
接线盒根据其用途和特点可以分为多种类型,其中包括:
分配接线盒:用于将电力分配到不同的电路或设备,通常用于住宅、工业和商业建筑。
终端接线盒:用于连接电缆或电线的末端,通常用于电信和数据通信领域。
防爆接线盒:具有防爆特性,用于危险环境中,如石油化工、矿山等。
太阳能接线盒:专用于太阳能电池板的连接和保护,用于太阳能发电系统。
电子接线盒:用于连接和保护电子设备内部的电路,通常用于计算机、电视等设备。
接线盒在不同领域的应用
接线盒在各个领域中都有广泛的应用,以下是一些示例:
住宅建筑:在家庭电路分布中,接线盒用于将电力连接到不同的房间和电器设备,确保电力供应的安全和可靠。
工业制造:在工业自动化设备中,接线盒用于连接传感器、电机、控制器等,以确保设备的正常运行。 能源领域:在发电厂和电力分配站,接线盒用于连接和分配电力,确保电网的稳定性。
交通信号系统:在交通信号灯和铁路信号系统中,接线盒用于连接信号灯和控制电路,确保交通流畅和安全。
太阳能发电:太阳能接线盒用于连接太阳能电池板,将太阳能转化为电能并分配到电网或电池存储中。
结论
在电力领域,接线盒是电路连接的关键组成部分,它不仅提供了电力分配和连接的功能,还保护了电路免受外部环境的影响。不同类型的接线盒在各种应用领域中都发挥着不可或缺的作用,确保了电力供应的安全、稳定和可靠。随着技术的不断进步,接线盒的设计和性能将继续提升,以满足不断变化的电力需求。因此,接线盒可以被视为电力系统中的精密守护者,为现代社会的可持续发展提供了坚实的支持。
引言:
在现代工业领域,管道和导线的保护和传输***关重要。尼龙波纹管作为一种多功能的管道保护材料,已经成为各种应用中的不可或缺的组成部分。本文将深入探讨尼龙波纹管的定义、特点、种类以及在不同领域中的广泛应用,以展示它在工业界的重要性和多功能性。
尼龙波纹管的定义和特点
尼龙波纹管是一种由尼龙材料制成的柔性管道保护装置。它具有以下关键特点:
柔性和耐用:尼龙波纹管具有极高的柔韧性,可以适应多种弯曲和形状,同时具有出色的耐用性,能够长期承受外部压力和环境条件的影响。
耐化学腐蚀:尼龙波纹管对许多化学物质和腐蚀性液体具有抵抗能力,因此广泛用于化工和制药领域。
抗高温和低温:它可以在广泛的温度范围内工作,包括高温和低温环境。
电磁屏蔽性:尼龙波纹管可以提供电磁屏蔽,保护电线和电缆免受外部电磁干扰。
防水和防尘:它能够有效地防止水和尘土进入管道或电线,保持内部设备的清洁和安全。
尼龙波纹管的种类
尼龙波纹管有多种类型,适用于不同的应用场景:
尼龙波纹电线管:用于电线和电缆的保护,通常在建筑和电气工程中使用。
尼龙波纹液体输送管:用于输送各种液体,包括油、水、化学品等,广泛应用于工业流体输送。
尼龙波纹护套管:作为电线和电缆的外部护套,提供额外的保护和耐用性。
尼龙波纹导管:用于光纤和通信线路的保护,确保信号传输的稳定性。
尼龙波纹管的应用领域
尼龙波纹管在各个工业领域中都有广泛的应用,以下是一些示例:
电气工程:在电线和电缆的保护中,防止机械损伤和化学腐蚀。
制药和化工:用于化学品输送和处理,确保流体的安全和稳定。
机械制造:在机器和设备中,用于保护液压管路和传感器线路。
交通运输:用于汽车、火车和飞机的电子设备和导线的保护。
通信领域:用于光纤和通信线路的保护,确保信号的质量和可靠性。
结论
尼龙波纹管作为一种多功能的管道保护装置,在工业界发挥着不可或缺的作用。它的柔韧性、耐用性和化学腐蚀抵抗能力使其适用于各种恶劣环境和应用中。随着技术的不断进步,尼龙波纹管的设计和性能将继续提升,以满足不断变化的工业需求。因此,尼龙波纹管可以被视为工业领域的多功能利器,为各种应用提供了可靠的管道保护和电线导管解决方案。
引言:
在现代社会中,电力设备和电子设备的应用已经无处不在。然而,许多应用场合常伴随着潮湿、多雨的环境,这就需要一种特殊的电路保护装置,那就是防水接线盒。本文将深入探讨防水接线盒的定义、功能、种类以及在各个领域中的广泛应用,以凸显其在电路保护中的重要性。
防水接线盒的定义和功能
防水接线盒,又称为防水连接盒,是一种专门设计用于防水防尘的电气连接设备。它具有以下关键功能:
电线连接:防水接线盒用于连接电线或电缆,确保电流正常传输,同时防止水分、湿气和灰尘进入接线部分。
防水防尘:防水接线盒采用密封设计,有效地防止水分和尘埃侵入,从而保护内部电路免受损坏。
耐用性:它通常由耐用的材料制成,具有抗冲击和耐候性,可在恶劣天气条件下长时间使用。
安全性:防水接线盒确保电路连接安全可靠,降低电路故障和火灾的风险。
防水接线盒的种类
防水接线盒有多种类型,根据用途和特点的不同可以分为以下几类:
塑料防水接线盒:通常采用聚碳酸酯(PC)或聚丙烯(PP)等塑料材料制成,适用于轻型应用。
金属防水接线盒:由金属材料制成,具有更高的耐用性和防护性能,适用于重型工业环境。
防爆防水接线盒:具有防爆性能,适用于危险气体或粉尘环境,如化工厂和矿山。
电子防水接线盒:用于电子设备内部电路的防护,通常采用特殊密封技术。
防水接线盒的应用领域
防水接线盒在各个领域中都有广泛的应用,以下是一些示例:
户外照明:在户外照明设备中,如路灯、露天广告牌,用于保护电路免受雨水和湿气的侵害。
水下设备:用于水下摄像机、潜水设备等,确保设备在水中工作时电路安全。
农业领域:用于农业自动化设备,保护电路免受农田中的水分和灰尘影响。
电信设备:用于电信基站和通信设备的电路保护,确保通信信号的稳定传输。
工业制造:用于工厂设备和机械的电路连接,确保设备在恶劣工业环境中可靠运行。
结论
防水接线盒作为一种电路保护装置,在各个领域中发挥着不可或缺的作用。它的防水防尘性能可以确保电路在潮湿、多雨的环境中安全运行,降低电路故障和维修成本。随着技术的不断进步,防水接线盒的设计和性能将不断提升,以满足不断变化的工业需求。因此,防水接线盒可以被视为电路保护的坚实壁垒,为各种应用提供了可靠的电路连接和保护解决方案。
标题:尼龙波纹管:工业领域的多功能利器
引言:
在现代工业领域,管道和导线的保护和传输***关重要。尼龙波纹管作为一种多功能的管道保护材料,已经成为各种应用中的不可或缺的组成部分。本文将深入探讨尼龙波纹管的定义、特点、种类以及在不同领域中的广泛应用,以展示它在工业界的重要性和多功能性。
尼龙波纹管的定义和特点
尼龙波纹管是一种由尼龙材料制成的柔性管道保护装置。它具有以下关键特点:
柔性和耐用:尼龙波纹管具有极高的柔韧性,可以适应多种弯曲和形状,同时具有出色的耐用性,能够长期承受外部压力和环境条件的影响。
耐化学腐蚀:尼龙波纹管对许多化学物质和腐蚀性液体具有抵抗能力,因此广泛用于化工和制药领域。
抗高温和低温:它可以在广泛的温度范围内工作,包括高温和低温环境。
电磁屏蔽性:尼龙波纹管可以提供电磁屏蔽,保护电线和电缆免受外部电磁干扰。
防水和防尘:它能够有效地防止水和尘土进入管道或电线,保持内部设备的清洁和安全。
尼龙波纹管的种类
尼龙波纹管有多种类型,适用于不同的应用场景:
尼龙波纹电线管:用于电线和电缆的保护,通常在建筑和电气工程中使用。
尼龙波纹液体输送管:用于输送各种液体,包括油、水、化学品等,广泛应用于工业流体输送。
尼龙波纹护套管:作为电线和电缆的外部护套,提供额外的保护和耐用性。
尼龙波纹导管:用于光纤和通信线路的保护,确保信号传输的稳定性。
尼龙波纹管的应用领域
尼龙波纹管在各个工业领域中都有广泛的应用,以下是一些示例:
电气工程:在电线和电缆的保护中,防止机械损伤和化学腐蚀。
制药和化工:用于化学品输送和处理,确保流体的安全和稳定。
机械制造:在机器和设备中,用于保护液压管路和传感器线路。
交通运输:用于汽车、火车和飞机的电子设备和导线的保护。
通信领域:用于光纤和通信线路的保护,确保信号的质量和可靠性。
结论
尼龙波纹管作为一种多功能的管道保护装置,在工业界发挥着不可或缺的作用。它的柔韧性、耐用性和化学腐蚀抵抗能力使其适用于各种恶劣环境和应用中。随着技术的不断进步,尼龙波纹管的设计和性能将不断提升,以满足不断变化的工业需求。因此,尼龙波纹管可以被视为工业领域的多功能利器,为各种应用提供了可靠的管道保护和电线导管解决方案。
引言:
在现代工业和电子领域中,对于电缆和电线连接的可靠性和安全性要求越来越高。同时,环保意识也成为了全球范围内的重要议题。REACH防水接头,作为一种环保并提供出色性能的电缆连接解决方案,正逐渐赢得越来越多行业的青睐。本文将深入探讨REACH防水接头的定义、特点、应用领域以及为何成为工业界的理想选择。 REACH防水接头的定义与特点
REACH是指欧洲化学品注册、评估、许可和限制(Registration, Evaluation, Authorization, and Restriction of Chemicals)的法规,它旨在保护人类健康和环境,同时促进欧洲化学品产业的创新。REACH防水接头是符合REACH法规的电缆连接器,具有以下关键特点:
环保材料:REACH防水接头采用符合REACH法规的环保材料制成,不含有害化学物质,对环境友好。
高度防水:它具有***的防水性能,能够在潮湿和多雨的环境中保护电缆连接不受损害。
抗化学腐蚀:REACH防水接头对多种化学物质具有良好的抵抗性,适用于各种恶劣化学环境。
耐用性:它经过精密设计和测试,具有出色的耐用性,可长期承受机械应力和外部环境的影响。
可靠性:REACH防水接头确保电缆连接的可靠性,降低了电路故障的风险。
REACH防水接头的应用领域
REACH防水接头在各个领域中都有广泛的应用,以下是一些示例:
电气工程:用于户外电气设备和电缆连接,确保电路在恶劣天气条件下的稳定运行。
工业自动化:在工厂自动化系统中,用于连接传感器、电机和控制器,提高生产效率。
医疗设备:用于医疗设备和仪器的电缆连接,确保医疗设备的安全性和可靠性。
通信领域:在通信设备和基站中,用于保护电缆连接,确保通信信号的稳定传输。
能源领域:用于风力发电和太阳能发电设备的电缆连接,提高可再生能源系统的可靠性。
结论
REACH防水接头作为一种环保且提供***性能的电缆连接解决方案,正在全球范围内受到越来越多行业的青睐。它不仅确保了电缆连接的可靠性和安全性,还有助于维护环境和保护人类健康。随着环保意识的不断增强,REACH防水接头将继续在各个工业领域中发挥其优势,成为工程师和设计师的理想选择,以满足高性能和环保的双重需求。因此,REACH防水接头被认为是现代工业界的一项重要技术创新,将为各行各业的发展提供可持续性的支持。
引言:
在电力系统的建设和运行中,防水配电箱扮演着***关重要的角色。它不仅可以保护电力设备免受恶劣天气和环境条件的侵害,还可以确保电路连接的可靠性。本文将深入探讨防水配电箱的定义、特点、种类以及在各个领域中的广泛应用,以展示它在电力系统中的不可或缺性和重要性。
防水配电箱的定义和特点
防水配电箱是一种专门设计用于电力设备的外部保护装置,具有以下关键特点:
***的防水性能:防水配电箱采用密封设计,有效地防止水分、湿气和雨水进入内部,确保电力设备在潮湿或多雨的环境中安全运行。
耐候性:它通常由耐用的材料制成,能够承受极端气候条件,如高温、低温、紫外线和腐蚀。
防尘性能:防水配电箱不仅能够抵御水分,还可以有效地阻止灰尘和颗粒进入设备内部,降低维护频率。
安全性:它确保电路连接安全可靠,降低了电路故障和火灾的风险。
可定制性:防水配电箱可根据不同的应用需求进行定制,包括不同尺寸、形状和安装选项。
防水配电箱的种类
防水配电箱有多种类型,根据用途和特点的不同可以分为以下几类:
塑料防水配电箱:通常采用聚碳酸酯(PC)或聚丙烯(PP)等塑料材料制成,适用于轻型应用。
金属防水配电箱:由金属材料制成,具有更高的耐用性和防护性能,适用于重型工业环境。
防爆防水配电箱:具有防爆性能,适用于危险气体或粉尘环境,如化工厂和矿山。
户外防水配电箱:专门设计用于户外应用,如路灯、广告牌、电缆接头等。
防水配电箱的应用领域
防水配电箱在各个领域中都有广泛的应用,以下是一些示例:
建筑工程:用于建筑工地的电力配电,确保建筑设备的正常运行。
工业制造:用于工厂设备和机械的电力分配和保护,提高生产效率。
交通运输:在铁路、地铁、机场等交通基础设施中,用于电力系统的分配和控制。
能源领域:用于电力发电站和变电站的设备保护,确保电力系统的稳定运行。
户外照明:在户外照明设备中,如路灯、广告牌,用于保护电路免受雨水和湿气的侵害。
结论
防水配电箱作为电力系统中的关键组件,为电力设备的安全运行提供了坚实的防护。它的防水性能、耐候性和可定制性使其适用于各种环境和应用。随着电力系统的不断发展和现代化,防水配电箱的设计和性能将继续提升,以满足不断变化的工业需求。因此,防水配电箱可以被视为电力系统的可靠守护者,为各个领域的电力设备提供了安全和可靠的电路分配和保护解决方案。
引言:
在现代电气工程中,电缆和线路的连接必须具备高度的可靠性和安全性。金属防水接头作为一种重要的电气连接组件,不仅可以抵御外部环境的侵害,还能确保电路的稳定性。本文将深入探讨金属防水接头的定义、特点、种类以及在各个领域中的广泛应用,以展示它在电气工程中的不可或缺性和重要性。 金属防水接头的定义与特点
金属防水接头是一种电缆连接器,具有以下关键特点:
***的防水性能:金属防水接头采用密封设计,可以有效地防止水分、湿气和雨水进入内部,确保电缆连接不受损害。
耐候性:它通常由高质量的金属制成,能够抵抗极端气候条件,如高温、低温和紫外线辐射。
抗腐蚀:金属防水接头具有良好的抗腐蚀性能,适用于恶劣环境,如化工工厂和海洋应用。
电磁屏蔽性:它可以提供电磁屏蔽,保护电线和电缆免受外部电磁干扰。
可靠性:金属防水接头确保电路连接的可靠性,降低了电路故障和火灾的风险。
金属防水接头的种类
金属防水接头有多种类型,根据用途和特点的不同可以分为以下几类:
螺纹式金属防水接头:采用螺纹设计,具有简单的安装和卸载过程,适用于户外和工业环境。
插拔式金属防水接头:具有插拔式连接方式,适用于需要频繁连接和断开的场合,如测试仪器和测量设备。
定位销式金属防水接头:使用定位销来确保连接的准确性和稳定性,适用于需要高度***连接的应用。
旋转式金属防水接头:具有旋转连接的功能,可用于需要连接角度可调的场合,如摄像头和照明设备。
金属防水接头的应用领域
金属防水接头在各个领域中都有广泛的应用,以下是一些示例:
电气工程:用于户外电气设备和电缆连接,确保电路在恶劣天气条件下的稳定运行。
工业制造:用于工厂设备和机械的电力分配和保护,提高生产效率。
通信领域:在通信设备和基站中,用于保护电缆连接,确保通信信号的稳定传输。
能源领域:用于电力发电站和变电站的设备保护,确保电力系统的稳定运行。
交通运输:在铁路、地铁、机场等交通基础设施中,用于电力系统的分配和控制。
结论
金属防水接头作为电气工程中的关键组件,为电缆连接提供了坚实的保护和稳定性。它的防水性能、耐候性和可定制性使其适用于各种环境和应用。随着电气工程的不断发展和现代化,金属防水接头的设计和性能将继续提升,以满足不断变化的工业需求。因此,金属防水接头被认为是电气连接的坚实屏障,为各个领域的电力设备提供了安全和可靠的电路分配和保护解决方案。
标题:REACH防水接头:环保与可靠的电气连接解决方案
引言:
在电气工程和电子设备制造领域,可靠的电气连接***关重要。同时,环保问题也引起了广泛关注。REACH防水接头,作为一种环保且提供***性能的电缆连接解决方案,正在逐渐成为众多行业的***。本文将深入探讨REACH防水接头的定义、特点、应用领域以及为何成为工业界的理想选择。
REACH防水接头的定义与特点
REACH是指欧洲化学品注册、评估、许可和限制(Registration, Evaluation, Authorization, and Restriction of Chemicals)的法规,旨在保护人类健康和环境。REACH防水接头是符合REACH法规的电缆连接器,具有以下关键特点:
环保材料:REACH防水接头采用符合REACH法规的环保材料制成,不含有害化学物质,对环境友好。
***的防水性能:它具有***的防水性能,能够在潮湿和多雨的环境中保护电缆连接不受损害。
抗化学腐蚀:REACH防水接头对多种化学物质具有良好的抵抗性,适用于各种恶劣化学环境。
耐用性:它经过精密设计和测试,具有出色的耐用性,可长期承受机械应力和外部环境的影响。
可靠性:REACH防水接头确保电缆连接的可靠性,降低了电路故障的风险。
REACH防水接头的应用领域
REACH防水接头在各个领域中都有广泛的应用,以下是一些示例:
电气工程:用于户外电气设备和电缆连接,确保电路在恶劣天气条件下的稳定运行。
工业自动化:在工厂自动化系统中,用于连接传感器、电机和控制器,提高生产效率。
医疗设备:用于医疗设备和仪器的电缆连接,确保医疗设备的安全性和可靠性。
通信领域:在通信设备和基站中,用于保护电缆连接,确保通信信号的稳定传输。
能源领域:用于风力发电和太阳能发电设备的电缆连接,提高可再生能源系统的可靠性。
结论
REACH防水接头作为一种环保且提供***性能的电缆连接解决方案,正在全球范围内受到越来越多行业的青睐。它不仅确保了电缆连接的可靠性和安全性,还有助于维护环境和保护人类健康。随着环保意识的不断增强,REACH防水接头将继续在各个工业领域中发挥其优势,成为工程师和设计师的理想选择,以满足高性能和环保的双重需求。因此,REACH防水接头被认为是现代工业界的一项重要技术创新,将为各行各业的发展提供可持续性的支持。
标题:防水接头:电气连接的安全卫士
引言:
在电气工程领域,稳定可靠的电气连接对设备和系统的正常运行***关重要。而在户外、恶劣天气或潮湿环境下,电缆和线路的连接往往容易受到损害。因此,防水接头应运而生,作为一种关键的电气连接组件,它不仅可以保护电路免受外部环境的侵害,还能确保电气设备的可靠性。本文将深入探讨防水接头的定义、特点、种类以及在各个领域中的广泛应用,以展示它在电气工程中的不可或缺性和重要性。
防水接头的定义与特点
防水接头是一种用于电缆和线路连接的装置,它具有以下关键特点:
***的防水性能:防水接头采用密封设计,有效地防止水分、湿气和雨水进入内部,确保电缆连接不受损害。
耐候性:它通常由高质量的材料制成,能够抵抗极端气候条件,如高温、低温和紫外线辐射。
抗腐蚀:防水接头对多种化学物质具有良好的抵抗性,适用于各种恶劣化学环境。
耐用性:防水接头经过精密设计和测试,具有出色的耐用性,可长期承受机械应力和外部环境的影响。
可靠性:防水接头确保电缆连接的可靠性,降低了电路故障和火灾的风险。
防水接头的种类
防水接头有多种类型,根据用途和特点的不同可以分为以下几类:
螺纹式防水接头:采用螺纹设计,具有简单的安装和卸载过程,适用于户外和工业环境。
插拔式防水接头:具有插拔式连接方式,适用于需要频繁连接和断开的场合,如测试仪器和测量设备。
定位销式防水接头:使用定位销来确保连接的准确性和稳定性,适用于需要高度***连接的应用。
旋转式防水接头:具有旋转连接的功能,可用于需要连接角度可调的场合,如摄像头和照明设备。
防水接头的应用领域
防水接头在各个领域中都有广泛的应用,以下是一些示例:
电气工程:用于户外电气设备和电缆连接,确保电路在恶劣天气条件下的稳定运行。
工业自动化:在工厂自动化系统中,用于连接传感器、电机和控制器,提高生产效率。
医疗设备:用于医疗设备和仪器的电缆连接,确保医疗设备的安全性和可靠性。
通信领域:在通信设备和基站中,用于保护电缆连接,确保通信信号的稳定传输。
能源领域:用于风力发电和太阳能发电设备的电缆连接,提高可再生能源系统的可靠性。
结论
防水接头作为一种关键的电气连接组件,为电缆和线路连接提供了坚实的保护和稳定性。它的防水性能、耐候性和可定制性使其适用于各种环境和应用。在电气工程中,防水接头被视为电路的安全卫士,为各个领域的电气设备提供了安全和可靠的电路连接解决方案。随着技术的不断发展,防水接头的设计和性能将继续提升,以满足不断变化的工业需求,确保电气系统的稳定运行。因此,防水接头在现代电气工程中扮演着不可或缺的角色。
引言:
电气连接在现代社会中扮演着***关重要的角色,无论是在工业生产中还是日常生活中。然而,在户外或暴露在紫外线下的电缆连接,常常受到紫外线辐射的侵害,导致电缆老化、劣化和性能下降。为了延长电气连接的寿命,抗紫外线电缆接头应运而生。本文将深入探讨抗紫外线电缆接头的定义、特点、应用领域以及为何成为电气工程的重要组成部分。 抗紫外线电缆接头的定义与特点
抗紫外线电缆接头是一种特殊设计的电缆连接器,具有以下关键特点:
紫外线抵抗:它采用特殊材料和涂层,具有***的紫外线抵抗性能,可抵御紫外线辐射引起的老化和劣化。
耐候性:抗紫外线电缆接头通常由高质量的材料制成,能够抵抗极端气候条件,如高温、低温和潮湿。
防水性能:它同时具备防水设计,可有效保护电缆连接免受水分和潮湿环境的侵害。
耐化学腐蚀:抗紫外线电缆接头对多种化学物质具有良好的抵抗性,适用于各种化学工业环境。
可靠性:抗紫外线电缆接头确保电缆连接的可靠性,降低了电路故障和火灾的风险。
抗紫外线电缆接头的应用领域
抗紫外线电缆接头在各个领域中都有广泛的应用,以下是一些示例:
户外照明:用于户外路灯、景观照明和太阳能照明系统,延长照明设备的使用寿命。
电力输配电:在电力输配电设备中,用于连接电缆和电线,提高电力系统的可靠性。
通信领域:在通信设备和基站中,用于保护电缆连接,确保通信信号的稳定传输。
太阳能能源:用于太阳能电池板的电缆连接,确保能源系统的稳定运行。
交通信号系统:用于交通信号灯和交通管理系统,提高交通系统的可靠性。
结论
抗紫外线电缆接头作为电气工程领域的重要组成部分,为电缆连接提供了关键的保护和性能提升。它的紫外线抵抗性能、耐候性和可定制性使其适用于各种环境和应用。在户外或受紫外线辐射的场合,抗紫外线电缆接头被视为电气连接的关键组件,可延长电气设备的使用寿命,减少维护成本,并提高电气系统的可靠性。因此,抗紫外线电缆接头不仅延长了电缆连接的寿命,还为电气工程提供了一种可靠、高效和环保的解决方案,推动了现代社会的发展。
引言:
在电气工程领域,电气连接是确保电路和设备正常运行的关键环节。而端子盒,作为一种电气连接的重要组件,扮演着重要的角色。它不仅用于连接电缆和线路,还起到保护、整理和管理电气连接的作用。本文将深入探讨端子盒的定义、特点、种类以及在各个领域中的广泛应用,以展示它在电气工程中的不可或缺性和重要性。
端子盒的定义与特点
端子盒是一种用于电缆和线路连接的装置,具有以下关键特点:
连接与分配:端子盒允许多个电缆或线路连接到同一点,同时还可以将电信号或电力分配到不同的部分。
防护功能:它采用密封设计,能够防止外部环境、灰尘、湿气和水分侵入,有效保护电气连接不受损害。
耐腐蚀性:端子盒通常由耐腐蚀材料制成,能够抵抗化学物质和恶劣环境条件的侵蚀。
耐热性:一些端子盒还具备耐高温特性,适用于高温环境下的电气连接。
可靠性:端子盒确保电缆连接的可靠性,降低了电路故障的风险。
端子盒的种类
端子盒有多种类型,根据用途和特点的不同可以分为以下几类:
螺纹式端子盒:采用螺纹设计,具有简单的安装和卸载过程,适用于各种电气工程。
插拔式端子盒:具有插拔式连接方式,适用于需要频繁连接和断开的场合,如测试仪器和测量设备。
固定式端子盒:用于需要稳定连接的场合,通常采用螺栓或固定夹持方式,确保连接牢固。
防爆端子盒:具有防爆设计,适用于爆炸性气体环境中的电气连接,确保安全性。
端子盒的应用领域
端子盒在各个领域中都有广泛的应用,以下是一些示例:
工业自动化:用于连接传感器、电机、控制器和仪表,实现自动化生产和监控。
电力输配电:在电力系统中,用于连接电缆和电线,确保电力系统的正常运行。
交通信号系统:用于交通信号灯、铁路信号设备和道路照明系统,提高交通系统的可靠性。
建筑业:在建筑电气工程中,用于连接照明、插座和电力设备。
风电和太阳能能源:用于风力发电和太阳能电池板的电气连接,确保能源系统的稳定运行。
结论
端子盒作为电气工程领域的重要组件,为电缆连接提供了关键的保护和管理功能。它的多功能性、可靠性和耐用性使其在各个领域中都有广泛的应用。在电气工程中,端子盒被视为电气连接的精密仪器,不仅延长了电气设备的使用寿命,还提高了电路的可靠性和安全性。因此,端子盒在现代电气工程中扮演着不可或缺的角色,推动着各个行业的发展。
引言:
在电气工程领域,电气连接的稳定性和可靠性对设备和系统的正常运行***关重要。然而,电气连接在恶劣天气或潮湿环境下常常受到水分侵害,从而导致电路故障和设备损坏。为了应对这一挑战,UL防水接头应运而生,它不仅具备***的防水性能,还符合UL(Underwriters Laboratories)标准,为电气连接提供了额外的安全保障。本文将深入探讨UL防水接头的定义、特点、应用领域以及为何成为电气工程的关键组成部分。
UL防水接头的定义与特点
UL防水接头是一种特殊设计的电缆连接器,具有以下关键特点:
UL认证:UL防水接头符合Underwriters Laboratories(UL)的标准和要求,经过严格的测试和认证,确保其质量和性能达到国际标准。
***的防水性能:它采用高质量的材料和密封设计,能够有效防止水分、湿气和雨水侵入内部,确保电缆连接不受损害。
耐候性:UL防水接头通常由耐候材料制成,能够抵抗极端气候条件,如高温、低温和紫外线辐射。
耐化学腐蚀:它对多种化学物质具有出色的抵抗性,适用于各种恶劣化学环境。
可靠性:UL防水接头确保电缆连接的可靠性,降低了电路故障和火灾的风险。
UL防水接头的应用领域
UL防水接头在各个领域中都有广泛的应用,以下是一些示例:
户外照明:用于户外路灯、景观照明和太阳能照明系统,延长照明设备的使用寿命。
电力输配电:在电力系统中,用于连接电缆和电线,确保电力系统的正常运行。
工业自动化:用于连接传感器、电机、控制器和仪表,提高工业生产的效率和可靠性。
通信领域:在通信设备和基站中,用于保护电缆连接,确保通信信号的稳定传输。
建筑业:在建筑电气工程中,用于连接照明、插座和电力设备,确保建筑设备的可靠性和安全性。
结论
UL防水接头作为电气工程领域的重要组件,为电缆连接提供了关键的保护和性能提升。它的UL认证、***的防水性能、耐候性和耐化学腐蚀性使其在各个领域中都有广泛的应用。在电气工程中,UL防水接头被视为电气连接的安全保障,不仅延长了电缆连接的寿命,还提高了电路的可靠性和安全性。因此,UL防水接头在现代电气工程中扮演着不可或缺的角色,为各个行业的发展提供了可靠、高效和安全的电气连接解决方案。
标题:防水接线盒:电气工程的护航者
引言:
在电气工程中,防水接线盒是一种***关重要的电气连接器,它具有防水、防尘和保护电气连接的功能。无论是户外工程、工业自动化、建筑电气还是其他领域,防水接线盒都扮演着关键的角色。本文将深入探讨防水接线盒的定义、特点、种类以及在各个领域中的广泛应用,以展示它在电气工程中的不可或缺性和重要性。
防水接线盒的定义与特点
防水接线盒是一种专门设计的电气连接器,具有以下关键特点:
防水设计:它采用密封设计,能够有效防止水分、湿气和雨水侵入内部,保护电气连接不受损害。
防尘性能:防水接线盒通常具有防尘特性,阻挡粉尘和杂质进入,保持连接的清洁状态。
耐候性:防水接线盒通常由耐候材料制成,能够抵抗极端气候条件,如高温、低温和紫外线辐射。
耐化学腐蚀:它对多种化学物质具有出色的抵抗性,适用于各种恶劣化学环境。
可靠性:防水接线盒确保电缆连接的可靠性,降低了电路故障和火灾的风险。
防水接线盒的种类
防水接线盒有多种类型,根据用途和特点的不同可以分为以下几类:
螺纹式防水接线盒:采用螺纹设计,具有简单的安装和卸载过程,适用于各种电气工程。
插拔式防水接线盒:具有插拔式连接方式,适用于需要频繁连接和断开的场合,如测试仪器和测量设备。
固定式防水接线盒:用于需要稳定连接的场合,通常采用螺栓或固定夹持方式,确保连接牢固。
防爆防水接线盒:具有防爆设计,适用于爆炸性气体环境中的电气连接,确保安全性。
防水接线盒的应用领域
防水接线盒在各个领域中都有广泛的应用,以下是一些示例:
户外照明:用于户外路灯、景观照明和太阳能照明系统,延长照明设备的使用寿命。
电力输配电:在电力系统中,用于连接电缆和电线,确保电力系统的正常运行。
工业自动化:用于连接传感器、电机、控制器和仪表,提高工业生产的效率和可靠性。
建筑业:在建筑电气工程中,用于连接照明、插座和电力设备,确保建筑设备的可靠性和安全性。
风电和太阳能能源:用于风力发电和太阳能电池板的电气连接,确保能源系统的稳定运行。
结论
防水接线盒作为电气工程领域的重要组件,为电缆连接提供了关键的保护和性能提升。它的防水设计、防尘性能、耐候性和耐化学腐蚀性使其在各个领域中都有广泛的应用。在电气工程中,防水接线盒被视为电气连接的护航者,不仅延长了电缆连接的寿命,还提高了电路的可靠性和安全性。因此,防水接线盒在现代电气工程中扮演着不可或缺的角色,为各个行业的发展提供了可靠、高效和安全的电气连接解决方案。
引言:
电气连接在现代社会中扮演着不可或缺的角色,而电缆接头是连接电线和电缆的关键组件之一。在某些特殊应用中,如机器人技术、航空航天和医疗设备,电缆经常需要承受扭曲和旋转的应力。为了确保电气连接的可靠性,耐扭电缆接头应运而生。本文将深入探讨耐扭电缆接头的定义、特点、种类以及在各个领域中的广泛应用,以展示它在电气工程中的不可或缺性和重要性。 耐扭电缆接头的定义与特点
耐扭电缆接头是一种专门设计的电缆连接器,具有以下关键特点:
扭曲耐力:耐扭电缆接头能够承受电缆的扭曲和旋转运动,而不损坏电气连接。
耐磨损:它通常具有耐磨损的外部涂层或套管,防止电缆在长期使用中受到磨损和破损。
防水防尘:耐扭电缆接头常采用密封设计,能够有效防止水分、湿气和灰尘进入内部,提高电气连接的耐用性。
高温耐受性:一些耐扭电缆接头能够在高温环境下工作,适用于极端条件下的应用。
可靠性:耐扭电缆接头确保电缆连接的可靠性,降低了电路故障和设备损坏的风险。
耐扭电缆接头的种类
耐扭电缆接头有多种类型,根据用途和特点的不同可以分为以下几类:
旋转式耐扭电缆接头:具有旋转连接部件,允许电缆在连接时旋转,适用于需要频繁扭曲的场合,如机器人技术。
扭曲式耐扭电缆接头:具有弯曲或弹性的连接部件,能够在扭曲时保持连接的稳定性,适用于医疗设备等应用。
高温耐受型耐扭电缆接头:具备高温工作能力,适用于高温环境下的航空航天和工业应用。
耐扭电缆接头的应用领域
耐扭电缆接头在各个领域中都有广泛的应用,以下是一些示例:
机器人技术:用于机器人的电缆连接,允许机器人执行复杂的运动任务。
医疗设备:在医疗设备中,用于连接旋转或移动的部件,如扫描仪和手术机器人。
航空航天:用于飞行器和卫星,确保电缆连接在极端条件下的可靠性。
工业自动化:用于工业机械和设备,提高生产线的灵活性和效率。
结论
耐扭电缆接头作为电气工程领域的关键组成部分,为电缆连接提供了关键的保护和性能提升。它的扭曲耐力、耐磨损性、防水防尘特性和高温耐受性使其在各个领域中都有广泛的应用。在电气工程中,耐扭电缆接头被视为电气连接的可靠守护者,不仅确保了电缆连接的稳定性,还提高了电路的可靠性和安全性。因此,耐扭电缆接头在现代电气工程中扮演着不可或缺的角色,为各个行业的发展提供了可靠、高效和安全的电气连接解决方案。
标题:耐扭电缆接头:电气连接的稳定之道
引言:
电气连接在现代社会中无处不在,而电缆接头作为连接电线和电缆的核心组件,其性能直接关系到电路的稳定性和可靠性。在某些特殊应用中,如机器人技术、医疗设备和工业自动化,电缆需要经受不断的扭曲和旋转应力,因此,耐扭电缆接头应运而生。本文将深入探讨耐扭电缆接头的定义、特点、种类以及在各个领域中的广泛应用,以展示它在电气工程中的重要性和不可或缺性。
耐扭电缆接头的定义与特点
耐扭电缆接头是一种特殊设计的电缆连接器,具有以下关键特点:
扭曲耐力:耐扭电缆接头能够承受电缆的扭曲和旋转运动,而不会影响电气连接的性能。
耐磨损:它通常具备耐磨损的外部涂层或材料,能够防止电缆在长期使用中受到磨损和破损。
防水防尘:耐扭电缆接头采用密封设计,能够有效防止水分、湿气和灰尘进入内部,提高电气连接的耐用性。
高温耐受性:一些耐扭电缆接头能够在高温环境下工作,适用于高温条件下的应用。
可靠性:耐扭电缆接头确保电缆连接的可靠性,降低了电路故障和设备损坏的风险。
耐扭电缆接头的种类
耐扭电缆接头有多种类型,根据用途和特点的不同可以分为以下几类:
旋转式耐扭电缆接头:具有旋转连接部件,允许电缆在连接时旋转,适用于需要频繁扭曲的场合,如机器人技术。
扭曲式耐扭电缆接头:具有弯曲或弹性的连接部件,能够在扭曲时保持连接的稳定性,适用于医疗设备等应用。
高温耐受型耐扭电缆接头:具备高温工作能力,适用于高温环境下的航空航天和工业应用。
耐扭电缆接头的应用领域
耐扭电缆接头在各个领域中都有广泛的应用,以下是一些示例:
机器人技术:用于机器人的电缆连接,允许机器人执行复杂的运动任务。
医疗设备:在医疗设备中,用于连接旋转或移动的部件,如扫描仪和手术机器人。
航空航天:用于飞行器和卫星,确保电缆连接在极端条件下的可靠性。
工业自动化:用于工业机械和设备,提高生产线的灵活性和效率。
结论
耐扭电缆接头作为电气工程领域的重要组成部分,为电缆连接提供了关键的保护和性能提升。它的扭曲耐力、耐磨损性、防水防尘特性和高温耐受性使其在各个领域中都有广泛的应用。在电气工程中,耐扭电缆接头被视为电气连接的稳定之道,不仅确保了电缆连接的稳定性,还提高了电路的可靠性和安全性。因此,耐扭电缆接头在现代电气工程中扮演着不可或缺的角色,为各个行业的发展提供了可靠、高效和安全的电气连接解决方案。
引言:
随着城市化的不断发展和现代化建筑的兴起,应急照明系统在建筑物中的重要性日益凸显。a型应急照明集中电源是一种关键的电力设备,它确保了在紧急情况下建筑物内的照明系统能够继续提供照明,为人们提供逃生和求助的必要光线。本文将深入探讨A型应急照明集中电源的定义、特点、工作原理以及在安全领域中的广泛应用,以展示它在现代建筑中的重要性和不可或缺性。 A型应急照明集中电源的定义与特点
A型应急照明集中电源是一种专门设计的电力设备,具有以下关键特点:
集中供电:它为建筑物内的应急照明系统提供电力,确保在电力中断或火警情况下仍能正常运行。
可靠性:A型应急照明集中电源具备高度可靠性,经过严格的测试和认证,以应对紧急情况。
持续供电:它能够提供数小时的电力供应,足够支持人员疏散、火警控制和应急情况下的照明需求。
自动切换:在电力中断时,A型应急照明集中电源能够自动切换到备用电源,确保照明系统不间断运行。
A型应急照明集中电源的工作原理
A型应急照明集中电源的工作原理基于以下关键步骤:
监测电力状态:它持续监测建筑物的主电源状态。当主电源正常时,A型应急照明集中电源不进行干预。
电力中断检测:如果主电源发生故障或中断,A型应急照明集中电源会迅速检测到,并立即启动备用电源。
备用电源启动:A型应急照明集中电源会启动备用电池或发电机,以供应紧急照明系统所需的电力。
照明系统供电:一旦备用电源启动,它将为建筑物内的应急照明系统提供稳定的电力,确保建筑物内的照明不中断。
A型应急照明集中电源的应用领域
A型应急照明集中电源在各个领域中都有广泛的应用,以下是一些示例:
商业建筑:用于商场、办公大楼、酒店等商业场所,确保顾客和员工在火警或电力中断时能够安全疏散。
医疗设施:用于医院、诊所和医疗实验室,保证医疗设施在紧急情况下的照明和设备供电。
工业厂房:用于工厂、生产车间和仓库,确保工人在紧急情况下的安全撤离和设备控制。
交通枢纽:用于地铁站、机场和火车站,保障旅客在火警或电力中断时的安全。
结论
A型应急照明集中电源作为建筑物内应急照明系统的关键组成部分,为紧急情况下的照明需求提供了可靠的电力保障。它的可靠性、持续供电能力和自动切换功能使其在各个领域中都有广泛的应用。A型应急照明集中电源不仅提高了建筑物内的安全性,还为人们在紧急情况下提供了明亮之光,为生命安全和财产保护做出了重要贡献。在现代建筑中,A型应急照明集中电源无疑是一项不可或缺的电力设备,为我们的生活和工作环境增添了一份安全和可靠的保障。
引言:
随着科技的不断发展,智能照明系统正逐渐改变着我们的生活和工作环境。智能照明控制器作为这一系统中的关键组件,扮演着重要的角色。智能照明控制器厂家在推动智慧城市、节能环保和舒适生活方面发挥着关键作用。本文将深入探讨智能照明控制器的定义、特点、技术创新以及厂家在智慧照明领域中的重要贡献,以展示它们点亮未来的智慧之光。 智能照明控制器的定义与特点
智能照明控制器是一种设计用于管理和控制照明系统的设备,具有以下关键特点:
远程控制:可以通过智能手机、平板电脑或计算机远程控制照明系统,实现灯光的开关、亮度和颜色的调整。
自动化调节:具备自动化功能,可以根据光线强度、时间表和传感器数据智能调节灯光,实现节能和舒适性。
节能环保:可以有效降低能源消耗,减少碳排放,为可持续发展做出贡献。
场景设置:允许用户创建不同的照明场景,满足不同的需求,如聚会、阅读、工作等。
互联互通:具备互联互通的能力,可以与其他智能家居设备、安全系统和建筑自动化系统集成。
智能照明控制器技术创新
智能照明控制器厂家不断推动技术创新,不仅提高了产品性能,还增加了功能多样性。以下是一些技术创新的示例:
人工智能(AI)集成:利用人工智能算法,智能照明控制器可以学习用户的偏好和行为,自动调整照明设置,提供更个性化的照明体验。
光谱控制:一些控制器可以调整灯光的色温和颜色,以满足不同场景下的需求,如冷暖光、彩色光等。
环境感知:集成环境传感器,能够感知室内光线、温度、湿度等参数,从而更***地调整灯光。
智能调度:基于日出和日落时间、用户活动等因素,智能照明控制器可以自动创建节能的照明调度。
智能照明控制器厂家的应用领域
智能照明控制器厂家的产品广泛应用于各个领域,包括:
家居照明:提供用户舒适、智能化的家居照明体验,实现远程控制和自动化调节。
商业建筑:在办公大楼、商场、餐厅等商业场所实现能效管理和照明舒适度的提升。
城市照明:为智慧城市的街道照明和公共区域提供远程控制和节能管理。
工业和生产:提供工厂和生产线的智能照明解决方案,提高能源效率。
结论
智能照明控制器厂家通过不断创新和提供先进的智能照明解决方案,正在改变我们的生活和工作环境。其产品具备远程控制、自动化调节、节能环保等特点,为用户提供更智能、更舒适、更环保的照明体验。在建筑领域、城市管理和工业生产中,智能照明控制器厂家的产品发挥着关键作用,促进了可持续发展、节能减排和智慧生活的实现。可以说,智能照明控制器厂家是点亮未来的智慧之光,为我们创造了更美好的生活和工作环境。
引言:
在紧急情况下,如火警或电力故障,建筑物内的照明系统仍然需要正常运行,以确保人员的安全疏散和紧急情况的控制。应急照明集中电源箱是一种关键设备,它为建筑物内的应急照明系统提供了稳定的电力供应,保障了人员生命安全。本文将深入探讨应急照明集中电源箱的定义、特点、工作原理以及在建筑安全中的不可或缺作用,以凸显它作为明亮后备力量的重要性。
应急照明集中电源箱的定义与特点
应急照明集中电源箱是一种专门设计用于管理和控制应急照明系统的设备,具有以下关键特点:
电力备用:它为建筑物内的应急照明系统提供备用电力,确保在主电源故障或火警情况下照明系统不中断。
自动切换:应急照明集中电源箱能够自动检测主电源故障并切换到备用电源,实现瞬间过渡,确保连续供电。
持续供电:它具备足够的电力容量,能够支持应急照明系统在紧急情况下长时间运行,以便人员安全疏散和灾害控制。
监测功能:应急照明集中电源箱通常具有电池状态监测和自诊断功能,确保备用电源的可靠性。
应急照明集中电源箱的工作原理
应急照明集中电源箱的工作原理基于以下关键步骤:
主电源监测:它持续监测建筑物的主电源状态。当主电源正常时,应急照明集中电源箱不进行干预。
电力中断检测:如果主电源发生故障或中断,应急照明集中电源箱会立即检测到,并启动备用电源。
备用电源启动:应急照明集中电源箱启动备用电池或发电机,以供应应急照明系统所需的电力。
照明系统供电:一旦备用电源启动,它将为建筑物内的应急照明系统提供稳定的电力,确保照明不中断。
应急照明集中电源箱的应用领域
应急照明集中电源箱的应用领域广泛,包括但不限于:
商业建筑:用于办公大楼、购物中心、酒店等商业场所,确保火警或电力中断时的照明和人员疏散。
医疗设施:在医院、诊所和实验室中使用,保障医疗设备和患者的安全。
工业厂房:用于工厂、生产车间和仓库,确保工人在紧急情况下的安全撤离和设备控制。
交通枢纽:用于机场、地铁站和火车站,保障旅客在火警或停电时的安全。
结论
应急照明集中电源箱是建筑物内应急照明系统的关键组成部分,为紧急情况下的照明需求提供了可靠的电力保障。它的自动切换、持续供电能力和监测功能使其在各个领域中都有广泛的应用。应急照明集中电源箱不仅提高了建筑物内的安全性,还为人们在紧急情况下提供了明亮的后备力量,为生命安全和财产保护做出了重要贡献
标题:智能照明控制器:***智能照明革命
引言:
随着科技的不断进步,智能照明系统正在改变着我们的生活和工作环境。智能照明控制器作为这一系统的核心组成部分,具有***的功能和创新性的设计,为用户提供了更智能、更舒适和更节能的照明体验。本文将深入探讨智能照明控制器的定义、特点、工作原理以及在不同领域中的广泛应用,以展示它们如何***智能照明革命。
智能照明控制器的定义与特点
智能照明控制器是一种专门设计用于管理和控制照明系统的设备,具有以下关键特点:
远程控制:用户可以通过智能手机、平板电脑或计算机远程控制照明系统,实现灯光的开关、亮度和颜色的调整。
自动化调节:具备自动化功能,可以根据光线强度、时间表和传感器数据智能调节灯光,实现节能和舒适性。
节能环保:可以有效降低能源消耗,减少碳排放,为可持续发展做出贡献。
场景设置:用户可以创建不同的照明场景,满足不同需求,如聚会、阅读、工作等。
互联互通:具备互联互通的能力,可以与其他智能家居设备、安全系统和建筑自动化系统集成。
智能照明控制器的工作原理
智能照明控制器的工作原理基于以下关键步骤:
传感器数据收集:控制器通过内置或外部传感器获取环境数据,如光线强度、运动检测、温度等。
智能分析:基于传感器数据和预设的条件,控制器使用智能算法来决定***佳的照明设置。
灯光控制:控制器发送指令到灯光装置,实现对亮度、色温和颜色的调整,以满足用户需求。
远程控制:用户可以通过手机应用或其他界面远程控制控制器,实现照明系统的灵活控制。
智能照明控制器的应用领域
智能照明控制器在各个领域中都有广泛的应用,以下是一些示例:
家居照明:提供用户智能化的家居照明体验,实现远程控制和自动化调节,提高生活舒适度。
商业建筑:在办公大楼、商场、餐厅等商业场所实现能效管理和照明舒适度的提升。
城市照明:用于智慧城市的街道照明和公共区域,提高城市能效和安全性。
工业和生产:提供工厂和生产线的智能照明解决方案,提高能源效率和生产效率。
结论
智能照明控制器不仅提高了照明系统的效率和性能,还为用户提供了更便捷的控制方式。其远程控制、自动化调节、节能环保等特点使其在各个领域中都有广泛的应用。智能照明控制器的不断创新和发展,将继续***智能照明革命,为我们的生活和工作环境带来更多的便利和舒适。可以说,智能照明控制器已经成为现代照明系统中不可或缺的一部分,为未来的智能化生活提供了坚实的基础。
引言:
在各种应急情况下,如火警、停电或突发事件,安全照明系统的稳定运行***关重要,它可以为人员提供安全疏散的必要照明,确保生命和财产的安全。36V应急照明集中电源是一种专门设计用于为安全照明系统提供备用电力的关键设备,它的可靠性和高效性在紧急情况下发挥着关键作用。本文将深入探讨36V应急照明集中电源的定义、特点、应用领域以及厂家在提供安全照明解决方案中的重要角色。
36V应急照明集中电源的定义与特点
36V应急照明集中电源是一种专门设计用于为建筑物内安全照明系统提供备用电力的设备,它具有以下关键特点:
备用电源:在主电源故障或停电情况下,36V应急照明集中电源提供备用电力,确保安全照明系统持续运行。
自动切换:具备自动切换功能,能够在主电源故障时瞬间切换到备用电源,避免任何照明中断。
高电力容量:36V电压提供足够的电力容量,能够支持大规模建筑物内的安全照明系统长时间运行。
电池监测:通常配备电池状态监测功能,确保备用电源的可靠性和及时维护。
36V应急照明集中电源的应用领域
36V应急照明集中电源在各个领域中都有广泛的应用,包括但不限于:
商业建筑:用于办公大楼、购物中心、酒店等商业场所,确保火警或电力中断时的安全照明和人员疏散。
医疗设施:在医院、诊所和实验室中使用,保障医疗设备和患者的安全。
工业厂房:用于工厂、生产车间和仓库,确保工人在紧急情况下的安全撤离和设备控制。
交通枢纽:用于机场、地铁站和火车站,保障旅客在火警或停电时的安全。
36V应急照明集中电源厂家在提供安全照明解决方案中扮演着关键角色。他们的产品不仅需要具备高度的可靠性和稳定性,还需要满足不同应用场景的需求。这些厂家通过不断的研发和创新,提供各种型号的应急照明集中电源,以适应不同规模和复杂度的建筑物。他们还提供售前咨询、定制化解决方案和售后维护,确保安全照明系统始终处于***佳状态。 结论
36V应急照明集中电源是确保建筑物内安全照明系统稳定运行的关键组成部分。其备用电源、自动切换功能和高电力容量使其在各个领域中都有广泛的应用。36V应急照明集中电源厂家通过提供可靠的产品和专业的服务,为建筑安全和人员疏散提供了重要的支持。可以说,他们的工作是保障生命和财产安全的可靠之选,为建筑物提供了在紧急情况下的必要照明保障。
标题:36V应急照明集中电源厂家:安全照明的坚实后盾
引言:
在现代社会,建筑物的安全性和可靠性***关重要。无论是商业大楼、医疗设施、工业厂房还是公共交通枢纽,安全照明系统都是确保人员生命安全和财产保护的重要组成部分。而36V应急照明集中电源厂家的角色就是提供可靠的备用电源,确保在紧急情况下建筑物内的安全照明系统正常运行。本文将深入探讨36V应急照明集中电源厂家的重要性、产品特点以及在建筑安全中的作用。
36V应急照明集中电源厂家的重要性
36V应急照明集中电源厂家在建筑安全领域扮演着***关重要的角色。他们的产品是应急照明系统的核心组成部分,为建筑物提供备用电力,确保在主电源故障或停电时,照明系统仍然可用。以下是他们的重要性体现:
安全性保障:应急照明系统是建筑物内紧急情况下的照明保障,直接关系到人员的生命安全。36V应急照明集中电源厂家的产品可靠性直接影响到这一重要任务的完成。
电力过渡:这些厂家的产品具备自动切换功能,可以在主电源故障时瞬间切换到备用电源,确保照明不中断,帮助人员安全疏散。
稳定供电:36V电压提供了足够的电力容量,能够支持建筑物内的安全照明系统长时间运行,为人员提供持续的照明。
监测维护:厂家通常设计产品带有电池状态监测功能,可以监测备用电源的状态,及时维护,确保系统的可靠性。
36V应急照明集中电源的产品特点
36V应急照明集中电源厂家的产品具有以下特点:
高可靠性:产品经过严格的质量控制和测试,确保在关键时刻可靠运行。
自动切换:具备自动切换功能,实现瞬间过渡,确保连续供电。
高电力容量:36V电压提供了足够的电力,适用于各种规模的建筑物。
监测功能:带有电池状态监测和自诊断功能,确保备用电源的可靠性。
定制化解决方案:厂家通常提供定制化的产品和解决方案,以适应不同建筑物的需求。
36V应急照明集中电源在建筑安全中的作用
36V应急照明集中电源在各个领域中都有广泛的应用,包括但不限于:
商业建筑:确保商业办公楼、购物中心等场所的安全照明,保障火警或电力故障时的人员疏散。
医疗设施:为医院、诊所和实验室提供备用电力,保障医疗设备和患者的安全。
工业和生产:在工厂、生产车间和仓库中应用,确保工人在紧急情况下的安全撤离和设备控制。
交通枢纽:用于机场、地铁站和火车站,确保旅客在火警或停电时的安全。
结论
36V应急照明集中电源厂家的产品在建筑安全中扮演着不可或缺的角色。他们提供的备用电源解决方案确保了建筑物内安全照明系统的稳定运行,为人员生命安全和财产保护提供了坚实的后盾。这些厂家通过不断的创新和提供高可靠性的产品,为建筑物提供了在紧急情况下的必要照明保障,为建筑安全贡献了重要的力量。可以说,他们的工作是保障生命和财产安全的可靠之选。
推荐阅读:
ACB抽屉式框架断路器
应急照明配电箱厂家:安全电力的守护者
A型应急照明集中电源:安全保障与高效管理